Leading highway work zone safety solution manufacturers have developed innovative new systems offering greater utility and efficiency for work crews involved in vital highways’ projects. Guy Woodford reports
Mobile Barriers is now offering its MBT-1 barrier with cranes, scissor lifts, camera-communication towers and other options to enhance the system’s utility and efficiency.
“This has been largely client driven and an outgrowth of our ongoing development for the transportation and security/defence s
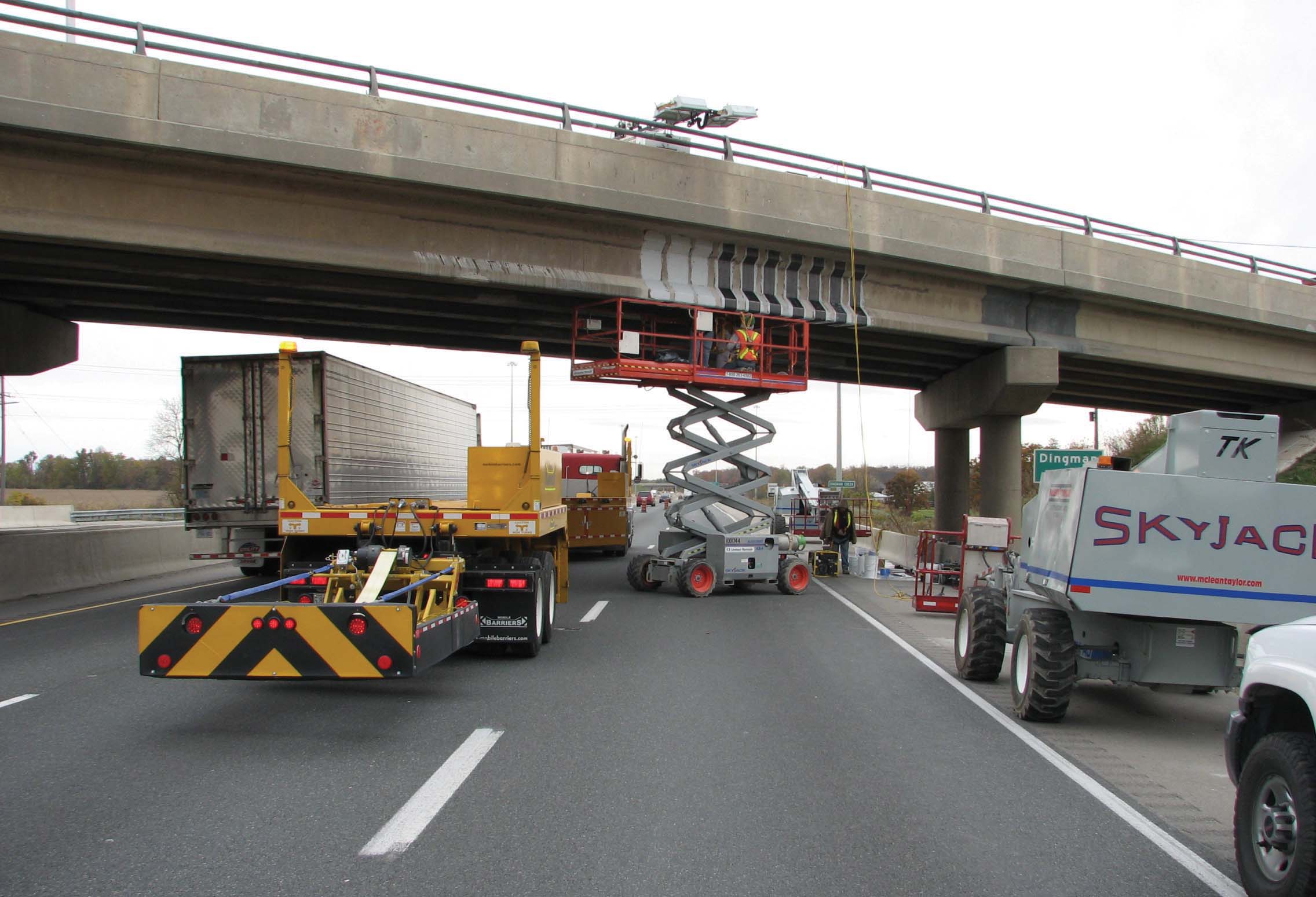
Mobile Barriers 1: The MBT-1 mobile barrier with scissor lift being used near London in Ontario, Canada
Leading highway work zone safety solution manufacturers have developed innovative new systems offering greater utility and efficiency for work crews involved in vital highways’ projects. Guy Woodford reports
6724 Mobile Barriers is now offering its MBT-1 barrier with cranes, scissor lifts, camera-communication towers and other options to enhance the system’s utility and efficiency.
“This has been largely client driven and an outgrowth of our ongoing development for the transportation and security/defence sectors,” said Kevin Groeneweg, CEO of US-based Mobile Barriers. “The MBT-1 incorporates strong platforms upon which this additional equipment and materials can be carried. The barriers are already being used with this equipment in the protected area. By moving the equipment to the platforms, we open up the work area and enable the tasks to be performed directly from the barrier on a highly mobile, highly efficient basis.”
One of the first crane applications was deployed by Powell Construction/Powell Mobile Barriers (PC-PMB), a Mobile Barriers affiliate in Ontario, Canada. PC-PMB were said to have liked the mobility, protection and carry capacity of the MBT-1 but needed assistance lifting, removing and replacing some of the poles and heavier materials they were dealing with. A 2.3tonne crane was added on one of the platforms. “Crews can use it to remove and replace poles, lift and position guardrail, and move other materials to and from the decks,” Groeneweg noted. “We are now looking at even larger cranes to lift and position steel and concrete barrier and other materials. The latest cranes can lift up to five tonnes and reach out nine metres. That’s enough to reach either platform and assist with removal and positioning of materials in a well-lit, protected area.”
Groeneweg said tunnel applications are driving the lift options. “Some [contractors] estimate 70% of their tunnel work involves overhead applications. Tunnels are inherently tight and doing work while keeping traffic moving is a challenge. The MBT-1 allows for a relatively small but highly mobile, highly integrated footprint. The barrier already carries power, lights, signage and TMA. Adding a scissor lift on one of the platforms gives crews the necessary overhead access with improved safety, better mobility and less impediment to traffic. Lights, ventilation, cameras and other equipment can be accessed and meaningful work can be done at night and off-traffic times with little or no set-up.” Launched at the end of 2013, the MPS 350X highway work zone solution from7402 Trinity Highway Products is an upgraded version of the original MPS 350, developed back in 1995.
Trinity Highways engineers have improved the non-structural mechanical and electrical systems as well as the aesthetics of the MPS 350X. The result is a fresh-looking, compact, galvanised, cantilevered truck-mounted attenuator that maintains all NCHRP Report 350 Test Level 3 mandatory and optional testing certification. It also maintains the British high speed standard TD 49 (tested at 110km/h). The upgraded unit is made of galvanised steel components with an open design which allows for easy inspection and maintenance and less wind resistance when travelling in the upright position. The MPS 350X lifting mechanisms are said to have been analysed and improved using state-of-the-art Finite Element Analysis (FEA) and Compute Simulation to improve long-term robustness.
The heavy-duty Durashell strike plate cover provides nuisance hit protection and a warning buzzer alerts highway work crews when the unit is not fully deployed or in the upright position.
More attachment methods were developed such as Socket Hitch receivers and fast deployment Tailgate Mounts. When impacted according to NCHRP Report 350 testing criteria, the unit’s debris field is said to be contained and easy to clean up.
“This has been largely client driven and an outgrowth of our ongoing development for the transportation and security/defence sectors,” said Kevin Groeneweg, CEO of US-based Mobile Barriers. “The MBT-1 incorporates strong platforms upon which this additional equipment and materials can be carried. The barriers are already being used with this equipment in the protected area. By moving the equipment to the platforms, we open up the work area and enable the tasks to be performed directly from the barrier on a highly mobile, highly efficient basis.”
One of the first crane applications was deployed by Powell Construction/Powell Mobile Barriers (PC-PMB), a Mobile Barriers affiliate in Ontario, Canada. PC-PMB were said to have liked the mobility, protection and carry capacity of the MBT-1 but needed assistance lifting, removing and replacing some of the poles and heavier materials they were dealing with. A 2.3tonne crane was added on one of the platforms. “Crews can use it to remove and replace poles, lift and position guardrail, and move other materials to and from the decks,” Groeneweg noted. “We are now looking at even larger cranes to lift and position steel and concrete barrier and other materials. The latest cranes can lift up to five tonnes and reach out nine metres. That’s enough to reach either platform and assist with removal and positioning of materials in a well-lit, protected area.”
Groeneweg said tunnel applications are driving the lift options. “Some [contractors] estimate 70% of their tunnel work involves overhead applications. Tunnels are inherently tight and doing work while keeping traffic moving is a challenge. The MBT-1 allows for a relatively small but highly mobile, highly integrated footprint. The barrier already carries power, lights, signage and TMA. Adding a scissor lift on one of the platforms gives crews the necessary overhead access with improved safety, better mobility and less impediment to traffic. Lights, ventilation, cameras and other equipment can be accessed and meaningful work can be done at night and off-traffic times with little or no set-up.” Launched at the end of 2013, the MPS 350X highway work zone solution from
Trinity Highways engineers have improved the non-structural mechanical and electrical systems as well as the aesthetics of the MPS 350X. The result is a fresh-looking, compact, galvanised, cantilevered truck-mounted attenuator that maintains all NCHRP Report 350 Test Level 3 mandatory and optional testing certification. It also maintains the British high speed standard TD 49 (tested at 110km/h). The upgraded unit is made of galvanised steel components with an open design which allows for easy inspection and maintenance and less wind resistance when travelling in the upright position. The MPS 350X lifting mechanisms are said to have been analysed and improved using state-of-the-art Finite Element Analysis (FEA) and Compute Simulation to improve long-term robustness.
The heavy-duty Durashell strike plate cover provides nuisance hit protection and a warning buzzer alerts highway work crews when the unit is not fully deployed or in the upright position.
More attachment methods were developed such as Socket Hitch receivers and fast deployment Tailgate Mounts. When impacted according to NCHRP Report 350 testing criteria, the unit’s debris field is said to be contained and easy to clean up.