BHS-Sonthofen is demonstrating its rotor centrifugal crushers of the RSMX series for processing hard and medium-hard rock to produce aggregate chippings and high-quality aggregates. The company says the rock-on-rock principle and the patented rotor with just two centrifugal chambers offer advantages over multi-chamber rotors, and these include the maximum input grain sizes of up to about 80mm for hard rock and up to 150mm for soft rock; optimal material flow in the rotor, free from clogging; 15-20% greater
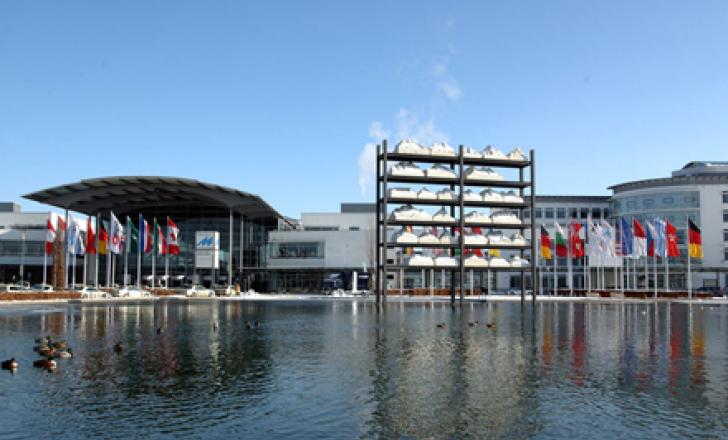
The company says the rock-on-rock principle and the patented rotor with just two centrifugal chambers offer advantages over multi-chamber rotors, and these include the maximum input grain sizes of up to about 80mm for hard rock and up to 150mm for soft rock; optimal material flow in the rotor, free from clogging; 15-20% greater throughput rate with the same power consumption; wear-related costs reduced by up to 25% and exhaust air quantity reduced by more than 10%.
BHS offers machines in four different sizes for throughput rates of up to 400tonnes/hour.
BHS says its rotor centrifugal crushers adopt the impact crushing principle where material is fed vertically from above onto the high-speed rotor, which is mounted on a shaft with vertical bearings. In both chambers of the rotor, the input material is rapidly accelerated outwards due to the high circumferential speed, routed out via a naturally forming material bed and hurled at high speed against a fixed annular wall, generally consisting of an anvil ring made of heavy-duty casting or an autogenous material bed.
Stand: B2.325/420
%$Linker: