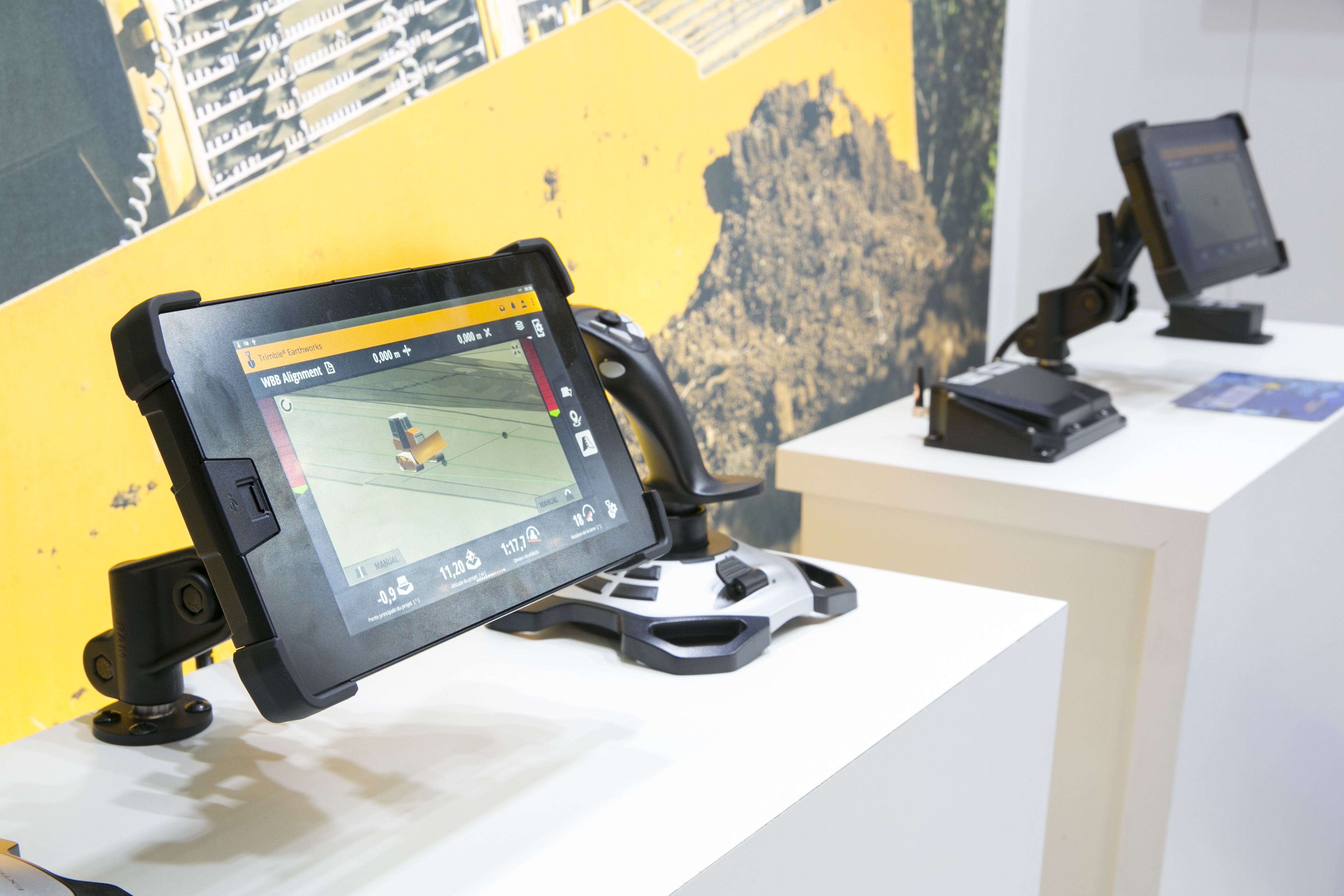
An important technology advance from
The first EarthWorks system was developed for use with excavators and this latest system is designed to be used with dozers, utilising much of the same hardware. Meanwhile, other EarthWorks packages are coming to market also, with systems for graders and scrapers close to launch. For these, key components in the hardware will remain the same. Martin Wagener, worldwide product implementation manager for Trimble said, “There are the same sensors for the dozer as on the excavator.”
The firm has utilised compact and rugged inertial motion sensors (IMUs), which are mounted on the roof of the dozer cab. These units measure position, motion and angles in all three axes. Solid state units, the sensors use industrial-grade versions of inertial navigation systems that would have previously only be available for the aviation sector. The units represent a major change from relying solely on GPS technology and are said to offer a far higher degree of accuracy than previous generation machine control packages for off-highway machines.
Wagener explained that mounting the dual antenna on the cab instead of on the blade as before helps to improves safety. The units are easier to mount or move and he added, “There’s no need climb onto the blade any more.”
The system is also more accurate as it now takes 100 measurements/second. Wagener said, “The target was to create a system at least as accurate as the mast mounts but we’re getting much better results.”
One of the key features for the new dozer package is over-cut protection, which is similar to that offered on the excavator system. This prevents an operator from removing too much material, eliminating the need for reworking, which can prove very costly. The system stops the dozer blade (or excavator bucket) from dipping below the levels set during the programming. At the same time, a line representation is displayed on the monitor in the cab, showing an operator exactly where to track the machine.
Another important feature of the new package is that customers for the system also benefit from a five-year software update service.
Trimble’s agreements with earthmoving machine manufacturers continue to develop also, with the company having recently agreed deals with both Doosan and Kobelco.
To meet the growing demand for grade control systems, Doosan Construction Equipment is now offering a Trimble Ready factory option for Doosan excavators. The Trimble Ready option will be available direct from the factory through Doosan Smart Solutions for use with Trimble GCS900 2D and latest 3D Grade Control Systems. The Trimble GCS900 Grade Control System gives operators access to design surfaces, grades and alignments on a display inside the excavator cab. However, the Control Boxes are not included and must be purchased directly from Trimble’s SITECH dealer channel.
The package means that the site plan and grade information can be displayed in the cab. This allows operators to finish jobs faster with minimal supervision, delivering a high precision finish, for fewer passes. At the same time, this sophisticated machine control offering means that there is no need to wait for subcontractors to provide survey and grade checking information. The package helps to reduce reworking as well as the need for stakes, hubs or stringlines. Using a virtual guidance system means that there is no risk of having to stop working should a stringline become damaged at a key stage.
Customers for Kobelco excavators also have the choice of a new Trimble Ready option for certain Tier 4 Final compliant models in the range. Customers can order the excavators from the Kobelco factory hardwired for the installation of the Trimble Earthworks Grade Control Platform. This can reduce the cost and installation time needed to install the sophisticated machine control package. Just a few hand tools are needed to make the installation, which is said to be very simple and helps to reduce machine downtime as well as cost.