WJ’s latest innovation is a method of road stud installation designed to remove vulnerable operatives from the carriageway
The bespoke design of the WJ Guardian system allows the complete road stud installation process to take place while protecting operatives within an integrated safety cell of an 18tonne truck.
The UK has used 12 million road studs on its national and local road network, all requiring maintenance or replacement at some point. Traditional methods of installation by hand or milling ma
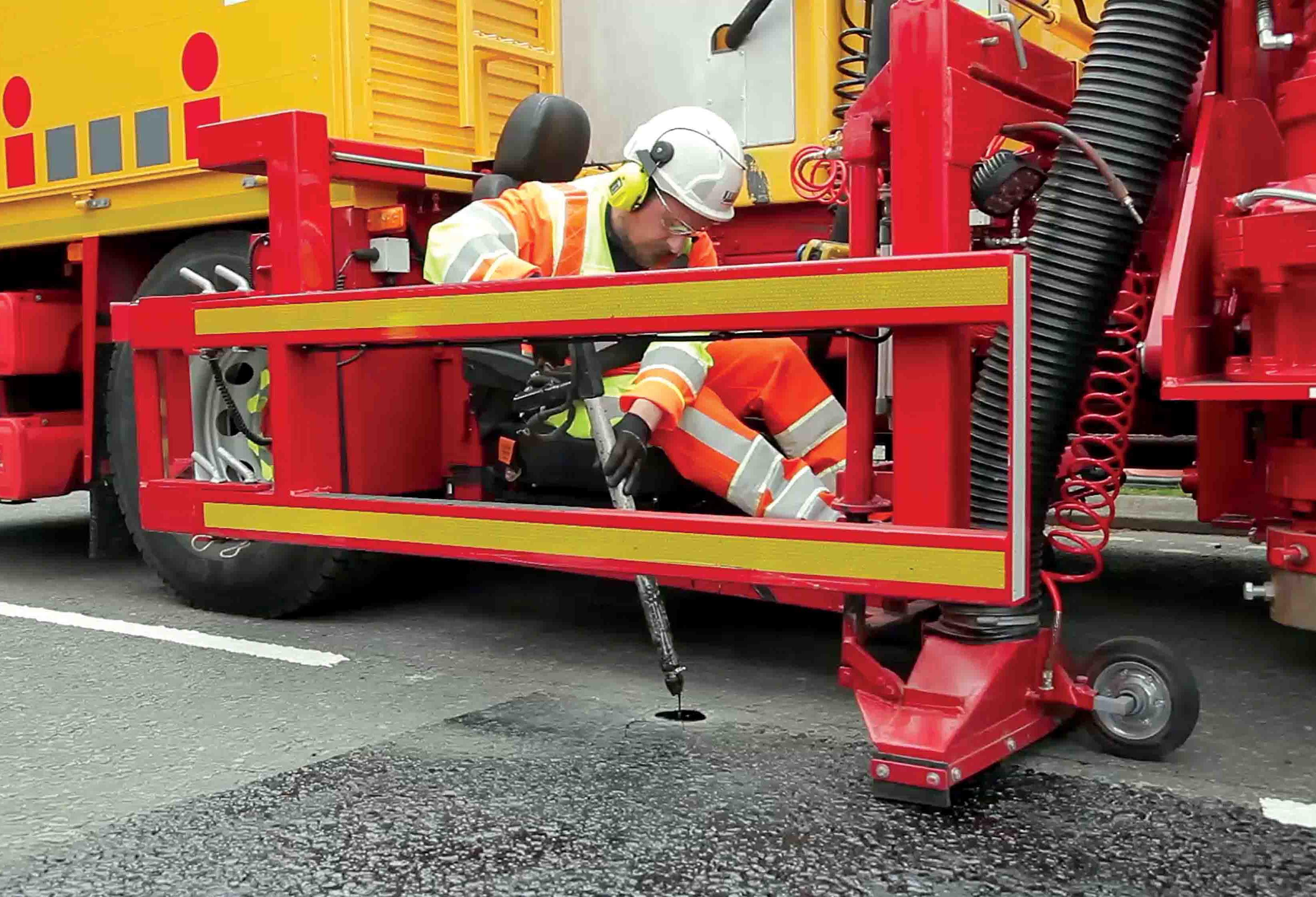
Installation operatives out of harm's way
WJ’s latest innovation is a method of road stud installation designed to remove vulnerable operatives from the carriageway
The bespoke design of the8037 WJ Guardian system allows the complete road stud installation process to take place while protecting operatives within an integrated safety cell of an 18tonne truck.
The UK has used 12 million road studs on its national and local road network, all requiring maintenance or replacement at some point. Traditional methods of installation by hand or milling machine require operatives to be in the centre of the carriageway and, therefore, at risk of injury while working within live traffic conditions.
That risk varies from site to site, but always with a need for safety zones, either stop/stop type traffic management or road closures, to comply with the regulatory requirements.
The WJ Guardian method does not negate this need for safety zones, but it does significantly reduce the actual safe work zone required. The method ensures that the operatives do not need to stand and operate equipment from the opposite carriageway to the vehicle. Instead, they are protected within the vehicle’s safety cell as well as within a regulated safety zone.
The development provides designers with the potential to eliminate a substantial number of road closures and reduce disruption within communities close to the work. WJ’s recent development focus has been on designing out risk through engineering and using its road marking vehicles as a protective safety barrier (see box). The patent pending WJ Guardian road stud installation technology is Phase 2 of a development project led by WJ’s engineering division in Elland, West Yorkshire in the UK.
With computer-aided design (CAD) software, phase 1 involved development of a lateral moving milling head so the installation vehicle would not need to straddle the centre of the road. CAD was used to simulate and validate the mechanical and physical properties of the design, ensuring that a legally compliant, robust and safe process was achieved even before component parts were manufactured and the truck was built.
Phase 2 involved the full design of a specialist installation vehicle with a protected control hub cell integrated within the chassis. It was important that a side under run device used fully complied with stringent requirements within the UK’s statutory Individual Vehicle Approval (IVA) scheme. From this safe position, the road operative activates the drill, vacuums up debris, applies hot bitumen grout and places the road stud before the driver of the vehicle moves onto the next position.
The Guardian system can be used to install all types of road studs. But, it was with this process in mind that WJ also developed the BSEN 1463 approved Allux prismatic road stud complete with stabilising shank.
WJ enthusiastically engage and share best practice in this way with clients, the5149 Road Safety Markings Association (RSMA) and other stakeholders to establish the best work-related health and safety practice. Many of WJ’s ideas have contributed to improvements across the highways industry.
George Lee, chief executive of the UK’s Road Safety Markings Association, said the system was “a real step change in road worker safety”.
WJ is in the process of retrofitting operator platforms to many of their standard studding rigs so that a measure of safety can be extended to other operatives.
The bespoke design of the
The UK has used 12 million road studs on its national and local road network, all requiring maintenance or replacement at some point. Traditional methods of installation by hand or milling machine require operatives to be in the centre of the carriageway and, therefore, at risk of injury while working within live traffic conditions.
That risk varies from site to site, but always with a need for safety zones, either stop/stop type traffic management or road closures, to comply with the regulatory requirements.
The WJ Guardian method does not negate this need for safety zones, but it does significantly reduce the actual safe work zone required. The method ensures that the operatives do not need to stand and operate equipment from the opposite carriageway to the vehicle. Instead, they are protected within the vehicle’s safety cell as well as within a regulated safety zone.
The development provides designers with the potential to eliminate a substantial number of road closures and reduce disruption within communities close to the work. WJ’s recent development focus has been on designing out risk through engineering and using its road marking vehicles as a protective safety barrier (see box). The patent pending WJ Guardian road stud installation technology is Phase 2 of a development project led by WJ’s engineering division in Elland, West Yorkshire in the UK.
With computer-aided design (CAD) software, phase 1 involved development of a lateral moving milling head so the installation vehicle would not need to straddle the centre of the road. CAD was used to simulate and validate the mechanical and physical properties of the design, ensuring that a legally compliant, robust and safe process was achieved even before component parts were manufactured and the truck was built.
Phase 2 involved the full design of a specialist installation vehicle with a protected control hub cell integrated within the chassis. It was important that a side under run device used fully complied with stringent requirements within the UK’s statutory Individual Vehicle Approval (IVA) scheme. From this safe position, the road operative activates the drill, vacuums up debris, applies hot bitumen grout and places the road stud before the driver of the vehicle moves onto the next position.
The Guardian system can be used to install all types of road studs. But, it was with this process in mind that WJ also developed the BSEN 1463 approved Allux prismatic road stud complete with stabilising shank.
WJ enthusiastically engage and share best practice in this way with clients, the
George Lee, chief executive of the UK’s Road Safety Markings Association, said the system was “a real step change in road worker safety”.
WJ is in the process of retrofitting operator platforms to many of their standard studding rigs so that a measure of safety can be extended to other operatives.