The Queensferry Crossing forms the centrepiece of a major upgrade to the cross-Forth transport corridor in the east of Scotland. It will be the longest three-tower, cable-stayed bridge in the world and represents a Scottish Government capital investment of more than €1.5 billion.
The 2.7km Queensferry Crossing is alongside the Forth Road Bridge and will carry the M90 motorway across the Firth of Forth between Lothian, at South Queensferry, and Fife, at North Queensferry. Each of the three towers are 207m
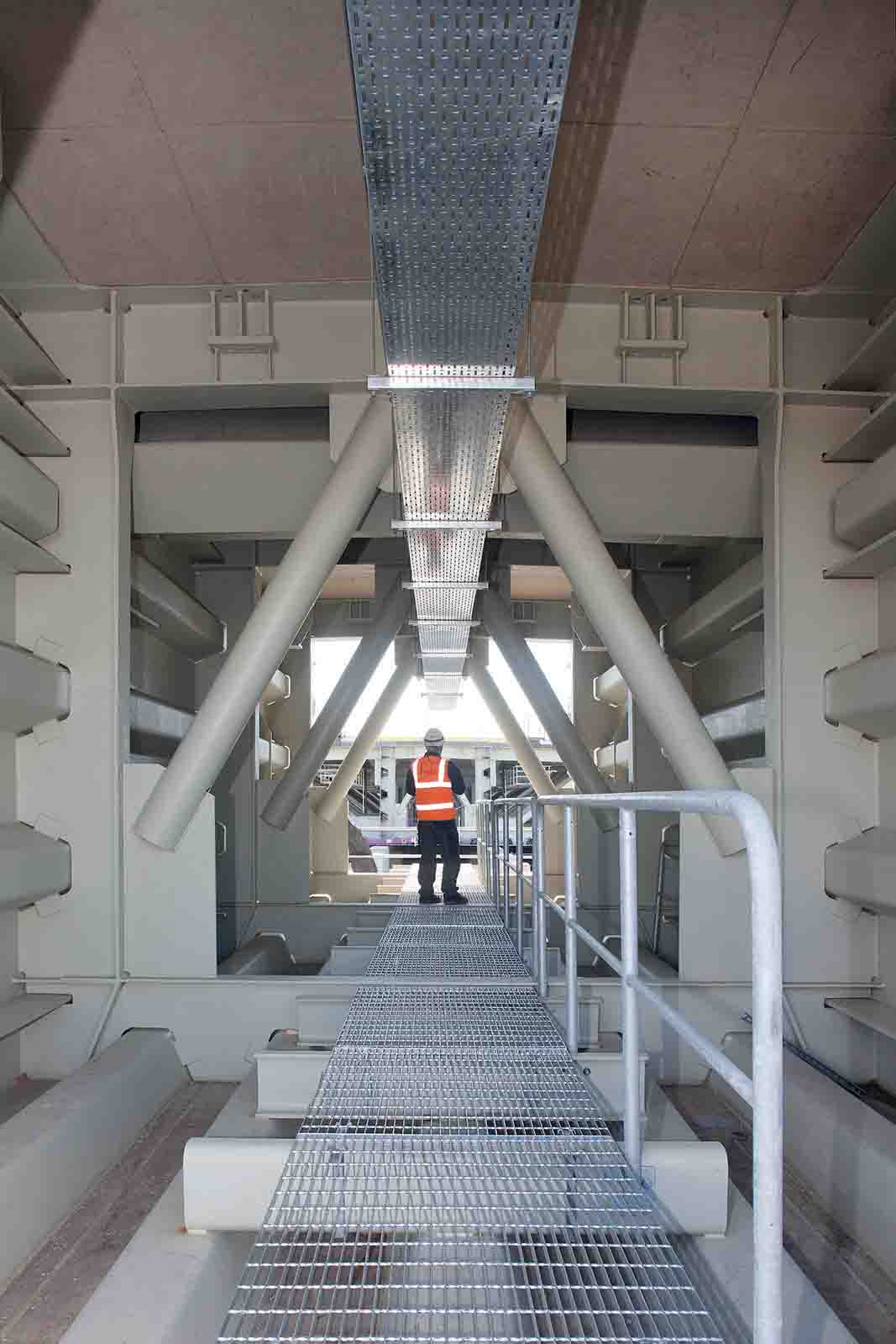
Queensferry Crossing takes shape
The Queensferry Crossing forms the centrepiece of a major upgrade to the cross-Forth transport corridor in the east of Scotland. It will be the longest three-tower, cable-stayed bridge in the world and represents a Scottish Government capital investment of more than €1.5 billion.
The 2.7km Queensferry Crossing is alongside the Forth Road Bridge and will carry the M90 motorway across the Firth of Forth between Lothian, at South Queensferry, and Fife, at North Queensferry. Each of the three towers are 207m high.
Scotland’s weather can often be extreme and has played its part during construction. The bridge was due to be completed by last December. But completion was put back to May this year due to weather delays. Media reports showed that 25 days were lost due to high winds during April and May last year. Any products or processes that can keep the project on schedule is vitally important.
The bridge will need around 4km of new connecting roads. But it is more than just a bridge. It also will carry an array of utilities and communications equipment, making Queensferry Crossing one of the UK’s most utility-complex bridges. This presented a supply chain challenge to the partnership between cable management specialist voestalpine Metsec, mechanical and electrical fixings supplier MEF and contractor SES Engineering Services (SES).
The 250tonne steel bridge sections arrive in Rosyth docks from China, where they are then prefabricated to incorporate all of the services and road surfaces. Specialist cold roll-forming company voestalpine Metsec - part of the voestalpine engineering group based in Linz, Austria – is supplying the cable management systems. These are prefabricated into 424 modules by SES and then installed into each of the 110 finished 750tonne road section decks. They are then taken out by barge onto the River Forth for lifting by crane to connect to the span between the bridge towers.
All of the cable management products used had to be pre-approved by the construction contractors, the Forth Crossing Bridge Constructors Consortium (FCBC):981 HOCHTIEF Solutions, 1021 American Bridge International, 4761 Dragados and 8288 Morrison Construction. Extreme temperatures meant it was essential that thermal extension couplers for cable management were designed into the project with the support of the Metsec team.
“MEF is part of the SES-approved supply chain because the company can supply cable management systems we needed in bespoke sizes, vitally important in terms of minimising waste and ensuring ease of fit,” says Gordon Cullen, contracts manager at SES. “MEF was willing to adapt the units to minimise the number of joints required.”
Metsec supplied hot-dip galvanised cable trays and cable ladders cut to special lengths, the trays to 3.5m and the ladders to 6.9m. The finished modules assembled by SES will hold a complex array of water management and cabling needs, from lighting and power, traffic management systems, security, fire alarms, radio communications, structural health monitoring and building monitoring, all designed to give optimal control over the management and performance of the bridge.
“It’s a highly complex installation that effectively acts as the ‘brains’ of the bridge,” says Cullen. “They control everything from the timing of the lights to maintenance planning with a focus on optimising efficiency and communications not just on the bridge but on how it communicates with the traffic management systems that feed into it.”
The bridge’s 55micron hot-dipped galvanised steel tray and ladder systems will need to endure exposure to the elements for up to two years before being completely sealed in under the bridge, explains Alistair Fairweather, sales manager at MEF. “The high quality of the product will contribute to keeping the whole life costs of the project down.”
“We knew we had the capability to reprogramme our mill to allow us to manufacture the specified lengths of ladder and tray in a way that would fit perfectly into the required modules,” says Jon Hillier, director at Metsec cable management division. “Working with MEF meant that we could offer just-in-time capabilities to support tight prefabrication scheduling for each bridge deck.”
The 2.7km Queensferry Crossing is alongside the Forth Road Bridge and will carry the M90 motorway across the Firth of Forth between Lothian, at South Queensferry, and Fife, at North Queensferry. Each of the three towers are 207m high.
Scotland’s weather can often be extreme and has played its part during construction. The bridge was due to be completed by last December. But completion was put back to May this year due to weather delays. Media reports showed that 25 days were lost due to high winds during April and May last year. Any products or processes that can keep the project on schedule is vitally important.
The bridge will need around 4km of new connecting roads. But it is more than just a bridge. It also will carry an array of utilities and communications equipment, making Queensferry Crossing one of the UK’s most utility-complex bridges. This presented a supply chain challenge to the partnership between cable management specialist voestalpine Metsec, mechanical and electrical fixings supplier MEF and contractor SES Engineering Services (SES).
The 250tonne steel bridge sections arrive in Rosyth docks from China, where they are then prefabricated to incorporate all of the services and road surfaces. Specialist cold roll-forming company voestalpine Metsec - part of the voestalpine engineering group based in Linz, Austria – is supplying the cable management systems. These are prefabricated into 424 modules by SES and then installed into each of the 110 finished 750tonne road section decks. They are then taken out by barge onto the River Forth for lifting by crane to connect to the span between the bridge towers.
All of the cable management products used had to be pre-approved by the construction contractors, the Forth Crossing Bridge Constructors Consortium (FCBC):
“MEF is part of the SES-approved supply chain because the company can supply cable management systems we needed in bespoke sizes, vitally important in terms of minimising waste and ensuring ease of fit,” says Gordon Cullen, contracts manager at SES. “MEF was willing to adapt the units to minimise the number of joints required.”
Metsec supplied hot-dip galvanised cable trays and cable ladders cut to special lengths, the trays to 3.5m and the ladders to 6.9m. The finished modules assembled by SES will hold a complex array of water management and cabling needs, from lighting and power, traffic management systems, security, fire alarms, radio communications, structural health monitoring and building monitoring, all designed to give optimal control over the management and performance of the bridge.
“It’s a highly complex installation that effectively acts as the ‘brains’ of the bridge,” says Cullen. “They control everything from the timing of the lights to maintenance planning with a focus on optimising efficiency and communications not just on the bridge but on how it communicates with the traffic management systems that feed into it.”
The bridge’s 55micron hot-dipped galvanised steel tray and ladder systems will need to endure exposure to the elements for up to two years before being completely sealed in under the bridge, explains Alistair Fairweather, sales manager at MEF. “The high quality of the product will contribute to keeping the whole life costs of the project down.”
“We knew we had the capability to reprogramme our mill to allow us to manufacture the specified lengths of ladder and tray in a way that would fit perfectly into the required modules,” says Jon Hillier, director at Metsec cable management division. “Working with MEF meant that we could offer just-in-time capabilities to support tight prefabrication scheduling for each bridge deck.”