
Construction machines have evolved in recent years, with significant advances in engines and power systems in particular and this has been seen amongst all equipment types, including soil compactors.
New generation engines are more fuel efficient and quieter, while offering greater power density. More importantly, new generation engines are also cleaner in operation, producing far lower levels of emissions. In Europe and the US, the stringent requirements have resulted in diesels that are far cleaner, with other markets now looking to follow suit and adopt similar rules. Meanwhile, visibility from the cab is a key safety issue for all machine types and here also, manufacturers have made significant advances in providing better sight lines for operators of soil compactors.
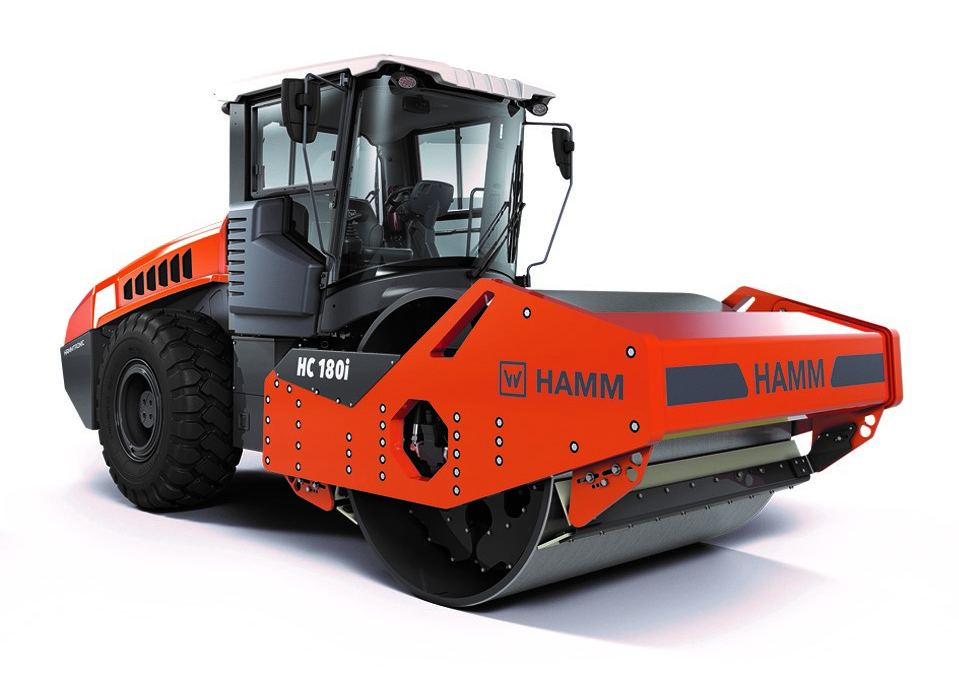
Machine control systems from the leading suppliers can now be used with soil compaction machines to make operations more efficient, reducing compaction time and fuel consumption, while boosting productivity and ensuring quality is optimised. The further move for the market will be the introduction of autonomous soil compaction machines, with prototype systems having already been developed, trialled and demonstrated to the industry.
Moving back down to earth somewhat however, key manufacturers re unveiling several new models.
From Ammann come the new ARS 30 and ARS 50 compact single drum rollers, which are said to deliver high output despite their size. The ARS 30 weighs in at 3tonnes, while the ARS 50 weighs in at 5tonnes and these are now the most compact soil compaction machines from the firm.
The novel design features hydrostatic drive and has allowed the firm to do away with the need for a rear axle. As a result, the engines are mounted low in the chassis, which has lowered the centre of gravity and is of benefit when using the units on slopes, while also allowing better sight lines from the cab.
Operator comfort is said to be good and both machines have adjustable seats and vibration-isolated platforms. They are also said to be easy to operate with a tough dashboard able to cope with arduous construction applications as well as a multifunctional control display.
Of note is that the drums are designed to be maintenance-free, reducing the cost of ownership.
Rival firm BOMAG meanwhile says that its latest soil compactors can deliver high amplitudes as well as ensuring compaction forces reach greater depths than for earlier models. The firm offers variants with smooth and padfoot drums. The latter can be used for compacting cohesive soils, with profiles that penetrate deeply into the ground.
The high-torque drives and high gradeability allow operation on difficult and uneven terrain. Meanwhile, multiple discs in the front drum are said to ensure effective braking.
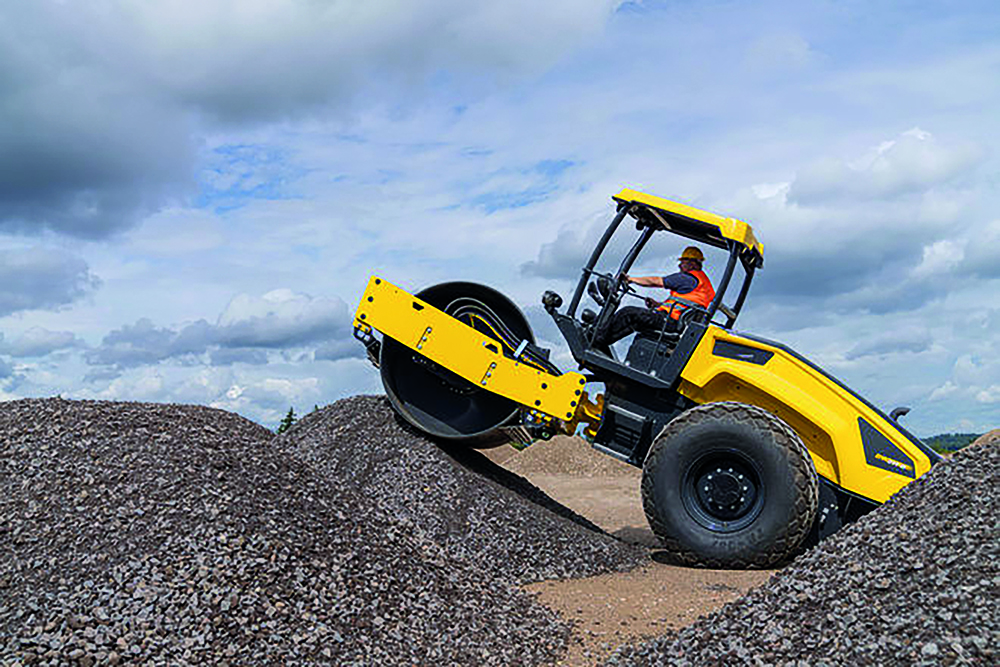
The cabs are said to be ergonomic and offer a good view to the front and rear, as well as of the drum, while the controls are said to be easy to use.
The firm says that its Smart Line single drum rollers are durable and versatile and can be used in a range of applications. Maintenance is said to be straightforward with grouped service points that are easy to access.
The firm also says that the machines have been developed to work in tough conditions, such as ambient temperatures up to 50°C. A novel feature is the ability to interface with the Bomap app for tablets and smartphones.
These machines are available in Tier 2 versions as well as Tier 3 and Tier 4 Final/Stage V compliant variants, meeting the demands of different global market requirements.
From Dynapac comes an extension to its offering of soil compactors featuring the innovative SEISMIC system. The new CA3500D SEISMIC roller retains the proven features of the CA3500 model but now features the sophisticated SEISMIC compaction system as well.
This technology allows automatic optimisation of drum frequency for any surface to compacted. The onboard machine control unit and compaction meter work in combination, allowing the SEISMIC system to sense dynamic characteristics of the surface to be compacted and then calculate the optimum drum frequency. The process uses data from the SEISMIC Compaction Meter in the onboard machine control, which regulates the hydraulics. With this system, the SEISMIC package can determine the resonant frequency of the soil automatically. Using this system ensures that the correct compaction forces exactly are delivered where required. In addition, the system can change the drum frequency every 0.2 seconds to ensure maximum performance. As the drum performance is matched to the ground parameters, it delivers the required compaction force, while also saving time and fuel.
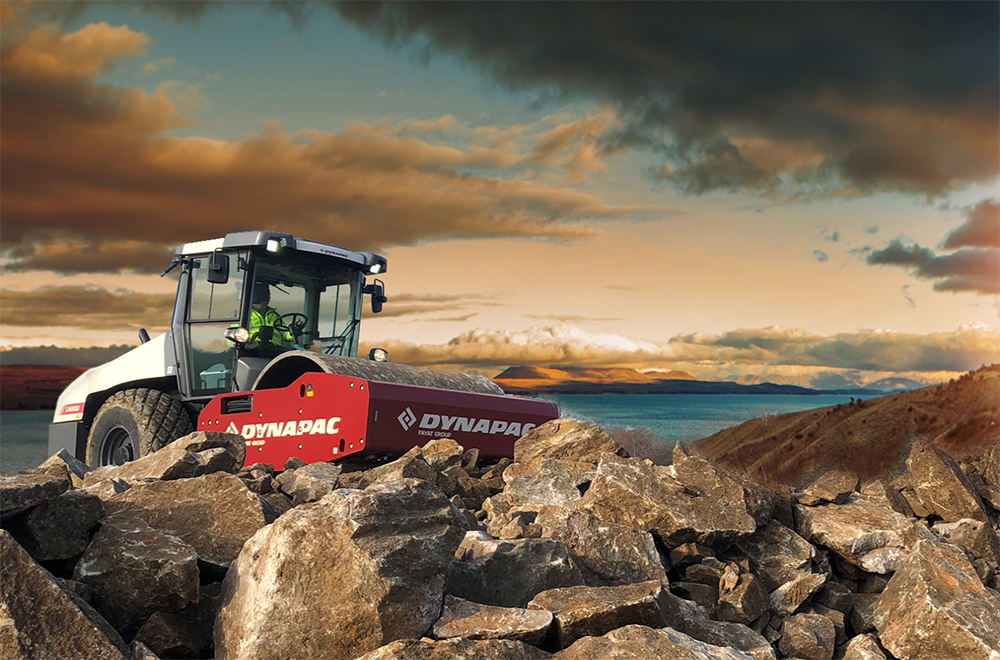
The system can help to boost productivity onsite, while reducing the number of passes required. The package also eliminates the risk of over- or under-compaction. The firm claims that fuel consumption can be reduced by up to 55%, while productivity can be boosted by up to 40%. Due to lower frequencies, noise levels are also reduced while operating at lower frequencies also helps to reduce maintenance needs for the machine.
With this introduction, the SEISMIC feature is now available for Dynapac soil compactors ranging from the 7tonne CA1500 to the 21tonne CA6500 model.
Key benefits of the new HC Series soil compactors from Hamm are increased compaction forces. The new models are said to generate up to 15% more centrifugal force than the firm’s earlier generation models.
Operating weights range from 11-25tonnes while engine power outputs are from 85-160kW. However, the machines have new ECO modes that are said to ensure these models are more efficient than previous generation units. from the company. The new machines can operate in partial load mode unless more output is required, saving fuel.
The cabs are larger, with better visibility and lower vibration levels for the operator than on the earlier models. A wide array of options is available including an automatic engine stop system and a dozer blade, while CR variants with reinforced drums for use on rocky ground will be available in due course.