Telematics is giving contractors a greater oversight of the location and performance of their machinery
In simple terms, telematics is any integrated use of telecommunications and ICT (information and communications technology). It concerns the sending, receiving and storing of information via telecommunication devices.
Typically, this is in conjunction with machine or device control and includes use of global positioning systems, or GPS.
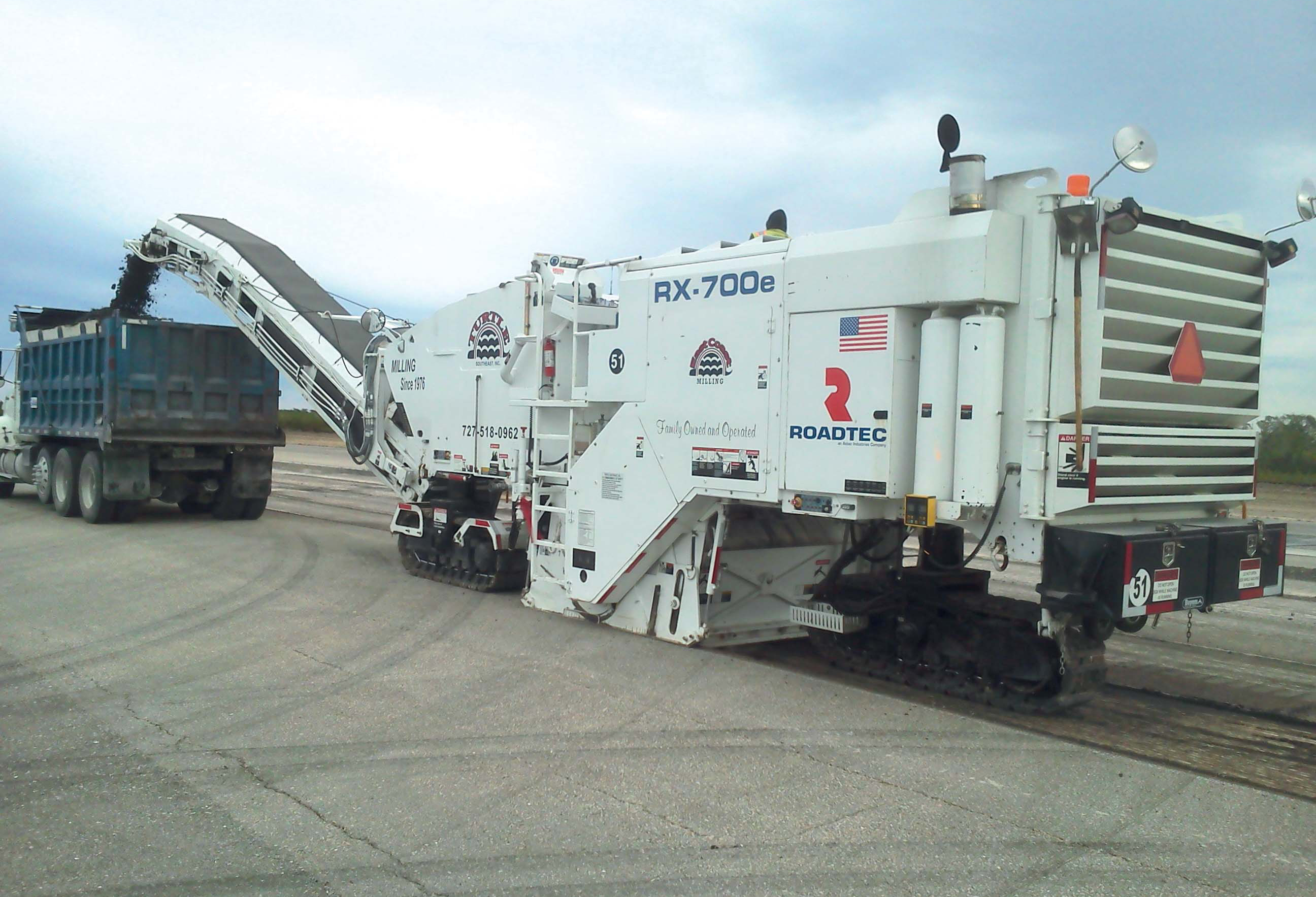
Roadtec to the rescue
Telematics is giving contractors a greater oversight of the location and performance of their machinery
In simple terms, telematics is any integrated use of telecommunications and ICT (information and communications technology). It concerns the sending, receiving and storing of information via telecommunication devices.
Typically, this is in conjunction with machine or device control and includes use of global positioning systems, or GPS.
The real revolution is in the software that translates this information into useful readable data upon which decisions are made. Software uses the information to control production, monitor progress and send out alerts.
Telematics offers contractors the ability to monitor where their equipment is located in real time, which machines are running and the level of productivity being achieved. With GPS and 3-D digital site models, machines can grade, compact, mill and pave with astounding accuracies. Machines can also “tell” owners when it is time for scheduled maintenance and diagnose the cause of mechanical and hydraulic issues.
Telematics systems consist of software, on-machine viewing screens, and wireless signal boosters to send and receive data at the machine. Numerous functions, such as engine data and fuel consumption, can be viewed at the machine, on the owner’s computer screen from a remote location and by a system providers’ support personnel.
“We have developed a custom remote diagnostic system for our machines that can address a problem and correct it to maintain the contractor’s productivity,” says Max Peters, account manager with1252 Roadtec. “Our Roadtec Guardian Telematics System consists of software, on-machine viewing screens and wireless signal boosters to send and receive data from a machine.”
Numerous functions such as engine performance and fuel consumption can be viewed by the machine’s operator or on a computer screen from a remote location. The data can tell company personnel if an engine is faltering, how much fuel is being burned, if the engine is idle, how long it’s been idling and where the engine is located.
Fleet management can help track assets and save time when a need emerges for a piece of heavy equipment that may be sitting idle on the other side of a jobsite or at another location. Engine diagnostics can prevent costly workflow slow-downs or stoppages.
Engine diagnostics is extremely important. “We’ve taken the next logical step with telematics and can diagnose why a machine’s engine has stopped,” Peters says. “Telematics can tell the contractor that the engine has stopped, whereas our system tells why.”
Telematics promises to tell operators why the engine won’t start, such as a failed neutral switch on a propel joystick or possibly an E-Stop that isn’t activated because a wire is loose. Or perhaps a circuit breaker didn’t “pop”, but failed internally. Additionally, the contractor will be able to see battery voltage levels when cranking the engine.
With telematics, it is possible to monitor and troubleshoot everything from the machine’s fuel consumption to engine codes; starting circuits to cutter circuits; and the machine’s propel functions, load controls, hydraulics, steering circuits, and grade and slope settings. Everything can be seen instantly, even the exact location of the machine via GPS.
With Roadtec’s Guardian, technicians are available 24/7. The support staff technicians see the same machine circuits and systems as live schematics that the contractor sees and can guide them through a fix or do it for them remotely.
But how does it work in practice?
“Our support centre receives a notice from a milling machine working in Florida reporting that the signal from the left front pulse pickup was lost,” says Peters. “A pulse pickup monitors the speed of the hydraulic motors that drive the tracks. On this particular machine, the left front track pulse pickup value showed zero and all other track pulse pickup values were normal.”
A support centre engineer then logs into that machine in Florida and confirms the condition. The engineer calls the machine owner to alert him of a problem and the customer quickly finds a broken wire.
“The problem was corrected within 30 minutes from the time we received the notice,” says Peters. “Help from technical service is only a phone call away.”
In simple terms, telematics is any integrated use of telecommunications and ICT (information and communications technology). It concerns the sending, receiving and storing of information via telecommunication devices.
Typically, this is in conjunction with machine or device control and includes use of global positioning systems, or GPS.
The real revolution is in the software that translates this information into useful readable data upon which decisions are made. Software uses the information to control production, monitor progress and send out alerts.
Telematics offers contractors the ability to monitor where their equipment is located in real time, which machines are running and the level of productivity being achieved. With GPS and 3-D digital site models, machines can grade, compact, mill and pave with astounding accuracies. Machines can also “tell” owners when it is time for scheduled maintenance and diagnose the cause of mechanical and hydraulic issues.
Telematics systems consist of software, on-machine viewing screens, and wireless signal boosters to send and receive data at the machine. Numerous functions, such as engine data and fuel consumption, can be viewed at the machine, on the owner’s computer screen from a remote location and by a system providers’ support personnel.
“We have developed a custom remote diagnostic system for our machines that can address a problem and correct it to maintain the contractor’s productivity,” says Max Peters, account manager with
Numerous functions such as engine performance and fuel consumption can be viewed by the machine’s operator or on a computer screen from a remote location. The data can tell company personnel if an engine is faltering, how much fuel is being burned, if the engine is idle, how long it’s been idling and where the engine is located.
Fleet management can help track assets and save time when a need emerges for a piece of heavy equipment that may be sitting idle on the other side of a jobsite or at another location. Engine diagnostics can prevent costly workflow slow-downs or stoppages.
Engine diagnostics is extremely important. “We’ve taken the next logical step with telematics and can diagnose why a machine’s engine has stopped,” Peters says. “Telematics can tell the contractor that the engine has stopped, whereas our system tells why.”
Telematics promises to tell operators why the engine won’t start, such as a failed neutral switch on a propel joystick or possibly an E-Stop that isn’t activated because a wire is loose. Or perhaps a circuit breaker didn’t “pop”, but failed internally. Additionally, the contractor will be able to see battery voltage levels when cranking the engine.
With telematics, it is possible to monitor and troubleshoot everything from the machine’s fuel consumption to engine codes; starting circuits to cutter circuits; and the machine’s propel functions, load controls, hydraulics, steering circuits, and grade and slope settings. Everything can be seen instantly, even the exact location of the machine via GPS.
With Roadtec’s Guardian, technicians are available 24/7. The support staff technicians see the same machine circuits and systems as live schematics that the contractor sees and can guide them through a fix or do it for them remotely.
But how does it work in practice?
“Our support centre receives a notice from a milling machine working in Florida reporting that the signal from the left front pulse pickup was lost,” says Peters. “A pulse pickup monitors the speed of the hydraulic motors that drive the tracks. On this particular machine, the left front track pulse pickup value showed zero and all other track pulse pickup values were normal.”
A support centre engineer then logs into that machine in Florida and confirms the condition. The engineer calls the machine owner to alert him of a problem and the customer quickly finds a broken wire.
“The problem was corrected within 30 minutes from the time we received the notice,” says Peters. “Help from technical service is only a phone call away.”