A reinforced concrete bridge over the Autobahn 8 between Merklingen and Nellingen in southern Germany was demolished overnight due in no small part to the efficient, reliable performance of Atlas Copco hydraulic attachments.
In addition to demolition grippers, breakers and pulverisers, the demolition team used the HM 2000 hydraulic magnet to demolish structures and sort demolition waste. There is now nothing to stop the widening of the A8 to six lanes or construction of the parallel high-speed Wendlingen
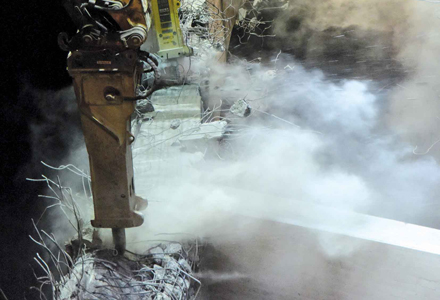
A reinforced concrete bridge over the Autobahn 8 between Merklingen and Nellingen in southern Germany was demolished overnight due in no small part to the efficient, reliable performance of 161 Atlas Copco hydraulic attachments.
In addition to demolition grippers, breakers and pulverisers, the demolition team used the HM 2000 hydraulic magnet to demolish structures and sort demolition waste. There is now nothing to stop the widening of the A8 to six lanes or construction of the parallel high-speed Wendlingen-to-Ulm railway link.
"A logistical masterpiece," is how Jörg Hamann, spokesman for Deutsche Bahn Projekt Stuttgart–Ulm, described the work. Demolition, including all ancillary tasks, was scheduled to be completed within just 14 hours and contractor Weilheim finished the task well within the given time.
They used eight178 caterpillar excavators with an operative weight of up to 50tonnes to remove the 1,500-tonne "Blaubeurer Weg" reinforced concrete bridge measuring 64m long and 6m wide. Several heavy-duty Atlas Copco grippers, breakers and concrete pulverisers weighing up to 4tonnes were used as attachments.
"Such structures would have been dynamited in the past," said Joachim Schmid, the demolition company’s chief executive. "Coming back to finish the task the next day was not an option here."
Tasks were completed in quick succession. As soon as roads were blocked off, workers disassembled the crash barriers and central reservations and then laid down non-woven fabric and gravel to protect the road surface. Next, the bridge railings were removed followed by the solid concrete sections and the entire superstructure.
Technical procedures for bridge demolition can be broadly similar every time, but each project has its own special characteristics, “a unique structure," said Schmid.
This particular overpass spanning the A8 did not feature a central support. As a result, excavators could not operate from above, the usual approach, but only from down below.
It was, therefore, all the more important that attachments could be applied exactly where they were needed using precisely the right amount of force.
It was not only the time-tested grippers and breakers which helped to dismantle the bridge successfully; an HM 2000 Hydro Magnet also gave an impressive performance. As a rigid magnet for carrier vehicles between 14-45tonnes, it is particularly suitable for separating scrap metal from other demolition waste. It ensures greater profit thanks to optimum use of scrap steel and also provides fast, highly effective sorting and efficient recycling. What's more, cleared construction sites mean significantly less damage is sustained by machines and equipment.
Now that the bridge is completely removed, the Deutsche Bahn project company has started construction of the A8 overpass with an overall length of around 87m and a height of up to 6.4m. Costing around €600,000, the replacement structure should be finished by January 2017.
In addition to demolition grippers, breakers and pulverisers, the demolition team used the HM 2000 hydraulic magnet to demolish structures and sort demolition waste. There is now nothing to stop the widening of the A8 to six lanes or construction of the parallel high-speed Wendlingen-to-Ulm railway link.
"A logistical masterpiece," is how Jörg Hamann, spokesman for Deutsche Bahn Projekt Stuttgart–Ulm, described the work. Demolition, including all ancillary tasks, was scheduled to be completed within just 14 hours and contractor Weilheim finished the task well within the given time.
They used eight
"Such structures would have been dynamited in the past," said Joachim Schmid, the demolition company’s chief executive. "Coming back to finish the task the next day was not an option here."
Tasks were completed in quick succession. As soon as roads were blocked off, workers disassembled the crash barriers and central reservations and then laid down non-woven fabric and gravel to protect the road surface. Next, the bridge railings were removed followed by the solid concrete sections and the entire superstructure.
Technical procedures for bridge demolition can be broadly similar every time, but each project has its own special characteristics, “a unique structure," said Schmid.
This particular overpass spanning the A8 did not feature a central support. As a result, excavators could not operate from above, the usual approach, but only from down below.
It was, therefore, all the more important that attachments could be applied exactly where they were needed using precisely the right amount of force.
It was not only the time-tested grippers and breakers which helped to dismantle the bridge successfully; an HM 2000 Hydro Magnet also gave an impressive performance. As a rigid magnet for carrier vehicles between 14-45tonnes, it is particularly suitable for separating scrap metal from other demolition waste. It ensures greater profit thanks to optimum use of scrap steel and also provides fast, highly effective sorting and efficient recycling. What's more, cleared construction sites mean significantly less damage is sustained by machines and equipment.
Now that the bridge is completely removed, the Deutsche Bahn project company has started construction of the A8 overpass with an overall length of around 87m and a height of up to 6.4m. Costing around €600,000, the replacement structure should be finished by January 2017.