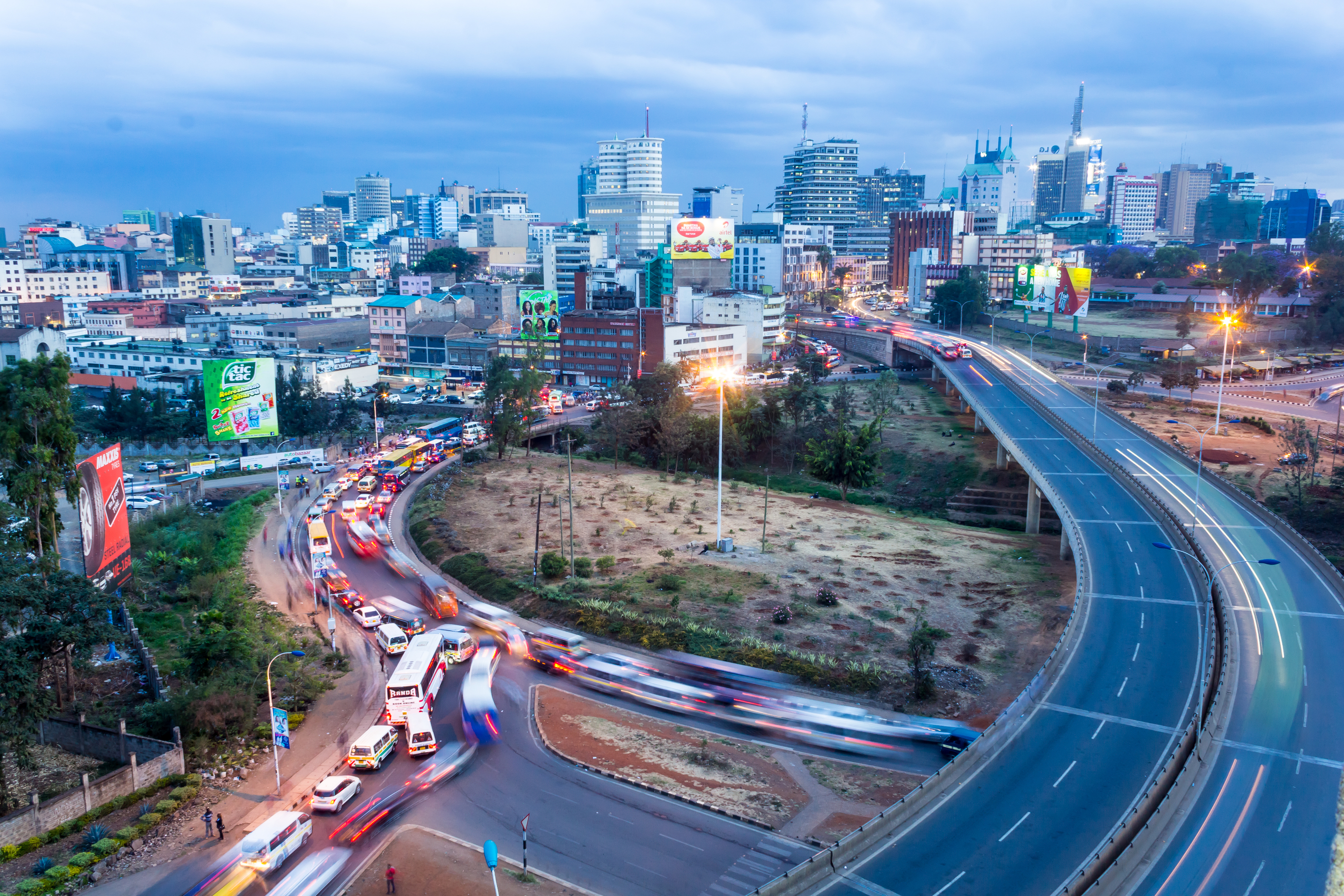
The lack of programmed maintenance of bridges in Kenya continues to undermine the structural integrity of the infrastructure and compromising their general usage safety despite the existence of approved measures to protect them from falling into a state of disrepair. Experts think that both the absence of a maintenance component in bridge construction contracts, especially for those built one or two decades ago, and a weak maintenance supervisory culture undermines the safety of the bridges. However, no major disaster has yet been reported in Eastern Africa despite this negligence of routine maintenance.
“Generally in East Africa there is a lack of regular and annual maintenance of bridge infrastructure,” said Walter Oyawa, acting CEO of Kenya’s Commission for University Education and a civil engineering professor.
“In developed countries such as Japan, where regular maintenance of bridge infrastructure is common, consultants or contractors do the design of the bridge with a component of maintenance included in the contract stating clearly when and how the maintenance should be done in five, 10 or 50 years,” he said.
“The maintenance schedule for any bridge depends on whether it has been constructed using concrete or steel,” he said.
Professor Oyawa said although both materials have a corrosion element, the corrosion element in concrete-built bridges shows on emerging cracks on both the superstructure and substructure components of the bridge. Kenya is struggling with a $3.5 billion to $4 billion road maintenance backlog that includes various types of bridges both in urban and rural areas.
The
However, Professor Oyawa says the lack of coordination and teamwork among road agencies, experts, contractors and even bridge users could partly explain the absence of a sustainable maintenance programme
“Part of the reason why maintenance is not given a priority in this part of the region is because of failure to transfer relevant technology and knowledge from foreign experts and contractors who construct the bridges to the local personnel and maintenance agencies,” he said.
Professor Oyawa said bridge construction contracts in countries such as those in East Asia “have technology/knowledge transfer as a mandatory component.”
“This means when the contractor completes the bridge project and hands it over, the local road/bridge agencies have capacity to operate and maintain it because there is a team that has already been trained to carry out the scheduled maintenance works,” he said.
He gave the example of the two-lane 192m-long prestressed concrete Mtwapa Bridge in the coastal city of Mombasa which was constructed in 1980 but had to be repaired in 2005 after it developed cracks in girders, deflection of the central span and damage in bearings.
“There was no team to collaborate with the Japanese contractor at the initial construction stage and the problems that emerged later meant the foreign contractor had to be called in to assess the bridge’s safety and carry out reinforcement, repairs and sealing,” said Professor Oyawa.
Meanwhile Germany-based specialist in mechanical engineering and steel construction, Maurer Group, says the quality and longevity of materials used in bridge construction can be easily assured if the production process is monitored closely and partnerships forged between the material producers, users and material testing agencies.
Raad Hamood, a director with Maurer Group, told participants at the transport infrastructure conference in Nairobi in June, the company, which has previously supplied bridge bearings for the 3km extradosed Kazungula road/rail bridge configuration across the Zambezi River, has innovated new bridge construction products that could improve safety, assure longevity of bridges and minimise maintenance costs.
He said the Maurer Sliding Material (MSM), a patented sliding material for structural bearings, could enhance the safety and performance of bridges in the African market since it fits in regions with temperatures of -50°C to 70°C and requires no maintenance.
Hamood, however, said for markets such as East Africa to benefit from the MSM sliding material, they have to exclusively use Maurer products because “MSM is exclusively for Maurer products.”
The challenge for bridge designers and construction contractors is to ensure the bearings achieve maximum efficiency in transmission of “vertical and horizontal loads from the superstructure into the bottom structure allowing for rotations and relative displacements where necessary.”
Hamood said Maurer, which manufactures fixed, guided-sliding and free-sliding bearings, depending on the products’ ability to compensate for displacements and transmit horizontal forces, places a premium on MSM because, “it accommodates for concrete setting and evenness deviations due to its elastoplastic behaviour (whereas rigid sliding materials may lead to local overstress and wear).”