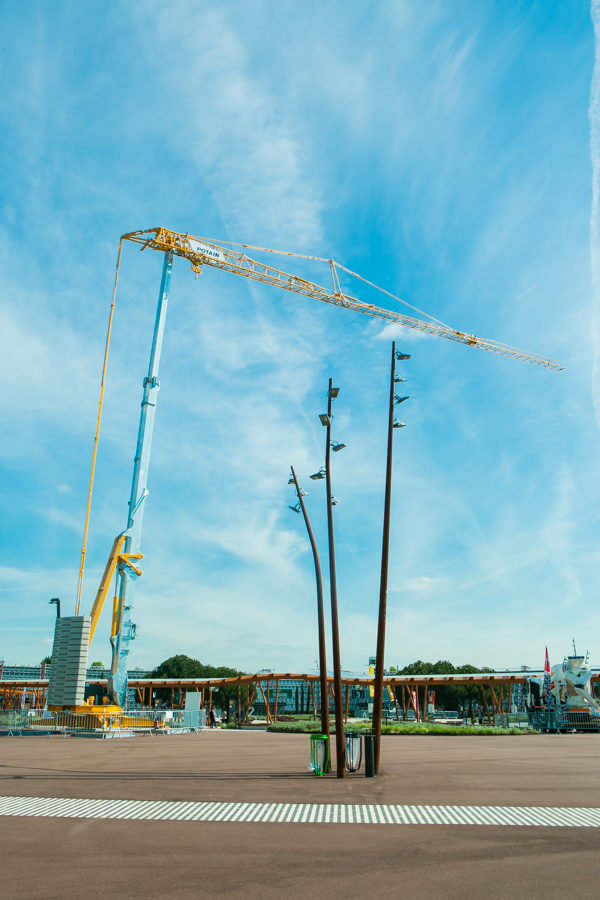
Manitowoc shed its food equipment arm, Manitowoc Foodservice, in March 2016 and the last two years have been ‘challenging’, according to executive vice president Aaron Ravenscroft. “It’s a difficult business,” he says. “It’s extremely capital intensive and cyclical, it’s high risk and high stress work and most of our customers are family-owned businesses who need a personal approach rather than a corporate one.”
The company is harnessing technology to communicate with users and minimise downtime. Jerome Chanel, vice president of services, said that the use of its remote diagnostics tool CraneSTAR Diag is ramping up after its launch five years ago, with his team responding to 500 communications every month.
“Our customer surveys tell us that we can troubleshoot one in two problems the first time thanks to the tool,” says Chanel. “That saves trouble and saves downtime.” In cases where an engineer must visit site, the diagnostic tool means that they can arrive equipped with the right parts. Manitowoc has also just launched a new smartphone app which helps operators translate error codes, depending on the crane and operating system.