
The Fehmarn Belt Tunnel could open by mid-2029, partly due to two robotic welding machines that have accelerated production of reinforcement steel for tunnel elements.
Around 1,500 tonnes of reinforcement for casting the concrete tunnel elements are produced weekly for the 17.6km-long structure. The individual elements will eventually be lowered into place and connected together on the bottom of the Baltic Sea, according to the client Femern, part of the 100 per cent state-owned company Sund & Bælt. Femern is tasked with planning, building and operating the fixed link across the Fehmarnbelt between Denmark and Germany.
The steel work is so critical that a separate steel production hall was set up in 2023 on the main construction site in Rødbyhavn on the Danish island of Lolland. The hall, called the Panel Factory, covers about 13,000m² of the construction site and employs around 120 workers working in two shifts. This allows the team behind the Panel Factory to deliver about 1,500 tonnes of processed steel to the rest of the construction site each week.
The steel processing hall has the great advantage of allowing steel to be cut to the precise sizes needed. This reduces waste and simultaneously strengthens the supply security for the project by producing steel grids to size and on demand.
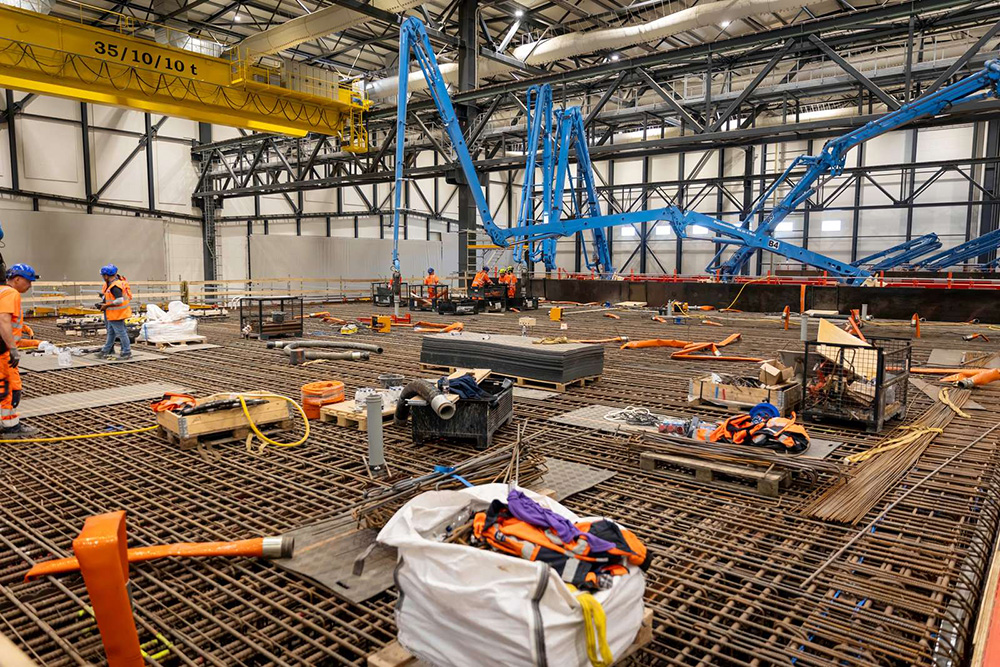
Welding steel is traditionally hard physical work, but in the Panel Factory, all manual heavy lifting has been completely eliminated. The heaviest lifts are performed by large overhead cranes, while small lifts make it easy for individual workers to move smaller steel parts between machines. Additionally, welding work emits toxic fumes meaning that all welding takes place in special areas with strong extraction systems.
However, most of the work is done by the two robotic welding machines, which handle over 70 per cent of the production. The robots are fed by a magnetic crane that can lift up to five tonnes of steel at a time. The steel comes in rods up to 15m long and 32mm in diameter.
The robotic welding machine is a prototype made by the Spanish company DCM-Wire. Normally, these machines are used to make thin panels for fences, and the Fehmarn project is the first place in the world where robotic welding machines are used to weld reinforcement steel of this thickness.
The tunnel will comprise 79 large 217m-long tunnel elements and 10 special 24m-long concrete elements, all built at the facility on Rødbyhavn - the largest construction site in northern Europe. A 217m-long element - composed of nine segments 24m long - weighs 73,500 tonnes.
Casting of the first element took about 10 months, whereas it is expected that the elements can be produced in nine weeks going forward. "Nowhere else in the world does serial production of concrete elements of this size take place, but this is precisely what we have to master over the years ahead. Our goal is to transform the exceptional into routine practice,” said Sébastien Bliaut, director of Fermen Link Contractors.
On June 17, the Danish king inaugurated the first 217m-long element to be submerged on the Danish side later this year. A time capsule containing the thoughts and items of people who helped build and design the first tunnel element was sealed and placed in the Fehmarnbelt project’s exhibition centre before being buried near the tunnel portal as a greeting to future generations.
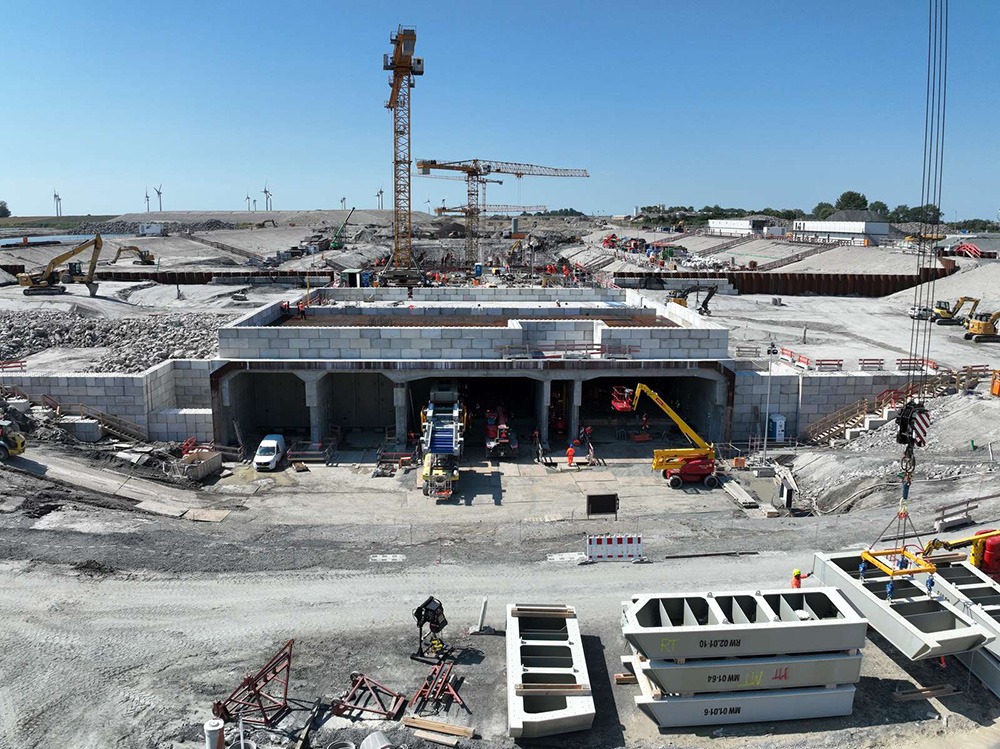
The finished tunnel element was left to cure for three weeks before the next stage began – installation of steel bulkheads and ballast tanks to ensure the element’s stability during immersion for placement in the tunnel’s trench on the bottom of the sea. Henrik Vincentsen, chief executive of Femern, said at the time of the first casting, that the work had been a long and complicated but the technology and methods had proven to work well.
Production on Lolland of the remaining 78 standard elements continues on five production lines, while a separate line produces the 10 special elements. At the opposite end of the construction site on Lolland, the contractor consortium, FBC, is currently excavating the portal and the tunnel trench where the first tunnel element will be immersed later this year.
The two contractor consortia, Fehmarn Belt Contractors (FBC) and Fehmarn Link Contractors (FLC), are responsible for the construction of the tunnel that will run between Rødbyhavn on Lolland and Puttgarden, a ferry harbour and a village on the German island of Fehmarn.
The contract with the Dutch contractor consortium, FBC, came into force in November 2019. The task includes the dredging work at sea, the establishment of the two work harbours and land reclamation for the new nature areas.
Femern entered into the conditional contracts for the construction of the tunnel itself, portals and ramps in May 2020. The contracts are with the FLC contractor consortium and were effective from 1 January 2021.
In May 2022, Femern and the contractor consortium Femern Systems Contractors (FSC) signed the contract for equipping the tunnel with electro-mechanical installations and technology. Then in December 2022, Femern and Elecnor signed the contract for building a large transformer station that will supply green power to the Fehmarnbelt tunnel’s installations and the railway between Denmark and Germany, as well as on Lolland.
When the tunnel is finished, crossing the Fehmarnbelt will take just seven minutes by train and 10 minutes by car.