Ian Fraser, Tensar International’s director of application technology, looks at the latest lessons learned from the flood-hit Workington Bridge project in Cumbria, North West England. Rarely has a disaster like the Cumbrian floods demonstrated with more clarity the benefit of designing working platforms and bridge abutments to tested performance standards, as opposed to slavishly following accepted, but often much less efficient, design norms.
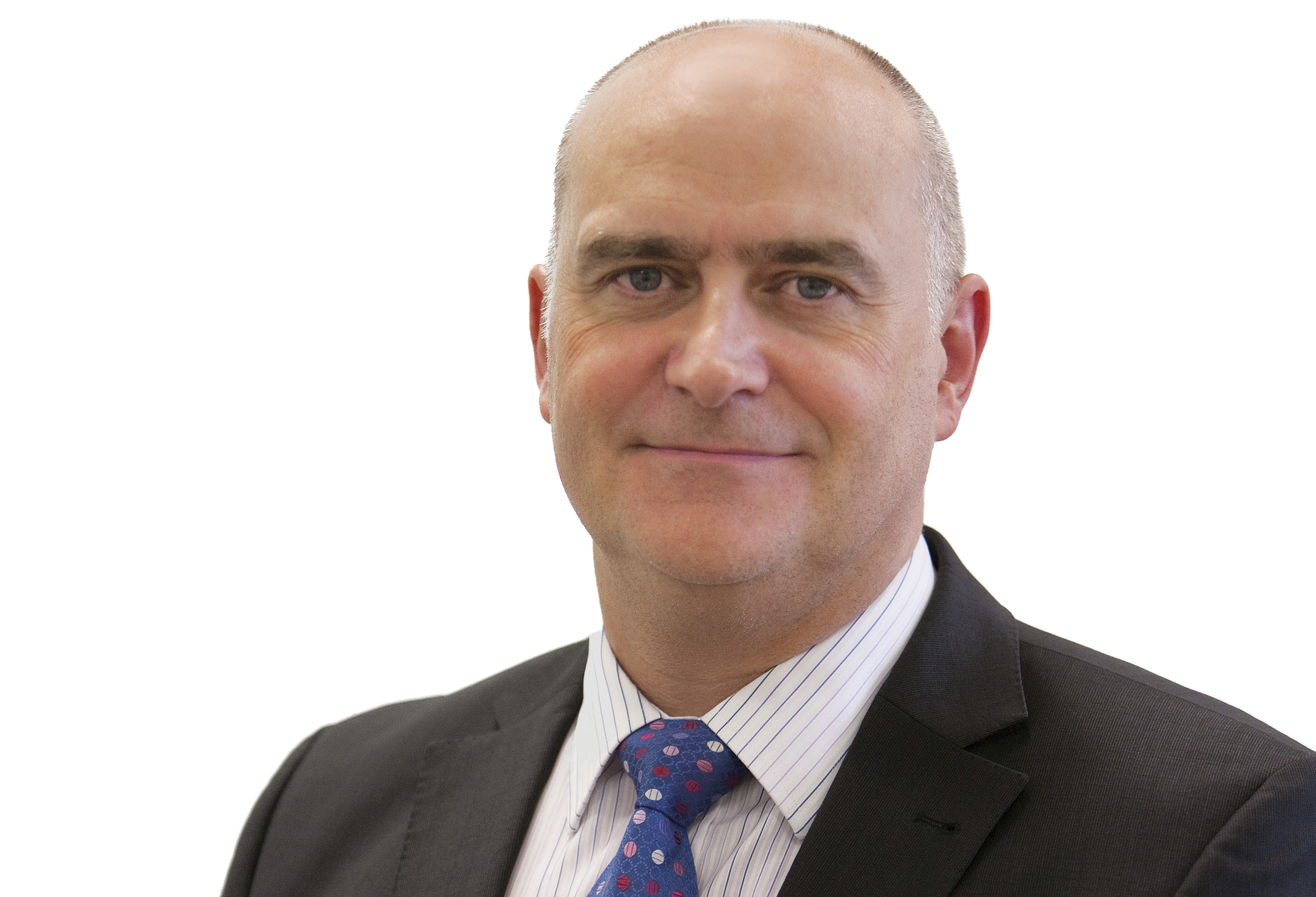
Ian Fraser, Tensar International’s director of application technology
Ian Fraser, 340 Tensar International’s director of application technology, looks at the latest lessons learned from the flood-hit Workington Bridge project in Cumbria, North West England
Rarely has a disaster like the Cumbrian floods demonstrated with more clarity the benefit of designing working platforms and bridge abutments to tested performance standards, as opposed to slavishly following accepted, but often much less efficient, design norms.
The case in point is the installation of the temporary bridge crossing the River Derwent at Workington, Cumbria, after a late 2009 flood isolated the two sides of the town. In a project designed and led by the Royal Engineers’ Captain Caroline Livesey, a replacement was in place in just 13 days.
The installation was based on a temporary working platform and bridge abutments, constructed from HA Type 1 sub-base aggregate mechanically stabilised by TriAx geogrid layers. This provided the load bearing base carrying all the associated plant for deploying the whole 52 metre span of the bridge, without requiring excavation of the wet topsoil, thereby saving time and materials.
Craig Roberts, Tensar’s area civil engineer, designed the supporting geogrid structures. The design was based on the improved layer stiffness resulting from the mechanical stabilisation of the aggregate due to the interlocking and confinement provided by the TriAx geogrids.
Full third party testing programmes had shown that load bearing structures could be achieved with significant savings in aggregate compared to the default design approach based on tensile strength, which is more appropriate to geotextiles. The bridge deployment was a well-deserved success for the Army engineers.
After 15 months and with repairs to one of the damaged road bridges completed, the temporary bridge was removed. Captain Livesey published a paper on the project in the ICE’s publication Civil Engineering (CE), which provided the opportunity of examining geogrid performance in an actual application by a third party.
Writing in CE Captain Livesey said: “The platform performed very well throughout the life of the bridge. During the construction phase there was very little deformation observed despite heavy point loads, and extensive trafficking from plant.
“Of particular note was the abutment area. During construction the maximum temporary loading conditions were not reached as the bridge landed on the north bank rollers before the centre of gravity had moved forward of the southern abutment rollers. However, no movement was recorded.
“Numerous surveys were then conducted during the life of the bridge and just before its recovery. Only 5 mm settlement was noted in the abutments during the 15-month life of the bridge.”’
These observations demonstrate the importance of relying on design methodologies derived from empirical data drawn from appropriately comprehensive performance trial programmes. By using state of the art design methods based on such data, civil engineers are reducing the cost and enhancing available sustainability benefits.
Rarely has a disaster like the Cumbrian floods demonstrated with more clarity the benefit of designing working platforms and bridge abutments to tested performance standards, as opposed to slavishly following accepted, but often much less efficient, design norms.
The case in point is the installation of the temporary bridge crossing the River Derwent at Workington, Cumbria, after a late 2009 flood isolated the two sides of the town. In a project designed and led by the Royal Engineers’ Captain Caroline Livesey, a replacement was in place in just 13 days.
The installation was based on a temporary working platform and bridge abutments, constructed from HA Type 1 sub-base aggregate mechanically stabilised by TriAx geogrid layers. This provided the load bearing base carrying all the associated plant for deploying the whole 52 metre span of the bridge, without requiring excavation of the wet topsoil, thereby saving time and materials.
Craig Roberts, Tensar’s area civil engineer, designed the supporting geogrid structures. The design was based on the improved layer stiffness resulting from the mechanical stabilisation of the aggregate due to the interlocking and confinement provided by the TriAx geogrids.
Full third party testing programmes had shown that load bearing structures could be achieved with significant savings in aggregate compared to the default design approach based on tensile strength, which is more appropriate to geotextiles. The bridge deployment was a well-deserved success for the Army engineers.
After 15 months and with repairs to one of the damaged road bridges completed, the temporary bridge was removed. Captain Livesey published a paper on the project in the ICE’s publication Civil Engineering (CE), which provided the opportunity of examining geogrid performance in an actual application by a third party.
Writing in CE Captain Livesey said: “The platform performed very well throughout the life of the bridge. During the construction phase there was very little deformation observed despite heavy point loads, and extensive trafficking from plant.
“Of particular note was the abutment area. During construction the maximum temporary loading conditions were not reached as the bridge landed on the north bank rollers before the centre of gravity had moved forward of the southern abutment rollers. However, no movement was recorded.
“Numerous surveys were then conducted during the life of the bridge and just before its recovery. Only 5 mm settlement was noted in the abutments during the 15-month life of the bridge.”’
These observations demonstrate the importance of relying on design methodologies derived from empirical data drawn from appropriately comprehensive performance trial programmes. By using state of the art design methods based on such data, civil engineers are reducing the cost and enhancing available sustainability benefits.