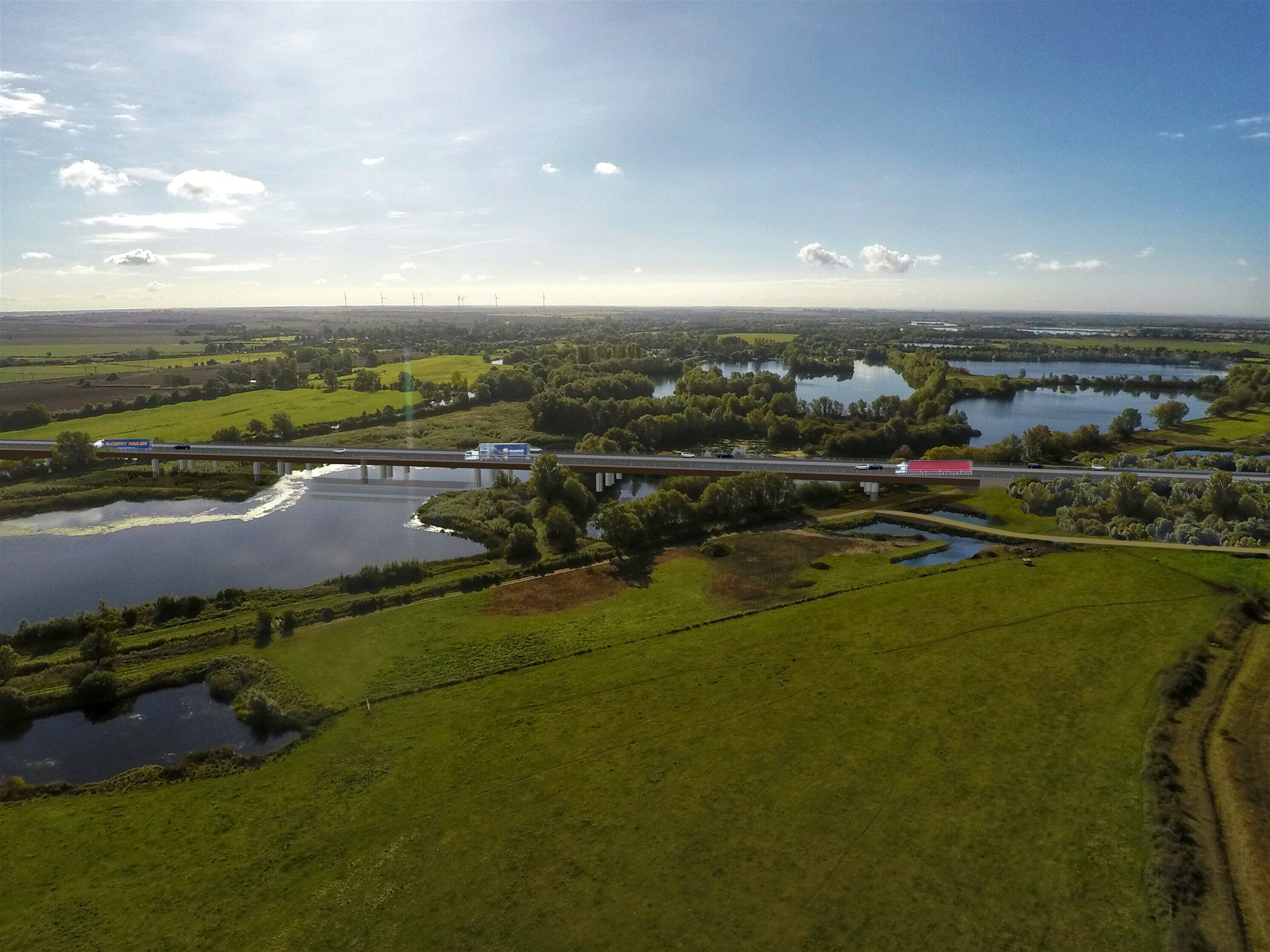
The UK is suffering badly from traffic congestion, a problem that is particularly severe in and around its major cities. Lack of investment in road construction over many years has resulted in a major backlog of work, while the country has seen growing vehicle numbers. To make matters worse, there have been few additions to the major road network since the late 1980s and early 1990s. And the combination of small island land mass, growing population and comparatively high population density has further exacerbated the problem.
So in a bid to improve traffic flow across England, several key routes are to be upgraded in a programme of works worth some €34 billion (£30 billion) running until 2025. This plan has been set out by
The A14 stretch between Cambridge and Huntingdon is one of the first stretches being upgraded. Other projects will include improving the A1 to the north of Peterborough, the A3 between London and Portsmouth, the A12 in Essex, the A50 between Stoke and Derby and the A303 between the M3 and M5. This last project includes building the controversial Stonehenge Bypass Tunnel.
The A14 has been prioritised as it is an important route, connecting the port of Felixstowe to the rest of the country. This busy road carries a high percentage of heavy trucks carrying goods to and from the port. Some of the truck traffic runs between the port and London, using the A12 and A14, which is why the former is also on the list of roads to be revamped. Meanwhile, many of the remaining trucks use the A14 as a connection between the port and the A1 to access the rest of the UK.
However, it is the stretch between Cambridge and Huntingdon in particular that has been unable to cope with the traffic volumes it has been carrying, around 85,000 vehicles/day. Delays on this section can be infuriating for drivers, who regularly get caught in long jams that are made even worse when crashes occur. As a result, an upgrade is now being carried out to the A14 for the 34km section between Ellington, to the west of Huntingdon, and the Milton junction on the Cambridge Northern Bypass. The project is being carried out by the A14 Integrated Delivery Team (A14 IDT), which is a joint venture comprising
The main focus of the project is to widen the existing road, boosting capacity sufficiently to allow the heavy traffic volumes it currently has to cope with. The scheme includes building a new bypass around Huntingdon, various junction improvements to ease the flow of traffic on and off the main route and the construction of access roads. And the work also includes widening a stretch of the A1 between Brampton and Alconbury. Construction work commenced in March 2017, with the new link due for completion in 2020 and the project is expected to cost some £1.5 billion.
Walters Group was one of two specialist firms awarded a contract by the A14 IDT to carry out the earthmoving work required to deliver the scheme. For its section of the project, this required shifting an estimated 12 million m3 of earth. The company has a modern fleet of 644 units, which includes equipment from
However, the vast scale of earthmoving work needed meant that Walters Group needed equipment and technology that would give it accurate results onsite. The team was already familiar with machine control technology and opted to use up-to-date
Andrew Burder, earthworks project manager at Walters Group/A14 IDT said that the system improves communications between the site office and the machine operators, “We message them and they’re able to message us back. They know when we’re going to use it remotely and we tell them when we’re going to play around with their system, so they know if anything will change on their screens.”
Utilising the latest machine control technology such as Topcon’s SiteLink 3D package allows the contractor to minimise the risk of machine downtime because the majority of technical issues can be resolved in real-time without needing a technician onsite.
Another benefit of machine control software is that it allows a contractor to connect the machine fleet with the office. Systems such as the SiteLink 3D package allow remote access to the machine fleet for users, so that a contractor can carry out regular tasks in real time such as file transfers, messaging and reporting and analytics.
A14 bridge link
The A14 Orwell Bridge project has won a Certificate of Excellence at the Institute of Civil Engineering’s (ICE) recent awards. The Orwell Bridge features 18 spans and has a total length of 1.3km. The bridge carries the A14 over the River Orwell and connects the port of Felixstowe to England’s strategic road network. This is a structure of notable engineering complexity and is listed as a critical infrastructure link for the UK.
Amey Consulting provided asset management and design services for Highways England Area 6 which included this structure. The asset management process involved data capture through automatic sensors installed throughout the bridge. The company used this data in risk management focused research to advance understanding of the bridge behaviour and ensuring safe and whole-life cost-effective operation of the asset.
Bogdan Tutoveanu, Technical Director for Amey Consulting said, “We’re delighted that our work on the management of the Orwell Bridge has been recognised by the ICE. The Orwell Bridge is a vital link between the port of Felixstowe and the rest of the UK, and maintenance of this asset supports huge economic activity. This project has been an outstanding example of Highways England and Amey Consulting working together to benefit Highways England, and the local economy.”
Burder commented that the information the contractor can feed into a machine control package in real time and the live data that can be recovered make this type of technology extremely valuable. He said, “We can see instantly where the machines are, what programme they’re working on, what construction offset they’re working to and which areas they’re working in – so we know instantly if they’re working on the right model and at the right level.”
For surveying tasks also, machine control systems offer major gains in efficiency. Mark Lawton, survey manager for the A14 IDT, said, “We’ve got the data links out there so we can send data from the office to the machines, and another critical factor is that the people planting phase has been reduced – there are no people working around the machines.”
With fewer surveying personnel having to work around machines in use, site safety is improved considerably, while Lawton added, “The quality of the data being sent to the machines is always consistent too.”
From the civil engineering perspective, one of the most challenging aspects has been the construction of a new viaduct carrying the A14 across the River Great Ouse. The bypass is to the south of Huntingdon and is located a distance from the existing A14, which is helping to reduce traffic disruption during its construction. The 750m viaduct presents challenges as it is being built over a flood plain area. One of the first steps was to install a 52tonne pontoon and a temporary bridge, giving heavy equipment access to the river area and allowing construction of the actual viaduct. The viaduct sits on columns supported by piled foundations and features 800 precast concrete panels, which are being manufactured onsite to help reduce truck movements in the area.
With the roadway being prepared, the surfacing operation is now being planned. Aggregate Industries was recently selected by the A14 IDT to deliver the surfacing for the A14 upgrade project. The company was awarded the contract for paving the 34km stretch of the multilane carriageway over a 30-month period. To minimise truck movements in the area, which would further add to the heavy congestion, the firm is carrying out the surfacing work using local primary and secondary aggregate. This reduces the distances that aggregate supplies have to travel, rather quarries some distance away.
The history challenge
With the reconstruction of the A14 between Cambridge and Huntingdon has come an additional challenge. The area has been a focus for human activity over millennia, so as well as the construction work there was also a planned programme of archaeological research, amongst the biggest ever such projects. Some 250 archaeologists, led by archaeology experts MOLA Headland Infrastructure, have dug over 40 separate excavation areas, uncovering new information about how the landscape was used. This is the first time archaeological digs have been carried out in the area and this work has been carried out ahead of the construction phase.
The research revealed that the 350ha area has been occupied by people for 6,000 years. With most of the archaeological programme now being completed, finds so far date from the Neolithic, Bronze and Iron Ages, as well as the Roman, Anglo-Saxon and Medieval periods.
Cambridgeshire County Council’s senior archaeologist in the Historic Environment Team, Kasia Gdaniec, said, “Earlier prehistoric Neolithic and Bronze Age ceremonial and burial monuments that are 5,500 and 4,000 years old, have also been investigated, but the new Roman pottery industry that has emerged from sites in the Brampton area and at the new Great Ouse bridge sets apart the host sites from others traditionally dug in the county.”
Important ancient finds have so far included three Neolithic henges that were nearly 50m in diameter and that would have had major ceremonial and territorial functions. During the period of the Roman Empire, the area hosted a trade distribution area, linked to the surrounding farmsteads by trackways as well as the main Roman road between Cambridge and Godmanchester.
The area was also active during Anglo-Saxon times as highlighted by the discovery of a large tribal territorial boundary with large ditches, gated entrance and a beacon located on top of a hill. An abandoned medieval village was also found dating from the 12th century, with 12 dwellings in a 6ha area, and with evidence of up to 40 earlier wooden structures on the same site dating back to the Anglo-Saxon period.
Dr Steve Sherlock, archaeology lead for the A14 Cambridge to Huntingdon project for Highways England, said, “The archive of finds, samples and original records will be stored so that the data and knowledge is preserved for this and future generations.
“We now have the evidence to rewrite both the prehistoric and historic records of the area for the last 6,000 years.”
The firm’s contract involves supplying and installing 700,000tonnes of asphalt and 500,000tonnes of cement bound granular material (CBGM). And the package of works was awarded after a 12-months process of Early Contractor Involvement (ECI).
To increase efficiency for the project Aggregate Industries invested in a new £3.5 million mobile asphalt plant, capable of producing 240tonnes/hour, and is erecting two further mobile mixing plants within the site compounds. Having the asphalt plants sited close to the paving operations is also helping to lower truck movements of asphalt, again as haulage distances will be shorter than had the materials come from plants located further away. And the firm has said that locating the plants onsite will lower the impact of operations on the local community and the network.
Given the existing congestion problem, it was recognised by the client that effective traffic management would be another crucial component during the construction schedule. The idea was to minimise the effects of congestion caused by the construction activity, so as to optimise traffic flow as much as possible. Managing the traffic minimises delays, while this can also help to improve safety for personnel in the working areas.
To handle the traffic passing through the work zone and to keep drivers informed, Highways England has installed sophisticated messaging systems. A specialist supplier, MVIS, was contracted by the A14 IDT to deploy a DATEX solution with variable message signs (VMS). In all, 26 of the Bartco UK VMS-C signs are being used to display journey times from their locations to the end of the affected stretch of road. These units provide drivers with information about journey times and, where possible, also suggest alternative routes.
The journey times displayed to drivers are calculated using the DATEX II system, based on data collected from in-vehicle sensors. The VMS units then renew the times they display every five minutes.