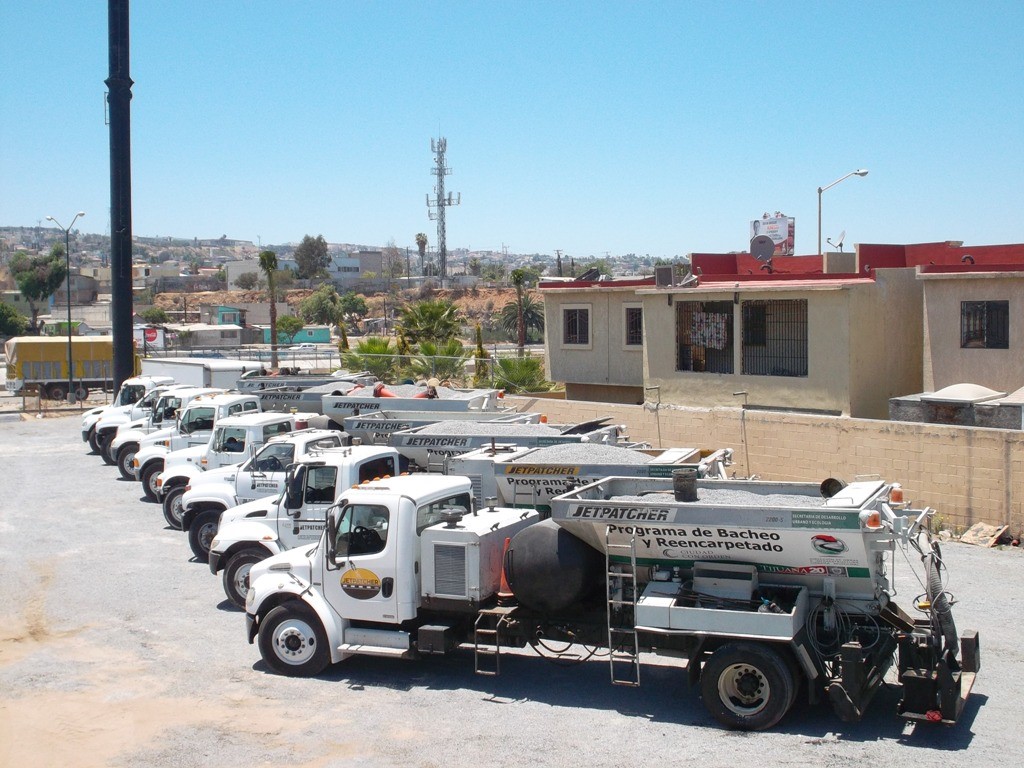
UK-based Jetpatcher reports that it has just shipped four more Jetpatcher kits to their partners in Mexico, making a total 110 shipped to date.
The kits include all the proprietary control systems as well as the company’s ‘Spreader Box’ attachment for localised sheet patching applications. The units are made entirely in Jetpatcher’s new factory in Rugby, northern England. The company says that its heavy investment in laser technology, fabrication and self-sufficient energy from a huge solar bank ensures a smoother, faster and greener process all round.
Jetpatcher offer a range of machines in various size from 1m2 up to 8m2 that can be operated from trailers or 7.5tonne vehicles all the way up to a 26tonne chassis.
Jetpatcher Mexico is one of the company’s several global, strategic manufacturing hubs, along with ones in India, South Africa and Europe. The company says that because the hubs are run by local people, with all their expertise and knowledge of the area’s specific needs, they can react faster when called upon for the perfect solution.
Most of the equipment has been sold to municipal and state governments, explains Saúl Arauzo, managing director and owner of Jetpatcher Mexico. “There are government entities that have up to six Jetpatchers in operation. However, great interest has also been shown by private sector companies, some with up to 12 Jetpatcher units for the maintenance of asphalt roads.”
Jetpatcher’s first units for Mexico arrived in the country for demonstrations and work in 2001 followed in 2002 by the first maintenance contract for municipal roads. The next year, 2003, saw official registration of the company Jetpatcher Mexico and the sale of the first five units.
Jetpatcher machines use high velocity air to prepare the area of the defect and to deliver emulsion and aggregate to seal, fill and compact the repair. The company says that this results in a quality repair that takes very little time, avoids further damage to the road base and is more economical than conventional repairs.
Jetpatcher also says that its units are the only machinery that uses a specialised distributor system which allows it to provide high production rates with little wear, as there are no moving parts. This eliminates costly maintenance time for the for the operators.
Since 1987 when the first Jetpatcher unit was built in New Zealand by Jim Turnbull, more than 650 units have been sold worldwide. The company was purchased by its UK distributor in 2016 and now has its global headquarters in Rugby, England.
The company says that it was instrumental in the creation of the UK’s BS 10947 standard which states that spray injection patching is suitable for several treatments. These include emergency and temporary patching repairs, pre-patching for surface dressing and slurry surfacing, localised preventative maintenance and also permanent patching repairs.
Spray injection patching is suitable for local and strategic roads, hard shoulders, motorways (temporary but can be permanent where located out the wheel path) and hard running untrafficked strips.