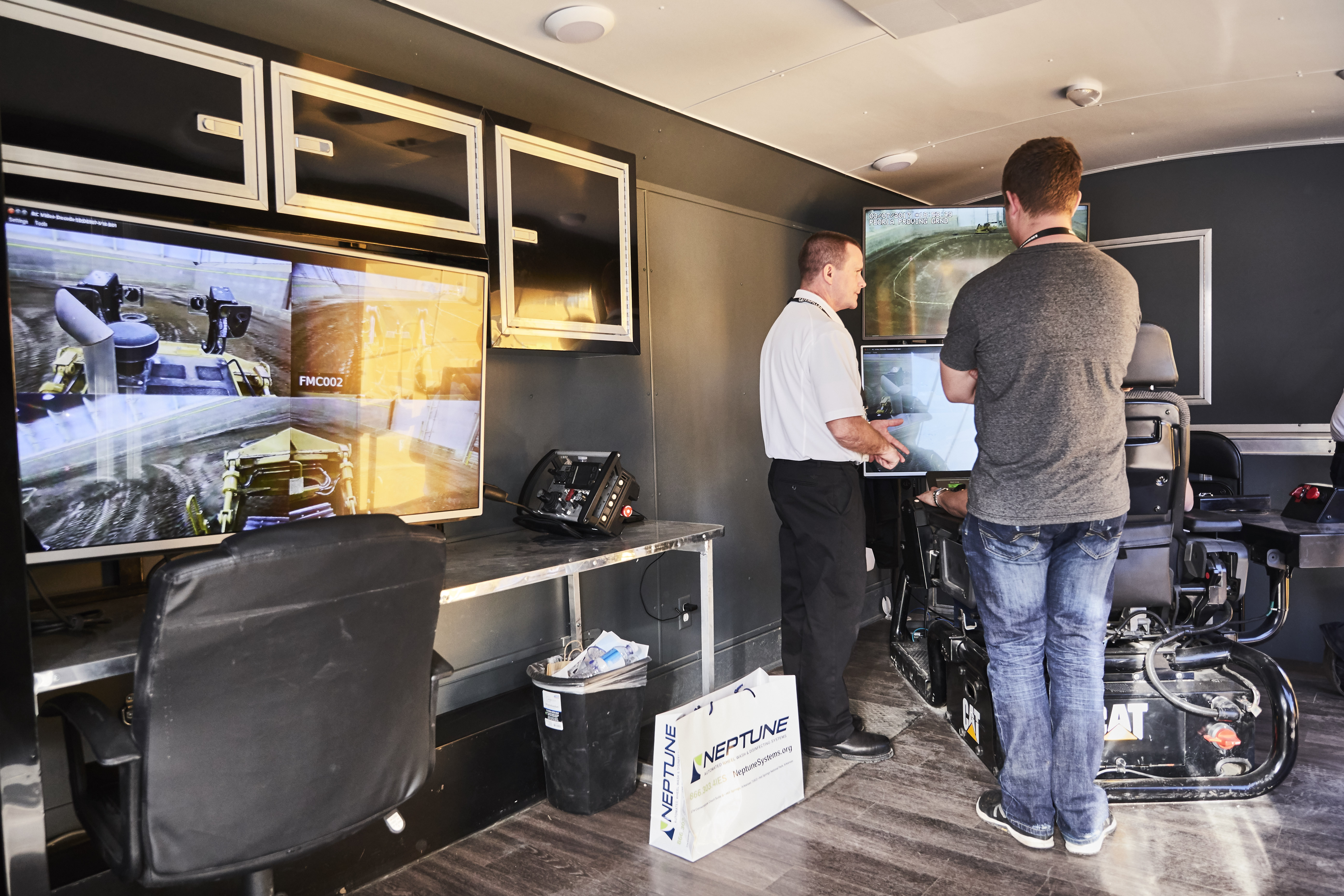
Machine control technology plays an increasingly important role in construction. The pace of development has been fast, with new systems offering major gains in both productivity and quality across a range of applications. At the recent
One of the notable demonstrations was of a
According to Brad Van De Weer, CAT market professional, heavy equipment, the system feels as though you are actually operating from the cab. “We have full controllability of the machine,” he said. “If I turn the throttle up and release the park brake I can raise the blade up and down, turn it right and left, I can raise and lower the ripper and control the travel controls on the left hand side of the controls.”
“It’s as if you were in the machine itself, very little time delay with operation, it’s very controllable, smooth and productive. The camera systems are placed in areas to simulate the operator’s view from the cab, but you actually gain in terms of perspective. The features and benefits are focused on safety - we don't want operators putting themselves in danger.”
“The system was initially developed for mining applications being installed on our D10s and D11s. Now that it’s been made available on our construction line, there’s a lot of demand for it on our D8T. We are focused on dozers for now but we’re looking to implement this technology in wheeled loaders and excavators soon.”
Also suited to earthmoving applications is the new Earthworks package from
This is bringing a significant innovation for the earthmoving market, he added. “We’re delivering excavator automation. For example, our system will control the bucket and the boom will go up or down to stay in profile.”
Although the system is limited to controlling the bucket, boom and dipper functions, this ensures that digging can be made precisely to grade. And he explained that the system is well suited to excavating slopes or cleaning up trench bottoms, for example. Trimble believes that the system will deliver a substantial gain in output and Drake said, “What we’re seeing is a 30° increase in production. It’s a lot more ergonomic and we find operators can take their hands off the controls on this new architecture.”
The system is based on commonly-available technology, which benefits the user. Drake said, “It’s an
Because the four sensors respond rapidly, the readings are fed back immediately so there is no risk of digging out too much before the system has time to respond. The new inertial measurement units (IMUs) are designed to be rugged and durable and can be used on excavators as well as dozers and graders. The IMU system is also connected to the internet, so that a contractor can view machine progress remotely - and this also allows for real-time data flow on production rates to give an accurate picture of site progress.
Further developments are planned and Drake said that the architecture will also give plenty of scope for additional functionality in the future, with links to systems from other divisions within Trimble to boost overall capabilities.
Meanwhile
The new Z-Robot is an advanced robotic total station with integrated Z-beam laser technology. The Z-Robot is designed to provide a hybrid function of high-precision, optically-based vertical accuracy control and the convenience of Z-beam laser positioning to maintain that accuracy across the paver.
“The ZPS system’s self-levelling Z-Robot cuts set-up time in half compared with previous concrete paving methods,” said Murray Lodge, senior vice president and general manager of Topcon’s Construction Business Unit. “With traditional systems, you need multiple, expensive robotic total stations to control the paver at any given time and at least another complete set of instruments for downrange transition. With the ZPS system, only one Z-Robot controls the paver - increasing productivity and profitability, and dramatically lowering the cost of the solution compared to LPS.”
On board the paver, the ZPS system uses the new Topcon Z-Stack modular-designed system that seamlessly integrates GPS, optical targeting and Z-beam reception into one unit by interlocking the required sensing technologies in one rugged ‘stack’.
“The Z-Stack sensor is revolutionary,” said Lodge. “It combines time-proven Topcon positioning technologies into one multi-functional, consolidated and complete system that provides better accuracies and more efficient paving than ever before. The system requires no separate base station and only one cable needed for power and connectivity.
“The system also offers a wider working area, with a range of up to 150 more feet than with traditional methods — minimising instrument transitions,” said Lodge.
At the same time,
The Leica iRD3/iRP3 solutions are said to deliver a 30% time and cost saving with every drilling/piling job. The systems drastically reduce the need for stakeout work. Among other features, they also offer wireless update of project files and remote support via telematics. Users can document work as the project progresses and avoid drilling in old and failed holes.
The Leica iCON rig solution is integrated into the Liebherr control system for efficient positioning of machines and their working tools. The LIPOS data interface combines Liebherr machine-based sensor data with the GPS navigation system from Leica Geosystems.
From Hemisphere GNSS come solutions that allow OEMs to develop their own machine control systems in-house. The GradeMetrix software means that OEMs can build their own branded software and hardware for high-precision GNSS-based machine control and guidance systems. The GradeMetrix package means that heavy equipment firms can tailor their own machine control solutions to the needs and working applications of their own products. The GradeMetrix application software is also offered with an array of compatible GNSS hardware components. These include IronOne Rugged Display & Computer and C321 RTK Base & Rover.
In addition the firm is offering new systems, designed specifically for harsh machine control environments. Its multi-frequency, multi-GNSS smart antenna offers precise heading, RTK positioning, and easy installation. VR500 adds another system component and empowers heavy equipment manufacturers to deliver their own machine control and guidance solutions to their customers.
VR500 is said to suit tough machine control environments, meeting IP ingress and MILSTD202G shock and vibration requirements. A fully scalable solution, the VR500 tracks GPS, GLONASS, BeiDou, Galileo, QZSS, and IRNSS, and is also
And newly developed receivers from the Topcon Positioning Group also offer accurate location for the OEM market. The two new B111 and B125 boards are full constellation GNSS receivers designed for use with a broad range of positioning applications. The boards can use the GPS, GLONASS, BeiDou and Galileo constellations with the B111 tracking signals in the L1 and L2 frequency band, while the B125 adds signals in the L5 band. Both boards are designed to provide scalable positioning from sub-metre DGPS positioning to sub-centimetre RTK positioning.
Both boards include 226-channel Vanguard Technology with Universal Tracking Channels. According to Topcon, the addition of BeiDou and Galileo constellation tracking along with GPS, GLONASS, SBAS and QZSS functionality ensures the boards offer optimum performance.
Meanwhile, the dual frequency B111 board has a low power consumption and a versatile communication interface, making it easier for OEMs to integrate the compact board into any precise positioning application. The board also includes an SD card interface designed to provide quick and easy support for data logging in addition to Quartz Lock Loop technology for GNSS tracking in high-vibration environments.