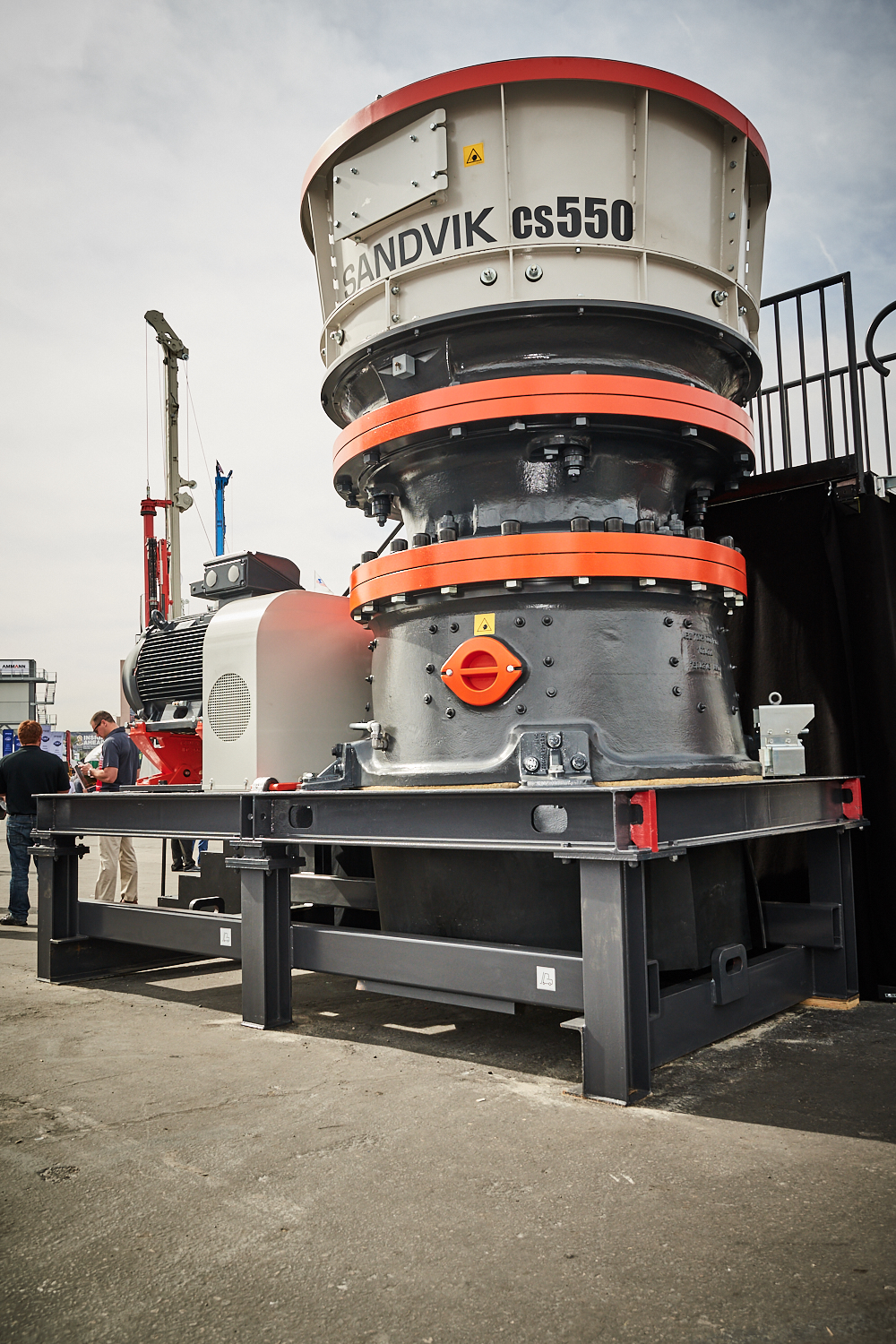
A key goal in any crushing operation is to accomplish more work – essentially the sum of crusher capacity and reduction ratio – in each crushing stage while never losing sight of overall efficiency. Sandvik CS550, the latest cone crusher which complements the first two 500-series crushers - Sandvik CH550 and Sandvik CH540 - does exactly this.
The Sandvik CS550 is a reliable, high-capacity and high-reduction workhorse for the secondary crushing stages. While nothing prevents Sandvik CS550 from being used in mining applications, its primary mission is construction.
From a practical standpoint this means aggregate quarries, while contractors looking for mobile solutions may also benefit.
Up to 25% higher reduction ratios can be achieved by the Sandvik CS550 compared to similar types of crushers. This enables a more efficient process already in the secondary stage and relieves the tertiary stage of some of its size reduction load, allowing a sharper quality focus. Furthermore, it decreases the recirculating load by up to 50% with no decrease in the output of high-value product. This means less material goes back into the crusher to be reprocessed, extending the service life of the wear parts, particularly the costly manganese steel used in the crushing chamber.
“Sandvik CS550 has a big intake to match the jaw crusher in the primary stage, with the possibility to produce large volumes, delivering a high reduction ratio and an excellent shape of the end product,” says Martin Johansson, life cycle manager cones and gyratory crushers with Sandvik Mining & Rock Technology. “The wide range when it comes to closed side settings, together with more and bigger throws, gives you extreme flexibility as Sandvik CS550 can be set to fit a huge variety of application needs.”
The CS550 also works well in round the clock mining operations where it is all about tonnage and extreme reliability with minimum downtime. More reduction in the secondary stage means more final product to bypass tertiary crushing. Less recirculation means less wear and less downtime.
A major competitiveness factor for Sandvik CS550 in all applications is the complete elimination of plastic backing materials in the crushing chamber and substantial improvements in the maintenance ergonomics, including extensive commonalities with other Sandvik cone crushers.
The automatic setting regulation system, which comes as standard with the crusher, optimises crusher operation for efficiency and adapts to variations in feed conditions by means of continuous liner wear measurement and compensation. The Hydroset system provides automatic hydraulically powered mainshaft positioning and overload protection to permit the passage of uncrushables. The automation and control system offered as standard for Sandvik 500-series crushers ensures optimal capacity and reduction settings for the high-powered equipment.