Safety restraints have come a long way in the past 20 years. But perfection has its drawbacks, notes Thomas Edl, head of barrier manufacturer Delta Bloc. In Europe, establishing regulations for construction and testing of road restraints has been complex. But the journey has been worthwhile in terms of lives saved, says Thomas Edl, managing director of Delta Bloc International, based in Vienna. The European Commission looked at this and decided that there should be regulations to make it an even playing fie
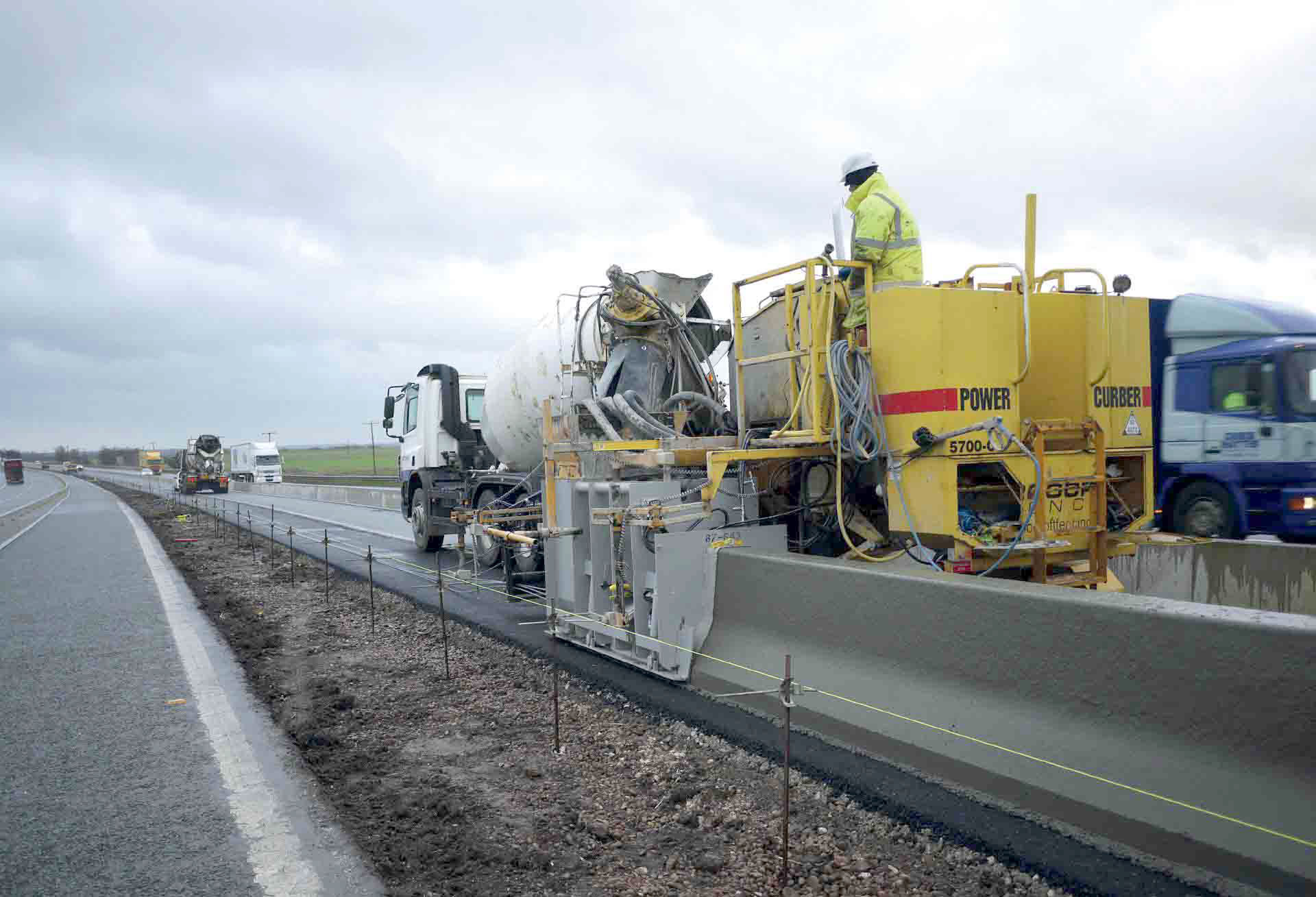
The wear life of cables in extruded barriers needs to be considered
Safety restraints have come a long way in the past 20 years. But perfection has its drawbacks, notes Thomas Edl, head of barrier manufacturer Delta Bloc
In Europe, establishing regulations for construction and testing of road restraints has been complex. But the journey has been worthwhile in terms of lives saved, says Thomas Edl, managing director of4017 Delta Bloc International, based in Vienna.
The European Commission looked at this and decided that there should be regulations to make it an even playing field for manufacturers across Europe. Hence, the adoption of CE certification EN1317, part 5, says Edl.
“It was a wake-up call for manufacturers and clients,” says Edl, who joined Delta Bloc in 2005 and has been managing director since 2007. He also holds a PhD in construction engineering material, specifically glass and timber, from Holzforschung Austria – the Austrian Forest Products Research Society. By his own admission, he’s a “technical person who has moved from glass and timber into concrete”.
Manufacturers such as Delta Bloc rose to the challenge created by the adoption of CE certification for in situ concrete barriers (so-called passive safety systems), several years ago. "From our point of view it was a positive move for the market. It forced manufacturers to invest in new technology. If the European Commission had not clarified this, the technology would have stayed the same for the next decade. Now there is an incentive for manufacturers to improve their product. That means only safe-proven in situ concrete barriers are used on roads. It pushes the industry to develop new systems.”
Delta Bloc is now manufacturing around 200km of CE certified concrete barriers a year and this will increase, he says. “Suddenly manufacturers were coming out with different shapes and heights and the market quickly moved on. For example, we have slipform in situ concrete barriers where the internal reinforced steel cable is corrosion resistant and the barriers themselves have a 50-year lifespan.”
Many European local authorities and highways agencies are now looking at regulations regarding transitional barriers and how they connect to other types of barrier. What is the joint or connect like and is it a safety weak point in today’s continuous safety barrier?
Manufacturers are putting a lot of work into the physical design of connections, including simulation and real-life crash testing, and not only from a single direction, that of the anticipated vehicle impact. Germany and France have the toughest regulations for transition sections and their connections. But there is as yet no pan-European harmonisation of this process and connection. “One country requires a crash test and another country requires a simulation. It’s still a tricky situation,” says Edl.
For the past 20 years, the standard across most of Europe has been an H2 containment level for concrete central reservation crash barrier performance. This means a barrier should stop a 13tonne bus. In the first decade of those 20 years, barriers performed better and better, many times reaching beyond H2 and sometimes nearly H3 – the ability to stop a 16tonne truck. Once that peak was achieved, manufacturers started to optimise the product by making it less expensive to make, and so to purchase.
On the one hand, that is good. But by optimising for a very specific safety requirement, in reality there was a downgrading of performance, explains Edl. Barriers still achieve H2 level, but often gone is that added margin of safety, or reserve safety, whereby in some situations the barrier might also perform greater than its regulation level of H2.
“Everybody is optimising. But some local authorities believe that perfecting the H2 barrier has led to less safety on the roads.”
Edl believes that the next driver for innovation is the search by local authorities for higher containment levels as standard along long stretches of highway. In some markets, the normal safety level might be raised from H2 to even H4b – the maximum level, a 38tonne truck - to regain that lost reserve safety. “The trend is that H4b will replace H2 as the standard barrier in the central reservation along long stretches of highway. So this is another wake-up call for manufacturers, to make H4b barriers as efficiently as we’ve been making H2 barriers.”
Delta Bloc is in the forefront, he says, and has brought down manufacturing costs for H4b barriers, allowing them to be sold in high volumes to suit clients. “We have developed new H4b barriers that will soon be on the market.”
In Europe, establishing regulations for construction and testing of road restraints has been complex. But the journey has been worthwhile in terms of lives saved, says Thomas Edl, managing director of
The European Commission looked at this and decided that there should be regulations to make it an even playing field for manufacturers across Europe. Hence, the adoption of CE certification EN1317, part 5, says Edl.
“It was a wake-up call for manufacturers and clients,” says Edl, who joined Delta Bloc in 2005 and has been managing director since 2007. He also holds a PhD in construction engineering material, specifically glass and timber, from Holzforschung Austria – the Austrian Forest Products Research Society. By his own admission, he’s a “technical person who has moved from glass and timber into concrete”.
Manufacturers such as Delta Bloc rose to the challenge created by the adoption of CE certification for in situ concrete barriers (so-called passive safety systems), several years ago. "From our point of view it was a positive move for the market. It forced manufacturers to invest in new technology. If the European Commission had not clarified this, the technology would have stayed the same for the next decade. Now there is an incentive for manufacturers to improve their product. That means only safe-proven in situ concrete barriers are used on roads. It pushes the industry to develop new systems.”
Delta Bloc is now manufacturing around 200km of CE certified concrete barriers a year and this will increase, he says. “Suddenly manufacturers were coming out with different shapes and heights and the market quickly moved on. For example, we have slipform in situ concrete barriers where the internal reinforced steel cable is corrosion resistant and the barriers themselves have a 50-year lifespan.”
Many European local authorities and highways agencies are now looking at regulations regarding transitional barriers and how they connect to other types of barrier. What is the joint or connect like and is it a safety weak point in today’s continuous safety barrier?
Manufacturers are putting a lot of work into the physical design of connections, including simulation and real-life crash testing, and not only from a single direction, that of the anticipated vehicle impact. Germany and France have the toughest regulations for transition sections and their connections. But there is as yet no pan-European harmonisation of this process and connection. “One country requires a crash test and another country requires a simulation. It’s still a tricky situation,” says Edl.
For the past 20 years, the standard across most of Europe has been an H2 containment level for concrete central reservation crash barrier performance. This means a barrier should stop a 13tonne bus. In the first decade of those 20 years, barriers performed better and better, many times reaching beyond H2 and sometimes nearly H3 – the ability to stop a 16tonne truck. Once that peak was achieved, manufacturers started to optimise the product by making it less expensive to make, and so to purchase.
On the one hand, that is good. But by optimising for a very specific safety requirement, in reality there was a downgrading of performance, explains Edl. Barriers still achieve H2 level, but often gone is that added margin of safety, or reserve safety, whereby in some situations the barrier might also perform greater than its regulation level of H2.
“Everybody is optimising. But some local authorities believe that perfecting the H2 barrier has led to less safety on the roads.”
Edl believes that the next driver for innovation is the search by local authorities for higher containment levels as standard along long stretches of highway. In some markets, the normal safety level might be raised from H2 to even H4b – the maximum level, a 38tonne truck - to regain that lost reserve safety. “The trend is that H4b will replace H2 as the standard barrier in the central reservation along long stretches of highway. So this is another wake-up call for manufacturers, to make H4b barriers as efficiently as we’ve been making H2 barriers.”
Delta Bloc is in the forefront, he says, and has brought down manufacturing costs for H4b barriers, allowing them to be sold in high volumes to suit clients. “We have developed new H4b barriers that will soon be on the market.”