A demolition job in California was carried out successfully using a hydraulic breaker fitted to an excavator. An overpass on Highway 91 in Southern California had to be removed, with the contractor opting to use a hydraulic breaker for the job. The work was carried out within the 22-hour possession period set by the local authorities, allowing the route to reopen to traffic on time and minimising transport delays.
The work was carried out safely and precisely, due to the use of suitable equipment. The re
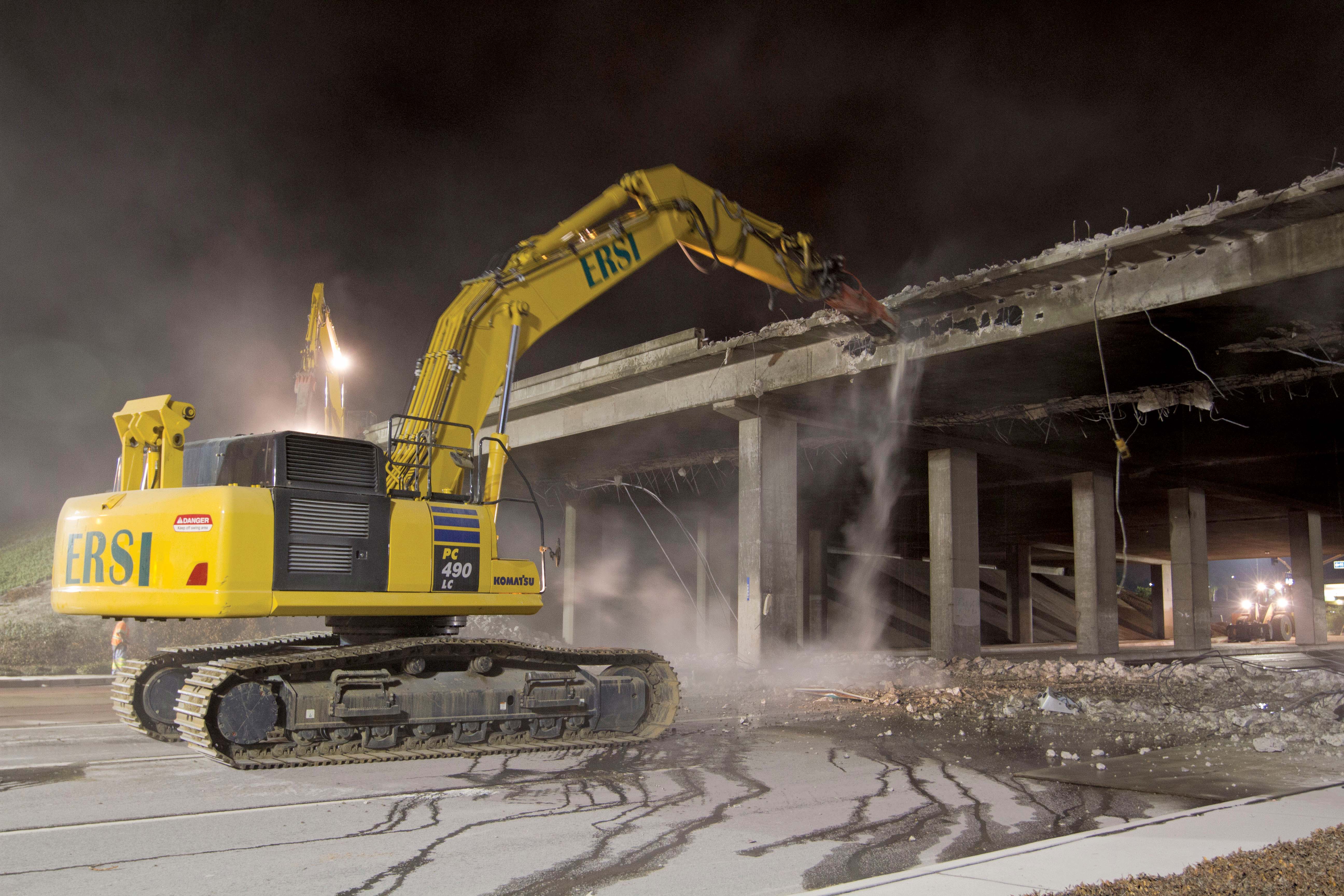
Tough working conditions proved no obstacle to safe removal of the old overpass in Southern California
A demolition job in California was carried out successfully using a hydraulic breaker fitted to an excavator
An overpass on Highway 91 in Southern California had to be removed, with the contractor opting to use a hydraulic breaker for the job. The work was carried out within the 22-hour possession period set by the local authorities, allowing the route to reopen to traffic on time and minimising transport delays.
The work was carried out safely and precisely, due to the use of suitable equipment. The removal of the large highway overpass benefited from extensive planning and preparation before the first piece of equipment rolled on to the worksite. This was important as the work was carried out on one of the most heavily congested freeways in southern 'California.' Safety and environmental issues included dust suppression, sound suppression, re-routing of vehicle traffic and the recycling of scrap and other re-usable materials.
These variables came in to play when Environmental Remediation Services, Inc (ERSI), a customer of Tracey Road Equipment, was contracted to help widen the Route 91 Corridor in Corona, California. Tracey Road Equipment is a distributor for Allied Construction Products,2403 Sandvik Construction’s authorised distributor for 5076 Rammer in North America. A key part of the project was the bridge demolition at the Interstate 15 and 91 Corona Interchange. To help alleviate traffic congestion flowing through Corona, a majority of the work had to be done at night. Working over active railroad tracks and storm runoff channels added further challenges to the project.
“The close proximity of the railroad tracks had to be accounted for,” said on-site ERSI superintendent Glenn Beam. “The trains were running close by the overpass so that gave us a limited work window.”
To minimise the risk of potential problems issues like this and others were planned for in advance. “This project was bid as a design-build and was funded by the State of California along with some Federal assistance. In a design-build, teams work together to come up with a good plan and calculate accordingly,” said Beam.
One of the plan’s primary considerations was that much of the demolition work was being carried out at height over long periods of time. For that reason, ERSI selected Rammer 4099 hydraulic hammers to demolish the overpass. Beam said, “We were working the Rammer 4099 in high elevation scenarios for a solid 22 hours.”
He explained that the breakers worked continuously during the 22-hour period and were matched with2300 Komatsu excavators, which also offered high performance in the tough application. Another important operating feature of this type of breaker was its sound-suppression system, which helped reduce noise and disturbance in the urban application.
So that the highway never had to be shut down completely, the work was carried out in phases. Beam said, “Our timetable had us doing the work in sections. This allowed us to build back what we took out, add the new lanes – all while keeping the lanes opened that weren’t demolished.”
As work began, excavator crews started in the middle of the overpass and moved outward. “To balance the load, we sectioned the bridge in half. The excavators then worked in opposite directions. We had a slotted deck that allowed us to drop the concrete and rebar below,” Beam said.
The demolition team then focused on lightening the girders. “First, the Rammer 4099 hammer knocked the concrete off and it fell to the deck. Then, we pepper-screwed the rebar and it fell on top of the concrete. We did the same thing with abutments – we peppered-screwed the end-caps.”
Another important feature of this model of Rammer breaker was its variable frequency, with blow rate ranging from 400–560bpm depending on the strength of the material being broken out. This enabled a total of 353.85m3 of concrete to be removed in a very limited period of time. In addition the 4099 hammer has other features, including the VIDAT System that includes vibration dampened tie-rods that reduce operating costs, extend operating life and minimise downtime. These meant that ERSI was able to handle the tight time constraints of the project. In fact, the Interstate 15 and 91 Corona Interchange was opened 11 hours ahead of schedule.
Demolition convention
The UK’s National Federation of Demolition Contractors recently held its annual convention in Northern Ireland. Located at the Slieve Donard Resort & Spa in County Down, and Sandvik Construction’s Ballygawley factory, the convention was a major success, with more than 200 delegates attending.
The National Federation of Demolition Contractors (NFDC) is the voice of the UK and Irish demolition industry. It aims to raise the industry’s profile by focusing on continually improving all facets of demolition; the organisation aims to benefit its members, customers, and the general public.
This is achieved through training, monitoring and policing of best practices, as well as enhancing the flow of information and discussion between the demolition industry and government, trade and technical organisations.
A key part of the NFDC’s activities is its annual conference. Delegates from throughout the industry are able to share best practices, listen to the latest thinking in the industry, and mix in an informal manner. This year’s conference was held at the Slieve Donard Resort & Spa in Northern Ireland.
Sandvik Construction played a key role in the success of the conference. On the Saturday morning delegates held their annual meeting on the shop floor of Sandvik’s Ballygawley factory; this was located in the spray shop, the home of a brand new powder coating plant.
Following the meeting the delegates undertook a factory tour of the Ballygawley site, during which they were able to see where, and how, the mobile crushing and screening range is manufactured.
An overpass on Highway 91 in Southern California had to be removed, with the contractor opting to use a hydraulic breaker for the job. The work was carried out within the 22-hour possession period set by the local authorities, allowing the route to reopen to traffic on time and minimising transport delays.
The work was carried out safely and precisely, due to the use of suitable equipment. The removal of the large highway overpass benefited from extensive planning and preparation before the first piece of equipment rolled on to the worksite. This was important as the work was carried out on one of the most heavily congested freeways in southern 'California.' Safety and environmental issues included dust suppression, sound suppression, re-routing of vehicle traffic and the recycling of scrap and other re-usable materials.
These variables came in to play when Environmental Remediation Services, Inc (ERSI), a customer of Tracey Road Equipment, was contracted to help widen the Route 91 Corridor in Corona, California. Tracey Road Equipment is a distributor for Allied Construction Products,
“The close proximity of the railroad tracks had to be accounted for,” said on-site ERSI superintendent Glenn Beam. “The trains were running close by the overpass so that gave us a limited work window.”
To minimise the risk of potential problems issues like this and others were planned for in advance. “This project was bid as a design-build and was funded by the State of California along with some Federal assistance. In a design-build, teams work together to come up with a good plan and calculate accordingly,” said Beam.
One of the plan’s primary considerations was that much of the demolition work was being carried out at height over long periods of time. For that reason, ERSI selected Rammer 4099 hydraulic hammers to demolish the overpass. Beam said, “We were working the Rammer 4099 in high elevation scenarios for a solid 22 hours.”
He explained that the breakers worked continuously during the 22-hour period and were matched with
So that the highway never had to be shut down completely, the work was carried out in phases. Beam said, “Our timetable had us doing the work in sections. This allowed us to build back what we took out, add the new lanes – all while keeping the lanes opened that weren’t demolished.”
As work began, excavator crews started in the middle of the overpass and moved outward. “To balance the load, we sectioned the bridge in half. The excavators then worked in opposite directions. We had a slotted deck that allowed us to drop the concrete and rebar below,” Beam said.
The demolition team then focused on lightening the girders. “First, the Rammer 4099 hammer knocked the concrete off and it fell to the deck. Then, we pepper-screwed the rebar and it fell on top of the concrete. We did the same thing with abutments – we peppered-screwed the end-caps.”
Another important feature of this model of Rammer breaker was its variable frequency, with blow rate ranging from 400–560bpm depending on the strength of the material being broken out. This enabled a total of 353.85m3 of concrete to be removed in a very limited period of time. In addition the 4099 hammer has other features, including the VIDAT System that includes vibration dampened tie-rods that reduce operating costs, extend operating life and minimise downtime. These meant that ERSI was able to handle the tight time constraints of the project. In fact, the Interstate 15 and 91 Corona Interchange was opened 11 hours ahead of schedule.
Demolition convention
The UK’s National Federation of Demolition Contractors recently held its annual convention in Northern Ireland. Located at the Slieve Donard Resort & Spa in County Down, and Sandvik Construction’s Ballygawley factory, the convention was a major success, with more than 200 delegates attending.
The National Federation of Demolition Contractors (NFDC) is the voice of the UK and Irish demolition industry. It aims to raise the industry’s profile by focusing on continually improving all facets of demolition; the organisation aims to benefit its members, customers, and the general public.
This is achieved through training, monitoring and policing of best practices, as well as enhancing the flow of information and discussion between the demolition industry and government, trade and technical organisations.
A key part of the NFDC’s activities is its annual conference. Delegates from throughout the industry are able to share best practices, listen to the latest thinking in the industry, and mix in an informal manner. This year’s conference was held at the Slieve Donard Resort & Spa in Northern Ireland.
Sandvik Construction played a key role in the success of the conference. On the Saturday morning delegates held their annual meeting on the shop floor of Sandvik’s Ballygawley factory; this was located in the spray shop, the home of a brand new powder coating plant.
Following the meeting the delegates undertook a factory tour of the Ballygawley site, during which they were able to see where, and how, the mobile crushing and screening range is manufactured.