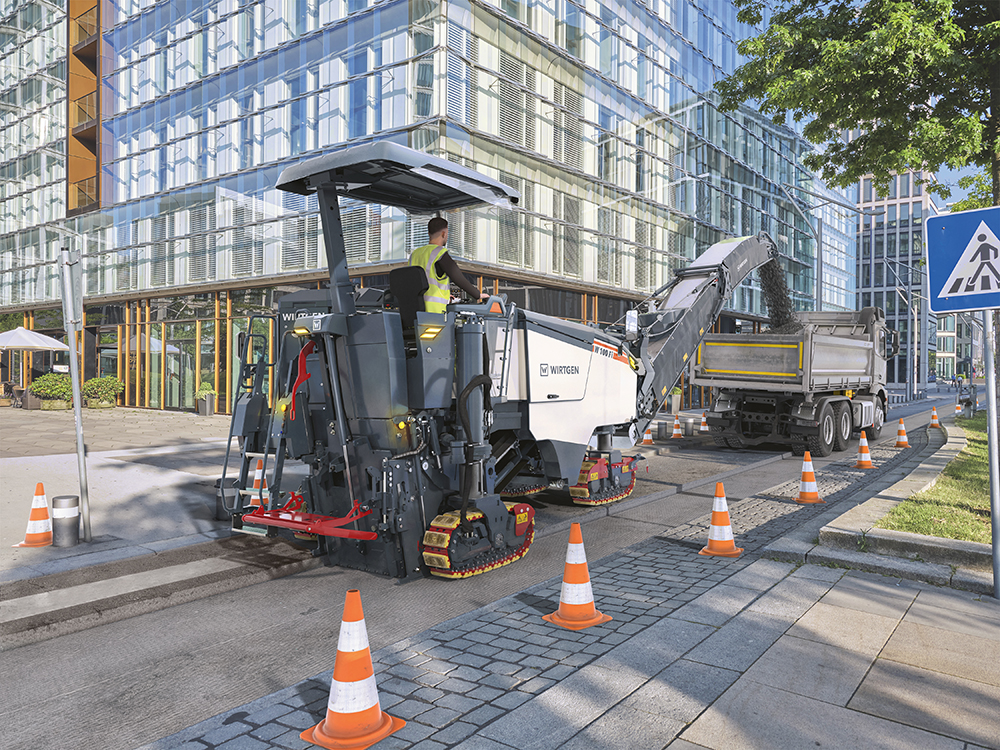
At the beginning of this year. WIRTGEN celebrated the market launch of its completely redesigned generation of compact milling machines. Industry-leading state-of-the-art technologies from the proven F-series large milling machines have now been integrated in the W 100 Fi, W 120 Fi and W 130 Fi compact milling machines. WIRTGEN will also be showing another innovation at Bauma 2022. For the first time, compact class machines can be fitted with a comfort cabin. This not only increases the safety of machine operators, but also the comfort of their workplace.
The first WIRTGEN Cold Milling Machine with Environmentally Friendly Engine Technology from John Deere
The front loaders with working widths of 1.0 m, 1.2 m and 1.3 m feature the latest and currently most environmentally friendly engine technology compliant with EU Stage 5 / US Tier 4 Final exhaust emission standards. The state-of-the-art diesel engine delivers a rated output of 265 kW / 355 hp. Wirtgen and John Deere have precisely tuned the torque characteristic of the engine to meet the specific needs of the cold milling process. The engine already delivers sufficient torque at engine speeds as low as 1,200 rpm, achieves maximum torque at 1,500 rpm and offers a very wide working speed range of 1,200 to 2,100 rpm. As a result, the machines use significantly less fuel, even when delivering the highest productivity and milling at the maximum depth of 330 mm.
Mill Assist and WPT for the One-Meter Class
Also onboard are the digital assistance systems Mill Assist, Wirtgen Performance Tracker (WPT) and the Level Pro Active leveling system, which have already delivered customer benefit in the F-series large milling machines. Now, customers can look forward to the benefits of high milling performance, maximum efficiency, and clear documentation in the compact milling machine class.
Mill Assist for Increased Milling Efficiency
In automatic mode, Mill Assist selects the operating strategy with the most favorable balance between milling performance and operating costs. This increases milling performance while simultaneously reducing not only diesel fuel, water, and pick consumption, but also CO₂ emissions.
Mill Assist automatically controls the engine speed and simultaneously provides a wide range of usable milling drum speeds for an enormous spectrum of applications. The low-speed range enables significant reductions in fuel consumption and minimizes pick wear. The upper speed range enables the achievement of an optimal milling pattern, even in the case of higher area performance rates.
The operator can additionally select one of three operating strategies for each milling job: “ECO”, “performance-optimized” or “milling pattern quality”. This makes it possible, for example, to pre-define the required milling pattern quality incrementally from coarse to very fine at the press of a button.
A Wide Range of Applications and Maximum Flexibility
Compact dimensions and optimized machine weight for easy transportation predestine these machines for a multitude of different construction site scenarios. Whether on highways, main roads, parking lots or inner-city streets – these high-performance machines are ideal for a broad spectrum of applications. Due to their outstanding productivity, they are ideal for surface layer rehabilitation and complete pavement removal on construction sites of all sizes. Thanks to the ability to quickly change the FCS milling drums with different pick spacings and working widths, the compact milling machines from Wirtgen can also be rapidly reconfigured on-site to adapt to changing applications.
Precise Leveling with LEVEL PRO ACTIVE
Already proven in the F-series large milling machines, the LEVEL PRO ACTIVE leveling system has now been made available for the compact class milling machines. Developed by Wirtgen especially for cold milling machines, the leveling system features informative operating panels and is intuitive and easy to use. All connected sensors and measured values are clearly displayed on the operating panel to make the work processes as efficient as possible. The system is fully integrated in the control system of the cold milling machine and, as essential machine functions are directly interconnected, provides a high level of automation. The system also offers many automatic and additional functions that make the operator’s job easier, for instance, automatic lifting for driving over manhole covers.
State-of-the-art cockpit, also available with an enclosed cabin
The newly developed operator’s cabin is characterized by ergonomically designed control elements with high-quality haptics and maximum ease of operation. In addition to the slender wasp waist of the machine, up to five on-board cameras provide an ideal view of all important working areas. The new 5-inch control screen in the multifunctional armrest displays all machine-relevant information. The access ladder to the cabin at the rear of the machine is fitted with an automatic height adjustment system. This assures that the machine operator can easily and safely access the platform in all working situations.
At Bauma 2022, WIRTGEN is showing another innovation in the compact milling machine class – a completely enclosed comfort cabin. It protects the operator against typical problems such as noise and dust on the construction site and provides ideal working conditions in all kinds of weather.
Content produced in association with Wirtgen Group