A key introduction from Kleemann is its new MOBICONE MCO 11 PRO mobile cone crusher. This is the first model in the high-performance PRO Line and has been designed as a mobile unit that can be tracked into position in quarry operations to increase its versatility.
This productive machine can process up to 470tonnes/hour depending on the material type and is driven by a diesel electric drive system that is said to be highly efficient, lowering fuel consumption. Because the machine has an electric drive it c
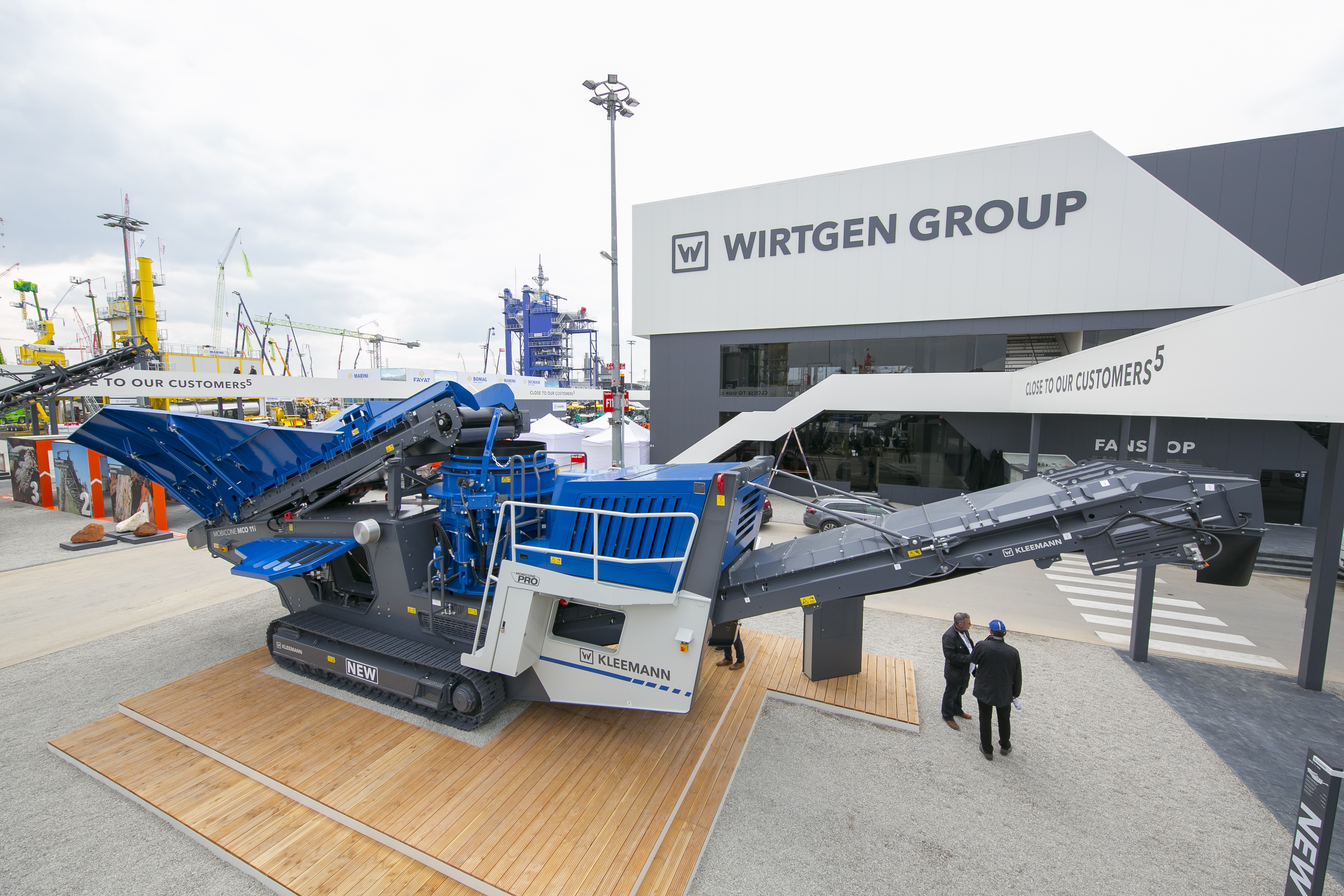
Kleemann’s new cone crusher offers high productivity
A key introduction from 261 Kleemann is its new MOBICONE MCO 11 PRO mobile cone crusher. This is the first model in the high-performance PRO Line and has been designed as a mobile unit that can be tracked into position in quarry operations to increase its versatility.
This productive machine can process up to 470tonnes/hour depending on the material type and is driven by a diesel electric drive system that is said to be highly efficient, lowering fuel consumption. Because the machine has an electric drive it can be run from an electric cable once in position onsite, which reduces fuel consumption although it can also use the 371kW diesel engine if there is no power available.
The highly sophisticated crusher can be linked to other Kleemann crushing and screening plants, allowing for an optimum flow of material through the reduction process. The key feature of the unit is its redesigned cone crusher, which is now driven by a 250kW electric motor. Product quality is said to be optimised due to the fully automatic gap setting feature that allows adjustments to be made during operation. The machine can be further optimised during use as it has a feeder unit that can be moved hydraulically, allowing the discharge pattern to be changed. The machine is equipped with Kleemann’s proven Continuous Feed System (CFS), which can adapt conveying capacity of the feed conveyor depending on the crusher level. The system ensures that the crusher maintains its optimum filling height, allowing continuous production of a high-quality output. When the plant is operated along with a Kleemann primary crusher, the CFS also controls the material feed of the upstream crushing stage to deliver optimum throughput for the entire stream. The machine has a sophisticated control system operated through a touchscreen that displays machine status and fault locations as well as plant functions.
Other features include ease of maintenance and transportation, ensuring high uptime and high mobility. The operator can refuel the plant from the ground or change the crushing tool without the need for sealing compound. The 48tonne machine can also be transported in one, without the need to disassemble machine parts allowing it to be commissioned more quickly once on site.
This productive machine can process up to 470tonnes/hour depending on the material type and is driven by a diesel electric drive system that is said to be highly efficient, lowering fuel consumption. Because the machine has an electric drive it can be run from an electric cable once in position onsite, which reduces fuel consumption although it can also use the 371kW diesel engine if there is no power available.
The highly sophisticated crusher can be linked to other Kleemann crushing and screening plants, allowing for an optimum flow of material through the reduction process. The key feature of the unit is its redesigned cone crusher, which is now driven by a 250kW electric motor. Product quality is said to be optimised due to the fully automatic gap setting feature that allows adjustments to be made during operation. The machine can be further optimised during use as it has a feeder unit that can be moved hydraulically, allowing the discharge pattern to be changed. The machine is equipped with Kleemann’s proven Continuous Feed System (CFS), which can adapt conveying capacity of the feed conveyor depending on the crusher level. The system ensures that the crusher maintains its optimum filling height, allowing continuous production of a high-quality output. When the plant is operated along with a Kleemann primary crusher, the CFS also controls the material feed of the upstream crushing stage to deliver optimum throughput for the entire stream. The machine has a sophisticated control system operated through a touchscreen that displays machine status and fault locations as well as plant functions.
Other features include ease of maintenance and transportation, ensuring high uptime and high mobility. The operator can refuel the plant from the ground or change the crushing tool without the need for sealing compound. The 48tonne machine can also be transported in one, without the need to disassemble machine parts allowing it to be commissioned more quickly once on site.