BHS-Sonthofen’s new generation of type DKXK twin-shaft batch mixers feature a rubber trough specially designed for producing calcium silicate bricks.
Calcium silicate bricks are made of sand mixtures containing a high silicate, quicklime and water content, a highly abrasive material.
BHS has therefore specifically developed the DKXK type of mixer for producing lime mixtures as an alternative version to the proven DKX type of twin-shaft batch mixer. Instead of a steel trough with a lining made of wea
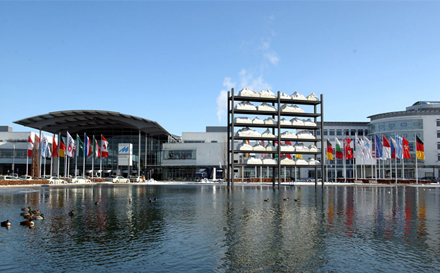
Calcium silicate bricks are made of sand mixtures containing a high silicate, quicklime and water content, a highly abrasive material.
BHS has therefore specifically developed the DKXK type of mixer for producing lime mixtures as an alternative version to the proven DKX type of twin-shaft batch mixer. Instead of a steel trough with a lining made of wear tiles, BHS builds its calcium silicate mixer with a rubber mixing trough that pulsates when mixing, thus effectively preventing sticky mixing material from caking.
This reduces blade and trough lining wear as well as reduces the engine's power consumption.
In the future, BHS-Sonthofen will offer the new mixer for the calcium-silicate brick industry with a filling volume ranging from 1,000-6,500litres.