A United Arab Emirates quarry is putting its Volvo fleet to the test in harsh conditions
A quarrying facility in the United Arab Emirates (UAE), is boosting output following the commissioning of a new machine fleet for loading and hauling duties. The quarry is located in the northeast of the UAE in Fujairah, an emirate almost entirely surrounded by mountains. This rugged landscape is the product of an estimated 800 million years of geological activity and is the source of a high quality limestone used in
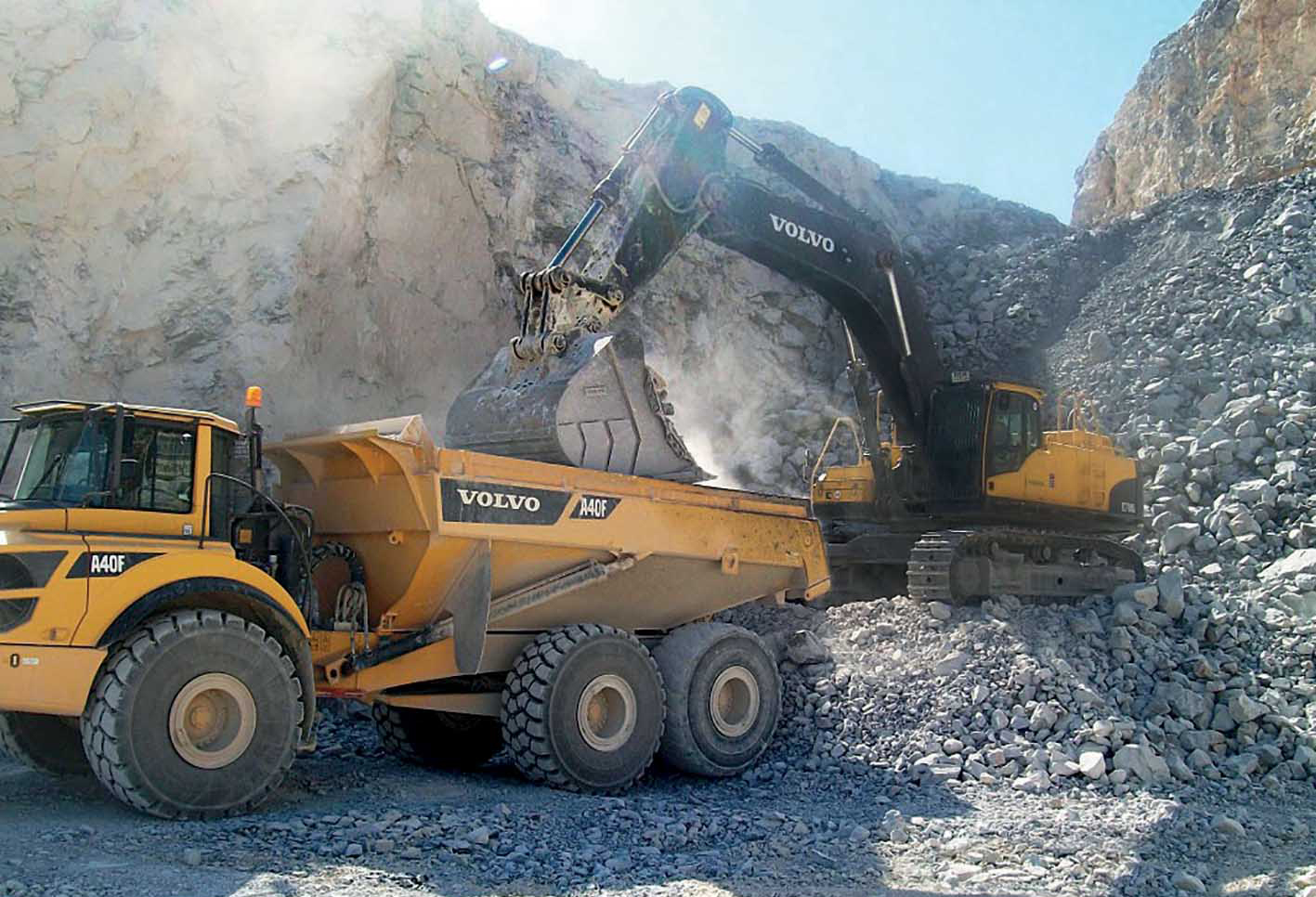
Excavators and haulers from Volvo CE are assisting production at a quarry in the UAE
A United Arab Emirates quarry is putting its Volvo fleet to the test in harsh conditions
A quarrying facility in the United Arab Emirates (UAE), is boosting output following the commissioning of a new machine fleet for loading and hauling duties. The quarry is located in the northeast of the UAE in Fujairah, an emirate almost entirely surrounded by mountains. This rugged landscape is the product of an estimated 800 million years of geological activity and is the source of a high quality limestone used in construction in the region.
Bin Lahej Crushers is one of the UAE’s leading quarrying specialists and is producing high quality aggregate from this facility, which is being used for a variety of major construction projects. Located in Ras Al Khaimah, close to Fujairah, the company is now running a fleet of Volvo articulated haulers, excavators and wheeled loaders to produce 850tonnes/hour of crushed limestone, with the facility running 20 hours/day and six days/week. Because of the high output requirements and the arduous environment, the reliability and durability of the fleet is of key importance with regard to maximising production and minimising unscheduled downtime.
The quarry firm is using two EC700C-Series excavators, three A40F-Series articulated haulers and two L150G-series wheeled loaders. The company ordered its first Volvo machine one year ago and the success of this unit in the application prompted the firm to purchase the rest of the equipment fleet from the same supplier.
Productivity is key to profitability at this site and the limestone is first drilled and blasted by a subcontractor in a nearby quarry. The Volvo EC700C excavators are then used to load the extracted material onto the A40F haulers, which transport the rock 400m to the crusher. The limestone first passes through a primary jaw crusher before going on to be further broken up by a secondary impactor. The Volvo machines work two 10-hour shifts, during which each hauler can make up to 50 trips between the rock face and the crusher.
Once crushed and screened to the necessary fractions, the finished product is then transported to a variety of locations throughout the region. The crushed material is used mainly as aggregate and Bin Lahej is a supplier to Middle Eastern companies such as Unimix. Aggregate from this facility has been provided to contractors working on projects as large as the Burj Khalifa in Dubai, the tallest man-made structure in the world.
Bin Lahej Crushers says that it has a strong demand for its products and as such, the machines need to be able to consistently produce large quantities of material every day. The firm’s ISO rating means that it is also responsible for producing a reliable quality of aggregate also, with the crushing and screening facility playing an important role.
Bin Lahej works closely with local359 Volvo CE dealer FAMCO, which is providing on-site training and assistance to ensure that each operator is able to derive optimum performance from the machines while also reducing fuel consumption and overall wear and tear.
The intensive nature of operations at the site, and the influence the operator has on efficiency, means that this is a very important aspect of working with Bin Lahej. Meanwhile the customer also says that the Volvo CE CareTrack is playing an important role in improving performance on site, as the telematics system allows the company to assess and adjust operator and machine behaviour to help maximise efficiency throughout the working day.
A quarrying facility in the United Arab Emirates (UAE), is boosting output following the commissioning of a new machine fleet for loading and hauling duties. The quarry is located in the northeast of the UAE in Fujairah, an emirate almost entirely surrounded by mountains. This rugged landscape is the product of an estimated 800 million years of geological activity and is the source of a high quality limestone used in construction in the region.
Bin Lahej Crushers is one of the UAE’s leading quarrying specialists and is producing high quality aggregate from this facility, which is being used for a variety of major construction projects. Located in Ras Al Khaimah, close to Fujairah, the company is now running a fleet of Volvo articulated haulers, excavators and wheeled loaders to produce 850tonnes/hour of crushed limestone, with the facility running 20 hours/day and six days/week. Because of the high output requirements and the arduous environment, the reliability and durability of the fleet is of key importance with regard to maximising production and minimising unscheduled downtime.
The quarry firm is using two EC700C-Series excavators, three A40F-Series articulated haulers and two L150G-series wheeled loaders. The company ordered its first Volvo machine one year ago and the success of this unit in the application prompted the firm to purchase the rest of the equipment fleet from the same supplier.
Productivity is key to profitability at this site and the limestone is first drilled and blasted by a subcontractor in a nearby quarry. The Volvo EC700C excavators are then used to load the extracted material onto the A40F haulers, which transport the rock 400m to the crusher. The limestone first passes through a primary jaw crusher before going on to be further broken up by a secondary impactor. The Volvo machines work two 10-hour shifts, during which each hauler can make up to 50 trips between the rock face and the crusher.
Once crushed and screened to the necessary fractions, the finished product is then transported to a variety of locations throughout the region. The crushed material is used mainly as aggregate and Bin Lahej is a supplier to Middle Eastern companies such as Unimix. Aggregate from this facility has been provided to contractors working on projects as large as the Burj Khalifa in Dubai, the tallest man-made structure in the world.
Bin Lahej Crushers says that it has a strong demand for its products and as such, the machines need to be able to consistently produce large quantities of material every day. The firm’s ISO rating means that it is also responsible for producing a reliable quality of aggregate also, with the crushing and screening facility playing an important role.
Bin Lahej works closely with local
The intensive nature of operations at the site, and the influence the operator has on efficiency, means that this is a very important aspect of working with Bin Lahej. Meanwhile the customer also says that the Volvo CE CareTrack is playing an important role in improving performance on site, as the telematics system allows the company to assess and adjust operator and machine behaviour to help maximise efficiency throughout the working day.