A new Trimble LOADRITE product is connecting quarries like never before, helping to find both immediate gains and long-term solutions. The new LOADRITE product, InsightHQ: The Connected Quarry, tracks three core areas: extraction, processing and load out, said John Vaassen, regional manager with Trimble LOADRITE. Tracking those main business drivers helps provide information crucial to the decision-making process. That applies to short-term challenges, such as prioritising trucking, to long-term decisions
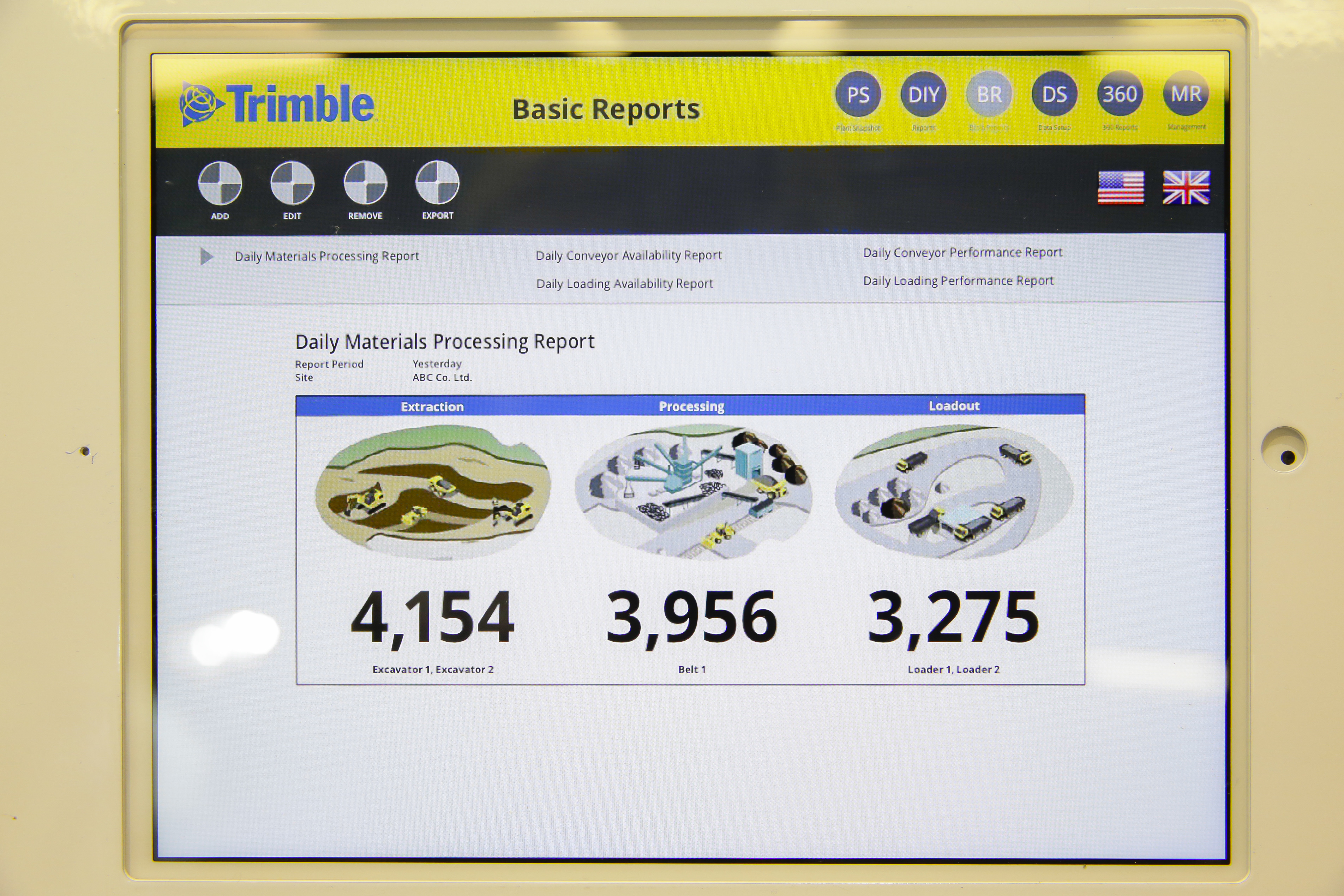
Trimble’s LOADRITE technology connects data from every phase of a quarry site.
A new 2122 Trimble 5004 LOADRITE product is connecting quarries like never before, helping to find both immediate gains and long-term solutions.
The new LOADRITE product, InsightHQ: The Connected Quarry, tracks three core areas: extraction, processing and load out, said John Vaassen, regional manager with Trimble LOADRITE. Tracking those main business drivers helps provide information crucial to the decision-making process. That applies to short-term challenges, such as prioritising trucking, to long-term decisions including equipment purchases.
The data – available at fixed and mobile locations – provides efficiencies in the individual areas while also delivering a complete picture, Vaassen said. “It’s truly a system that benefits the entire site.”
Finding an efficiency in one area leads to gains in others, Vaassen said. He offered an example where the technology created an immediate 18% gain by optimising haulage from 36 to 42tonnes per cycle. “Through continuous improvements, they eventually were able to increase their loading to 66tonnes per cycle,” Vaassen said.
Implementation of the system is easy, he said. “All members of the operation can easily learn how to use it. Everyone can see it every day. It makes the information more relevant. It’s not just the wheel loader operator or the management.”
The new LOADRITE product, InsightHQ: The Connected Quarry, tracks three core areas: extraction, processing and load out, said John Vaassen, regional manager with Trimble LOADRITE. Tracking those main business drivers helps provide information crucial to the decision-making process. That applies to short-term challenges, such as prioritising trucking, to long-term decisions including equipment purchases.
The data – available at fixed and mobile locations – provides efficiencies in the individual areas while also delivering a complete picture, Vaassen said. “It’s truly a system that benefits the entire site.”
Finding an efficiency in one area leads to gains in others, Vaassen said. He offered an example where the technology created an immediate 18% gain by optimising haulage from 36 to 42tonnes per cycle. “Through continuous improvements, they eventually were able to increase their loading to 66tonnes per cycle,” Vaassen said.
Implementation of the system is easy, he said. “All members of the operation can easily learn how to use it. Everyone can see it every day. It makes the information more relevant. It’s not just the wheel loader operator or the management.”