Highway road tunnels and inter-city vehicle underpasses are vital components of an essential busy highways network. Keeping them clean is essential. Road tunnels and vehicle underpasses require a specific strength of light. Too bright, and the lamps or lights may dazzle or distract drivers, and too dim the tunnel can seem claustrophobic and daunting, as well as increasing dangers from obstructions and other hazards.
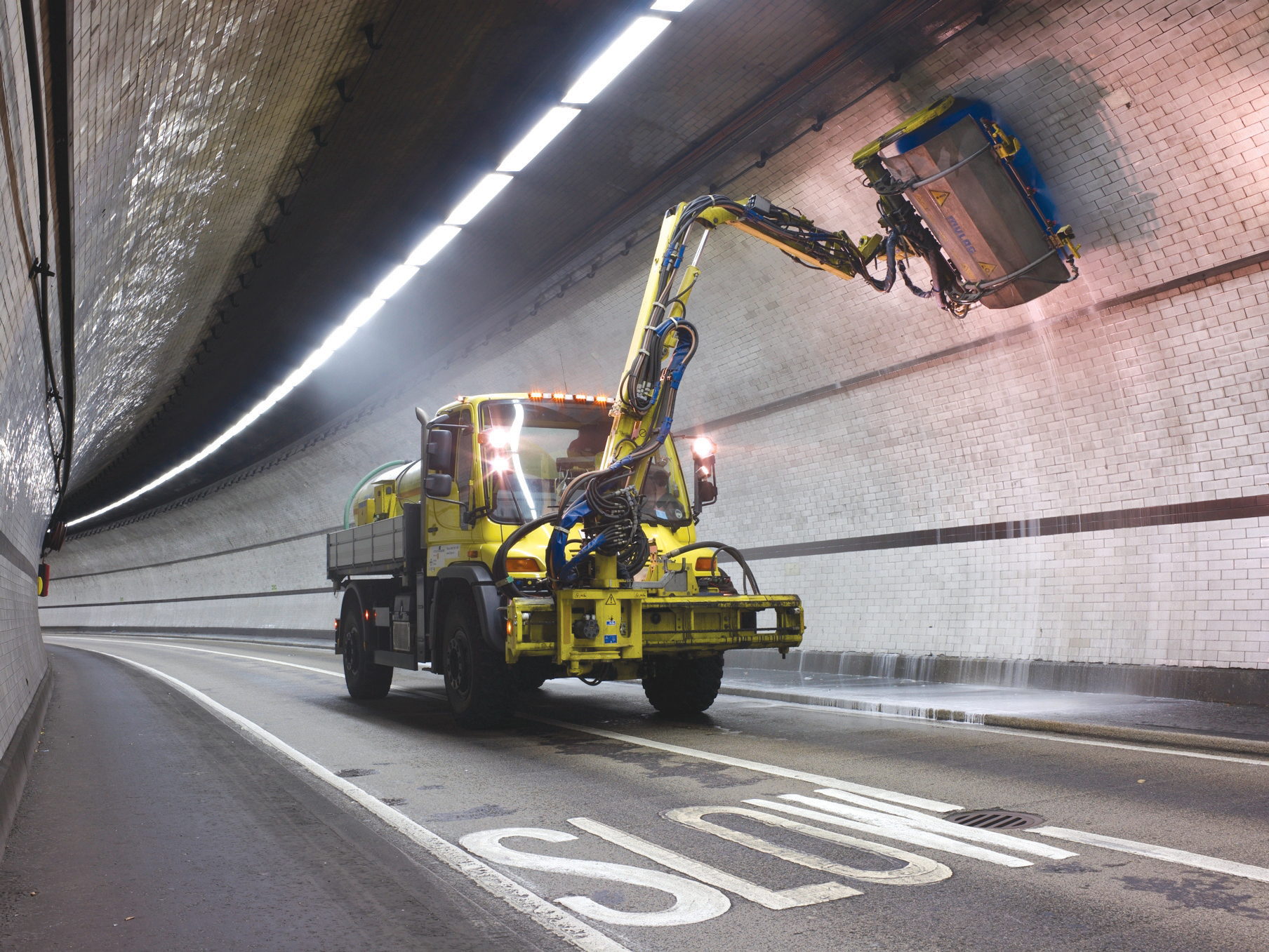
The Mercedes-Benz Unimog U500 with Mulag washing unit shift the grime and stains inside the Rotherhithe and Blackwall Tunnels
Highway road tunnels and inter-city vehicle underpasses are vital components of an essential busy highways network. Keeping them clean is essential
Road tunnels and vehicle underpasses require a specific strength of light. Too bright, and the lamps or lights may dazzle or distract drivers, and too dim the tunnel can seem claustrophobic and daunting, as well as increasing dangers from obstructions and other hazards. The solution is to use the walls of the tunnel to reflect artificial light and create a 'false' ambient lighting effect.The level of lighting must encourage drivers to use their dipped beam, or, in many modern vehicles, trigger the automatic headlight sensor, and also provide sufficient light for any pedestrians or emergency incidents, such as breakdowns. Reflectivity uses all surfaces of the tunnel, including the roadway, but by far the most important are the walls, which is a reason for painting them in light colours and keeping them clean. For example, the
Tunnel surfaces require frequent washing to make it easier to keep clean and maintain the levels of reflectivity. On open roads, street lamps are at their brightest when it is darkest: in tunnels the opposite is true. Motorists' eyes must adjust to the dark and therefore at the entrance and exit to the tunnel lighting is at its brightest, diminishing in intensity as the tunnel progresses, but cleanliness of the tunnel walls is a constant factor in road safety.
Tunnel walls under rivers and estuaries often have facings of light-painted ductile cast iron plates for security against tidal flows and the depth of the structure. At their entrance and exits (and with most horizontal road tunnels) the facing may be lightly curved or straight and made of smooth white or light enamel to aid reflectivity.
In either case aggressive and acidic emissions and deposits can adversely affect the appearance and longevity of the wall covering. The most cost-effective way of reducing these effects and the structure's life is to keep the tunnel clean.
Environmentally, a combination of energysaving lighting and clean reflective materials reduce the lighting requirements resulting in reduced energy.
One example is at London's Blackwall Tunnel under the River Thames, where the busy traffic thoroughfare is being cleaned by a
The purpose-designed application has been specified, purchased and is operated by
The tunnel walls and cladding are continuously being covered in dust particles between tunnel routine maintenance closures, and the long wheelbase Unimog U500 uses Mulag long-reach arms to shift the grime and stains. This is achieved, without damaging the walls or street furniture by using clean, chemical-free water from the 3,000litre water tank and without recourse to detergents.
Water is sprayed onto the wall followed by a large rotating brush that agitates and removes the dirt and grime followed again by a water spray that rinses the surface. The whole operation is combined within the brush assembly head and to prevent the potential risk of this fast and efficient operation damaging the tunnel wall panels, automated pressure sensors are attached to the brush mechanism. These automatically control the height, pressure and position of the brush, following the tunnel's wall curvature and varying height. The Unimog's Mercedes-Benz diesel engine meets Euro 4 emissions and a hydrostatic drive enables the driver to operate all attachments with stepless adjustments of working speeds at a constant engine speed and torque.
The Mercedes-Benz VarioPilot system allows the driving position to change from left to right, mechanically in less than a minute, to ensure the driver is always facing the correct and safest way.
The tunnel washing 'package' consists of a front-mounted, hydraulically adjustable telescopic arm with a reach of up to 6.5m either side of the Unimog, and with a lateral shift of 1.8m. This allows the brush to sweep to the left, right or overhead, with all controls operated by the driver within the vehicle's cab. All equipment, including the pumps, arms and brushes are operated hydraulically direct from the Unimog's engine.
The western tunnel at Blackwall was opened in 1897 after five years construction, and at 1,344m long was then the longest underwater tunnel in the world. The eastern bore opened in 1967, making it a twin-bore tunnel complex.