Kleemann has launched two new impact crushers, the Mobirex MR 110 ZSi EVO 2 and MR 130 Zi EVO 2.
“EVO 2 represents the continuing evolution of the successful EVO Contractor Line, with additional benefits in terms of economy and operational safety,” said Mark Hezinger, marketing manager.
The new impact crushers are differentiated by their size and productivity with the MR 110 ZSi EVO 2 having a crusher inlet opening of 1,100mm, and the MR 130 Zi EVO 2 a crusher inlet opening of 1,300mm. These provide feed
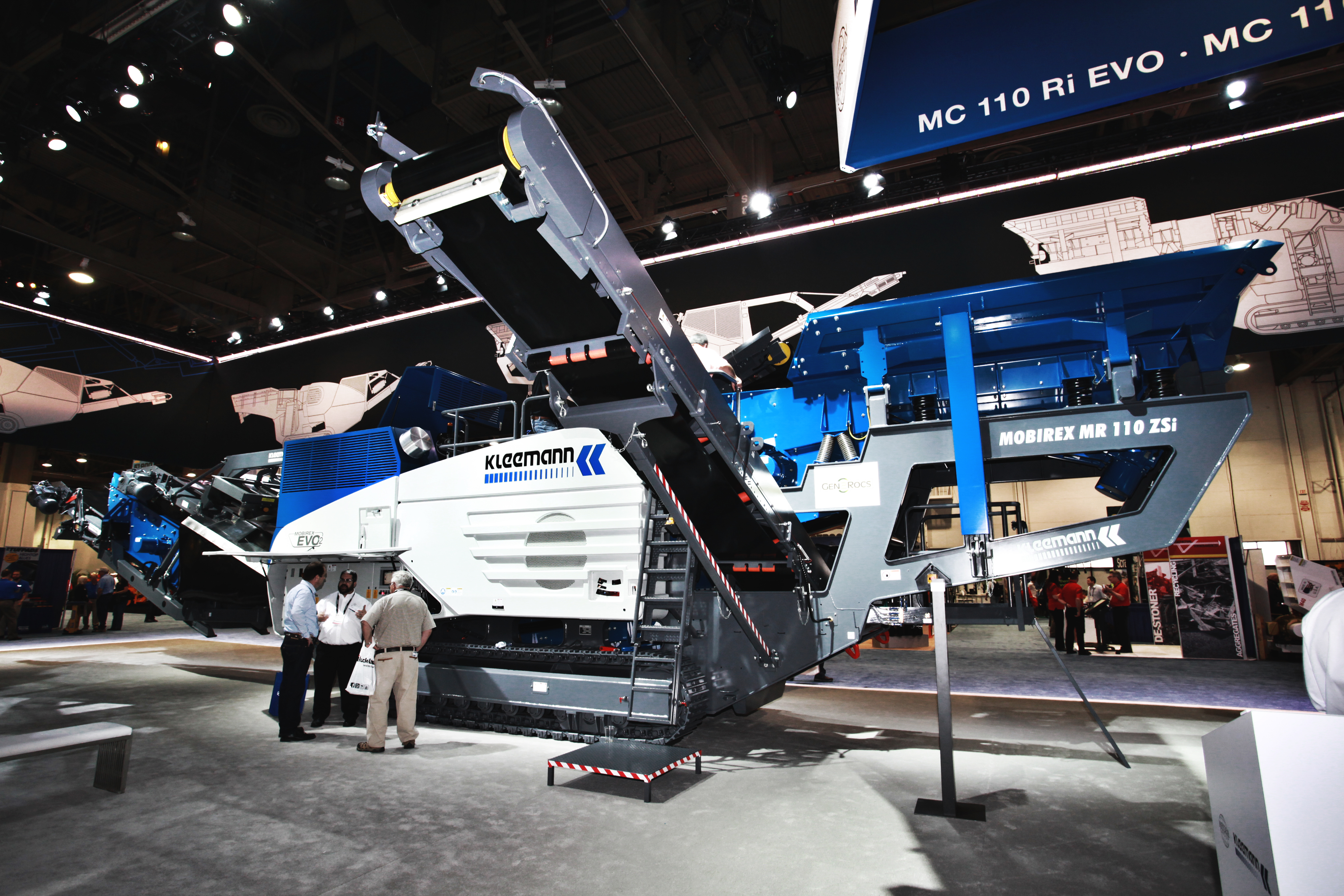
Kleemann has launched two new impact crushers, one being the MR 110 ZSi EVO2
“EVO 2 represents the continuing evolution of the successful EVO Contractor Line, with additional benefits in terms of economy and operational safety,” said Mark Hezinger, marketing manager.
The new impact crushers are differentiated by their size and productivity with the MR 110 ZSi EVO 2 having a crusher inlet opening of 1,100mm, and the MR 130 Zi EVO 2 a crusher inlet opening of 1,300mm. These provide feed capacities of up to 350 or 450tonnes/hour respectively.
The S indicates a Mobirex unit with optional, highly productive secondary vibrating screen with extra-large screening surface mounted on the discharge conveyor. This secondary screen unit can produce spec material, potentially eliminating the need for a separate screen.
The feeding unit has hydraulically folding hopper walls and locking system, which speeds set-up. A vibrating double-deck pre-screen between hopper and crusher eliminates fines from the product flow before they enter the crusher, reducing wear and cutting fuel costs.
Both units are Tier 4 Final-compliant, and they utilise direct drive crushers and electric drives for the vibrating conveyors, belts and the pre-screen, permitting high fuel efficiency and allows optimal loading of the crusher.
The crushers feature a new inlet geometry which allows even better penetration of the material into the range of the rotor.
A latest-generation diesel engine transmits its power almost loss-free directly to the flywheel of the crusher via a robust fluid coupling and V-belts, enabling enormous versatility as the rotor speed can be adjusted in four stages to suit different processing applications.
The Kleemann Continuous Feed System (CFS) manages a more equal loading of the crushing area, in which the conveying frequencies of the feeder trough and the pre-screen are adapted independently of each other to the level of the crusher, thus significantly boosting performance.
For the optional S version with secondary screen mounted, the oversize gradation return conveyor has been redesigned from the predecessor models, eliminating a vertical bend and integrating the transfer chute at the feed hopper.
%$Linker: