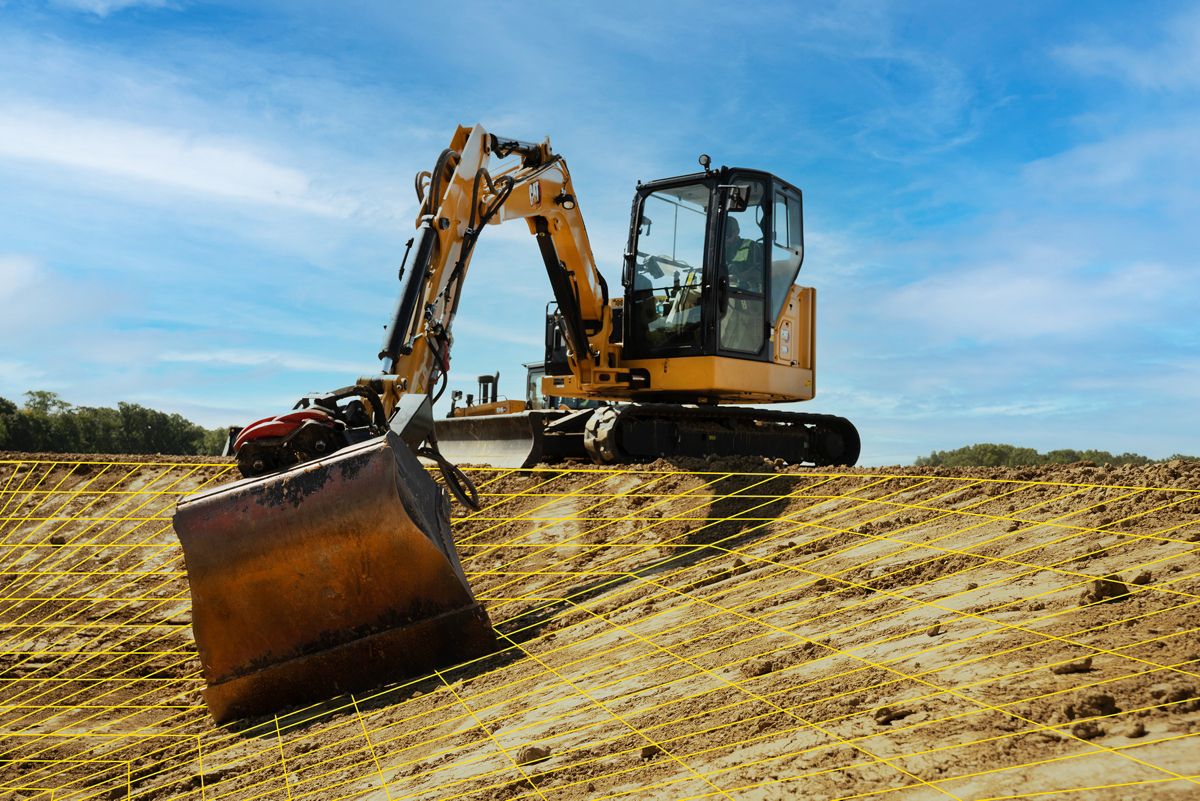
Both aftermarket grade technologies share similar capabilities with larger Cat excavators operating Cat Grade with Advanced 2D or 3D systems. A separate, high-resolution touchscreen monitor allows operators to view, create and work site designs inside the cab. Automatics deliver simple, single-joystick control over the stick and bucket to maintain grade and avoid overcutting and undercutting.
Cat Grade with Advanced 2D uses onboard processors and sensors to deliver real-time bucket tip and elevation guidance on the touchscreen. This allows operators to create and work to basic site designs, while grade design edits can be made in the cab. Field installation of the technology includes the hardware, sensors and dedicated monitor for grade plan creation, editing and viewing.
Using GPS and GLONASS systems to pinpoint location, Cat Grade with 3D allows multiple machines to grade to complex jobsite designs. The monitor shows bucket position throughout the digging motion, while height and depth audio alerts indicate when desired grade has been reached to protect from overcutting or undercutting. Beyond the hardware and sensors, including monitor, required for Grade with Advanced 2D, installation of Grade with 3D also requires GNSS receivers and antennas.
Cat Grade technologies help operators reduce the number of passes and shortens the time it takes to complete cuts. Saving costs associated with time, labour, fuel and material consumption, Cat Grade technologies allow companies to reach target grade quickly and lower overall operating costs at the jobsite.