With capital expenditure plans being reduced, many quarry operators are using the funds available to improve on productivity with their existing equipment fleets. Claire Symes reports. The economic downturn has had a big impact on the aggregates production sector with many quarry operators looking to reduce costs and rationalise operations. The impact of this can be seen in the reduction of capital expenditure plans but the investments that are being made are focused on efficiency.
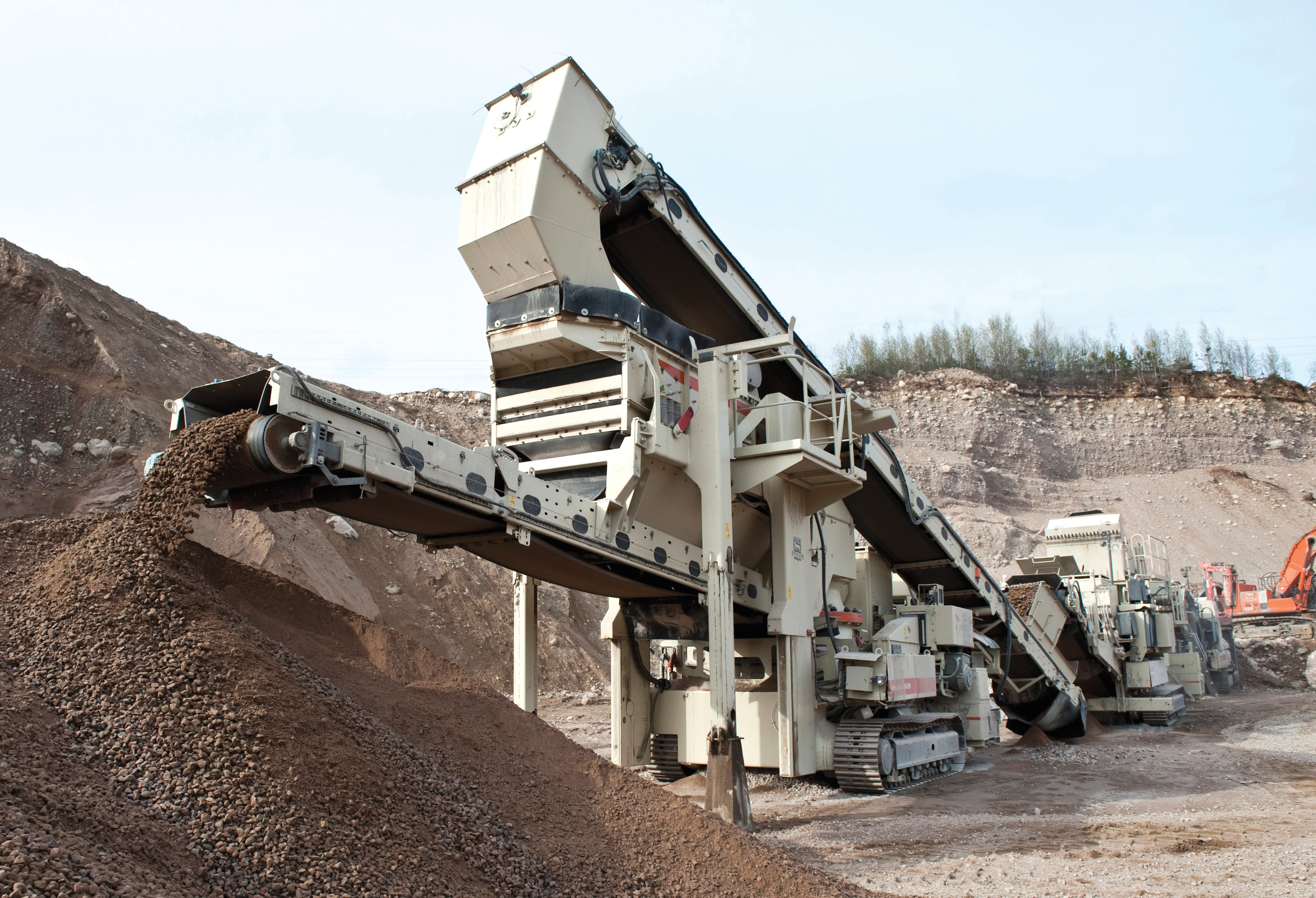
Many aggregates producers are focusing investment on improving existing equipment
With capital expenditure plans being reduced, many quarry operators are using the funds available to improve on productivity with their existing equipment fleets. Claire Symes reports
The economic downturn has had a big impact on the aggregates production sector with many quarry operators looking to reduce costs and rationalise operations. The impact of this can be seen in the reduction of capital expenditure plans but the investments that are being made are focused on efficiency.When it comes to crushing and screening equipment, the method of choice for enhancing productivity appears to be use of optimisation software. "Over the years we have seen an increase in demand for optimisation," said
"Dealers are also investing in
Version 3.3 of Bruno was released this year and is based around the cost per tonnes for 1000hours of operation. According to Pursio, it is deal for planning new plant, whether a fixed or mobile system.
"The system concentrates on operating costs - power draw, maintenance, parts," he said. "Some Finnish companies have taken Bruno as the official tool for design and these engineers have certain equipment that they have to work with. Recent optimisation of mobile plant for a Finnish customer helped to deliver 20% more production just by adjusting settings." In new quarries, operators are using software to optimise the operation to achieve targets and then benchmark the operation and track production.
Svensson believes that optimisation is important to quarries looking to improve production. "A typical example of the results possible is shown in a basalt quarry we carried out the process for in Germany," he said. "The product quality in the asphalt fractions did not meet the tight specifications but at the same time there was too little of the 11/16 fraction as well as the need to avoid excess dust and sand production.
"The obvious solution would have been to put in an extra crushing stage, however, this is a costly exercise so we made an attempt to fine tune the existing plant. By intensive simulations we found that with low cost changes to the existing equipment, that it was possible to meet the demands. Together with the customer, we implemented the changes and also trained the personnel to operate the equipment in a new way. The end result was good - the quality demands were met and increased production of the very much needed 11/16 product."
Teller believes that before global recession quarry operators were working flat out and not looking at their production so closely, now they are working more intelligently. "This trend is likely to continue," he said. "Bedrock is working with a number of universities so that the next generation of engineers has a clear understanding of the benefits of optimisation. With computerisation, people are more familiar with the internet and PCs so there is a new generation engineers who are more savvy." In the meantime, current research and development means that further innovations in optimisation software will soon be available and add more functionality.
Contractor capability
Today's largest mobile crushing and screening equipment can offer capacities to rival that of conventional static installations and has driven a step-change in quarry production. But as these larger mobile machines reach the size of being 'less mobile' development is shifting to improving efficiency of tracked and wheeled crushers and screeners."There has been a slight move towards smaller machines, which may be a reflection of the investment level that is available and customers making the most of the funds they do have," said Sandvik Mobile Crushing and Screening global product line manager John Nethery. "The trend towards larger and larger mobile crushing and screening equipment that we have seen in recent years was driven by demand from contractors but the recession has reduced this driver.
"However, once machines reach a certain size they stop being mobile in the true sense. Development now is likely to focus on improving efficiencies rather than increasing production capacities." According to Nethery, other developments in the next year or two are likely to offer further efficiency improvements. "More interlinking of controls between screens and crushers will improve the function and productivity," he said. "Screening development has already gone a long way and I think there will be more focus on crushing improvements."
Fuel focus
Fuel costs can make up a significant proportion of a quarry operator's running costs, which is why many have invested in modern, fuel efficient equipment. However, while the latest designs improve fuel economy, it is still the way the machine is driven and used that can have the biggest impact on fuel efficiency."Driving down costs and improving fuel burn can aid operators during a recession," explained Finning strategic account manager Rob Powell. "Machine design can only influence efficiency by a small percentage but operators have a much greater chance to influence it." Finning started running the one day courses in 2008 and so far 700 people have undergone the training but it is not just limited to operators. "The course is also aimed at supervisors and executives in the industry, so they can understand the potential benefits from optimising their operations," said Powell.
Steve Platt, who is also a strategic account manager with Finning, added, "It has been clear over the last 12 months of running the course that there is no single way of improving efficiency but it comes through a combination of factors.
"Some companies are spending £20million (€22.2million) on fuel each year so a 5 to 10% saving is significant." One of first ways delegates are trained to think about their actions is through considering idling on a wheeled loader. "A typical wheeled loader will burn 4.2litres per hour at idle and will be left at idle for an hour a day," explained Platt. "Over a 24 day working month, that adds up to 1209litres per year.
"At £0.41 (€0.45) per litre for fuel that costs £496 (€550) per year, and at £0.65 (€0.72) per litre, that's £786 (€872) per year. But very few quarry operators have just one wheeled loader - with a fleet of 30, the costs add up to between £14,800 and £23,580 (€16,427 and 26,176) a year in idling fuel costs." By putting figures to the actions, Finning is aiming to help the operators understand how their actions can influence the operation. Switching the engine off is not always the best option if the next task is less than 10 minutes away but trains operators to think about the options.
The course also considers changing gear at lower revs, dumping at lower engine speeds, use of the correct ground engaging tools (GET) as well as the benefit of new technologies such as product link, load sensing hydraulics, ride control and power shift.
According to Platt, using 20% lower revs during the dumping cycle can reduce fuel burn by up to 45%, while using the right GET can not only improve service life but also reduce fuel burn.
"One of our China Clay customers was using the old J Series GET, from which they achieved 250hours working life and a fuel economy of 80.5litres per hour. After switching to the improved K Series, they managed a service life of 360hours and a fuel economy of 75.7litres per hour," said Platt.
During the course, operators are also taught about the most fuel efficient loading and dumping techniques and the impact of haul road condition and tyre and track maintenance on economy. Nonetheless, operators need to balance economy with productivity and consider fuel burn per tonne moved when demand is high, but when demand is lower the focus should shift to economy.
According to Cat, other dealers in its European network can also offer the Eco-Drive training in the same way as Finning does at its facility in Leicester or at the customers' site. "The quarry operators may own the equipment, but it is the operators that drive it and most can benefit from objectively reviewing their skills," said Powell.