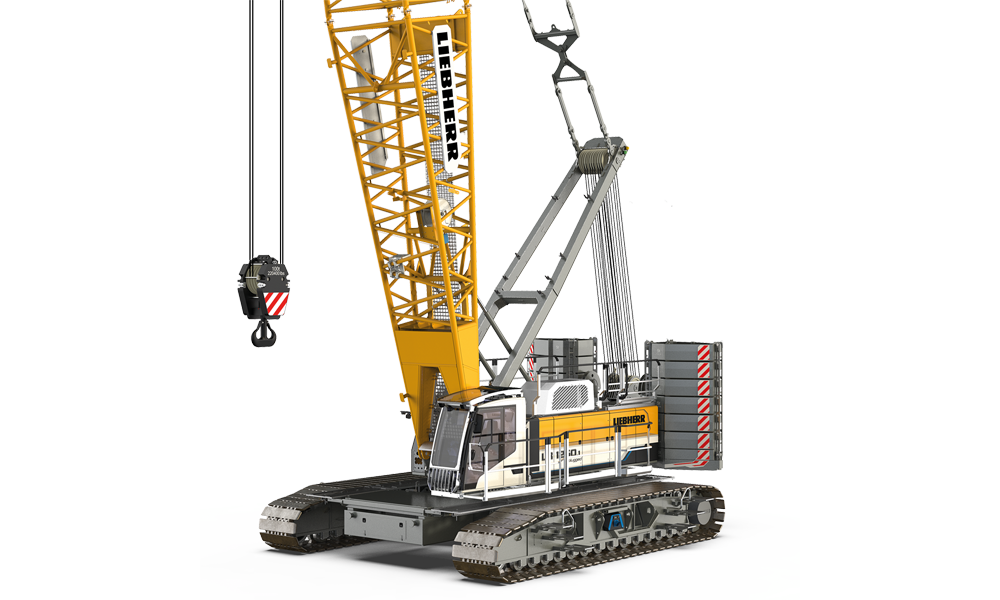
The LR 1200.1 unplugged and the LR 1250.1 unplugged are said to be the world’s first battery-powered crawler cranes. Both are driven by 255kW electric motors and can be used in aggregates production in a dragline configuration or for bridge and overpass construction duties for example.
The models have been introduced along with Liebherr’s new LRB 23 compact piling and drilling rig.
The LR 1200.1 unplugged has a maximum lifting capacity of 200tonnes, and the LR 1250.1 lifts 250tonnes. Liebherr stresses that the two claimed ground-breaking battery-powered crawler cranes come with no compromises regarding performance or availability when compared with the conventional versions.
The new machines are emission-free and have a very low noise level. That is a huge advantage in areas sensitive to noise and also for the people working on the job site.
The cranes can be recharged on a conventional Job site electric supply (32A, 63A) in 4.5 hours and optionally with 125A in 2.25 hours. The capacity of the battery is designed for four hours of lifting operation and the cranes can be operated without a cable due to the battery-electric drive design.
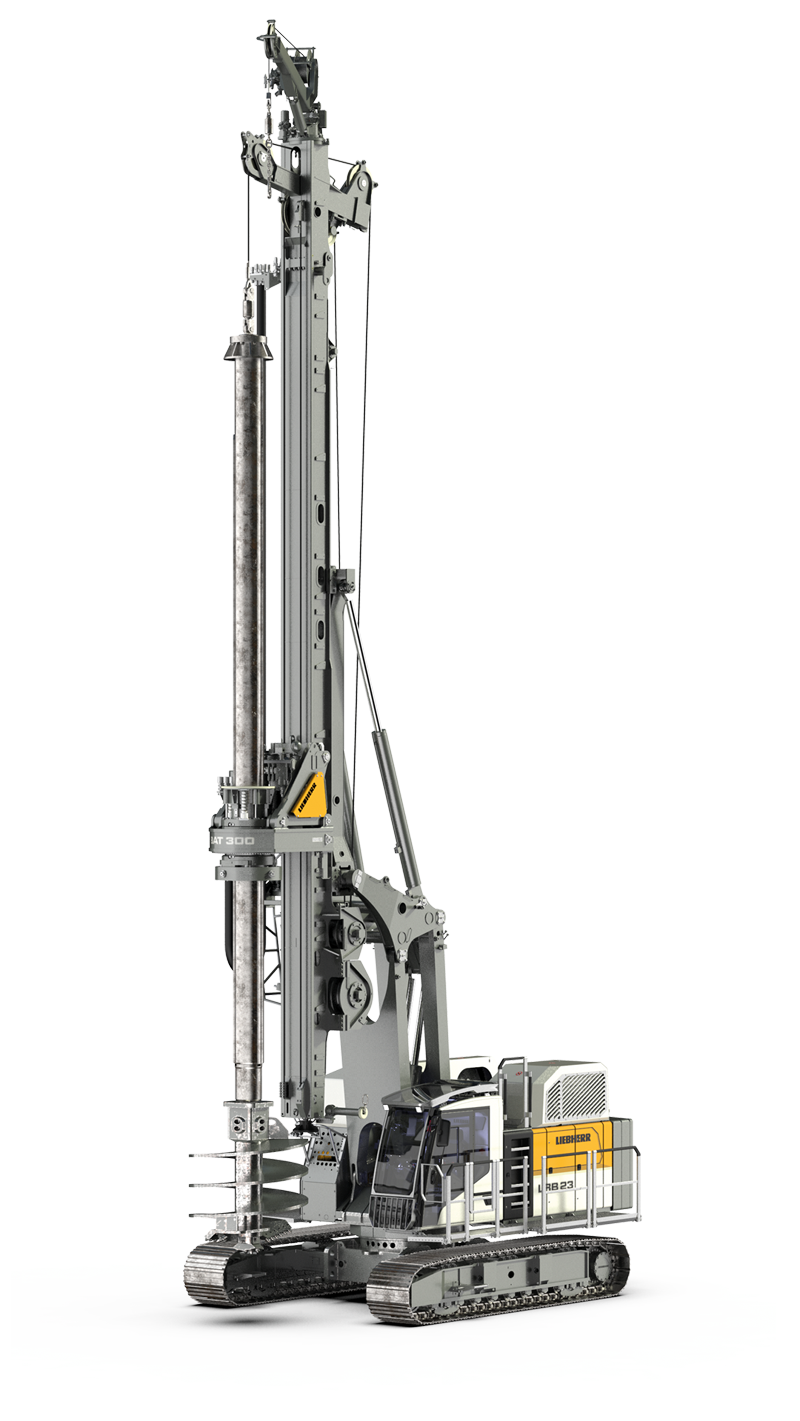
Meanwhile, the compact piling and drilling rig type LRB 23 closes the gap between the LRB 16 and the proven LRB 355.
The new all-rounder for deep foundation work offers an impressive engine output of 600kW and so delivers the necessary capacity for all common deep foundation work, such as drilling with a Kelly drill, double rotary drill, full displacement equipment and continuous flight auger, as well as soil mixing and applications with a vibrator or hydraulic hammer.
Its compact design allows for transportation of the LRB 23 in one piece, so simplifying mobilisation between job sites. The remote control simplifies the loading process for transport as well as the assembly of the machine.
The advantages of the rigid leader are proven and as it can withstand high torques, Kelly drilling is possible. The rotary drive BAT 300 delivers a maximum torque of 300kNm. Locking of the Kelly bar’s telescopic sections is aided by a visualisation system in the LRB 23. The operator is permanently informed about the actual distance to the next locking recess. Colour indications inform when the bar can be locked. False positioning of the Kelly bar during the shake-off process is indicated by a warning signal.
During continuous flight auger drilling, the concreting process is automated by the drilling assistant. All assistance systems contribute to time savings, higher machine availability and an increase in operating safety.