Terex Washing Systems (TWS) is making final plans to unveil what it says is a new innovative washing system. The AggreSand system is the latest addition to what the company says is an already extensive product portfolio, and it is due to be officially launched in Quarter 2, 2013. The TWS AggreSand system combines aggregate washing and screening with sand processing on a modular chassis, and brings together “tried and trusted TWS components in an innovative modular design.”
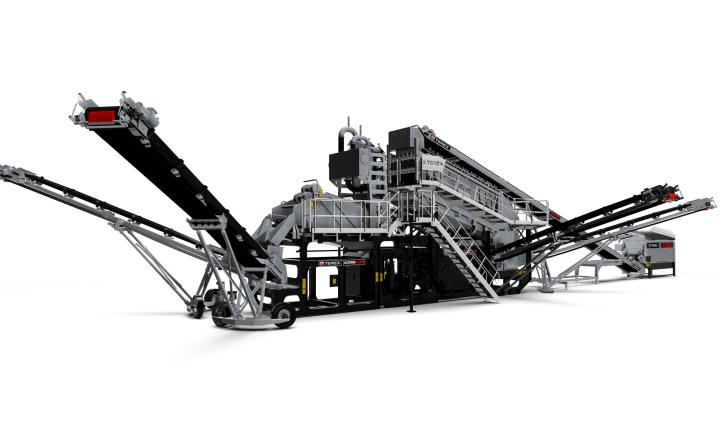
Terex Washing Systems is making final plans to unveil a new washing system
The AggreSand system is the latest addition to what the company says is an already extensive product portfolio, and it is due to be officially launched in Quarter 2, 2013.
The TWS AggreSand system combines aggregate washing and screening with sand processing on a modular chassis, and brings together “tried and trusted TWS components in an innovative modular design.”
TWS says that a gap in the market for such a washing evolution was identified following extensive research, part of which was conducted at the Terex Washing Systems first product development forums. This involved TWS engineers and sales technicians working with the global distributor network to formulate the concept.
TWS says that central to the development of the new plant was a modular design, pre-wired and pre-plumbed making it quick and easy to set up and easy to maintain.
According to TWS the plant also includes a range of other innovative features and designs.
“The AggreSand system will represent the epitome of washing in the marketplace and is a combination of significant enhancements and design changes to existing products as well as the introduction of new pioneering ideas,” says Sean Loughran, director of TWS.
“In our ongoing efforts to meet and exceed customer expectations, the AggreSand system will enable TWS customers to wash a wide range of materials at a high specification and produce up to five products.”
TWS designed a new modular hopper feeder with 12m3 capacity in keeping with ever increasing loading shovel sizes in today’s modern quarries and sand pits, and the H 12 is available with an automatic tipping grid and a 12ft two-deck vibrating grid complete with variable speed belt feeder, all controlled from the main operator interface and radio control unit.
TWS says the wide feed conveyor has a direct drive electric motor and gearbox arrangement and will work at a 19o angle when feeding the AggreSand system while the company opted for the 165R-3 (three-deck, two-bearing) rinsing screen, saying that its riveted construction reduces the stress associated with welded construction methods.
The 165R-3 gives 7.54m2 of screening area on all three decks.
“The large capacity split sump tank receives the rinsed fines from the bottom deck screen into either a course or fine compartment,” says TWS.
Two centrifugal slurry pumps (coarse an fine) are used to pump material from both sides of the sump tank into two hydrocyclones, which remove silts and clay (material below 63micron): these are sent to the water treatment plant.
The heavier material (above 63micron) exits the bottom of the hydrocyclones into a rubber lined box where blending can take place if required.
The underflow from the hydrocyclones transfers onto a dewatering screen via a discharge box which equally distributes the material across the screen to increase the dewatering screen area. Both materials are dewatered over a 500micron polyurethane screen to produce two instantly saleable grades of sand.
“The AggreSand system has the option of five conveyors: three aggregate and two sand. The 650mm wide conveyors are powered by direct drive electric motors and gearbox arrangements. The 9.3m long conveyors are angled at optimum height for excellent production,” says TWS.
The two conveyors have an automated radial wheel drive system that increases stockpiling capacity to 350m3.
“The 4m stockpile height of these conveyors make them ideal for producing generous stockpiles or feeding other equipment within the Terex product range,” says TWS, which points out that maintenance and access, “of critical importance during the design process of the AggreSand system,” has been achieved through a number of advanced features.
The system is operated via “an advanced and cutting edge user-friendly control system” utilising PLC technology already field proven on Terex crushing and screening plants.
“All components are designed so they can be easily dismantled and placed into standard 40ft containers, limiting the reassembly time on site with fewer crane lifts required,” adds TWS.
%$Linker: