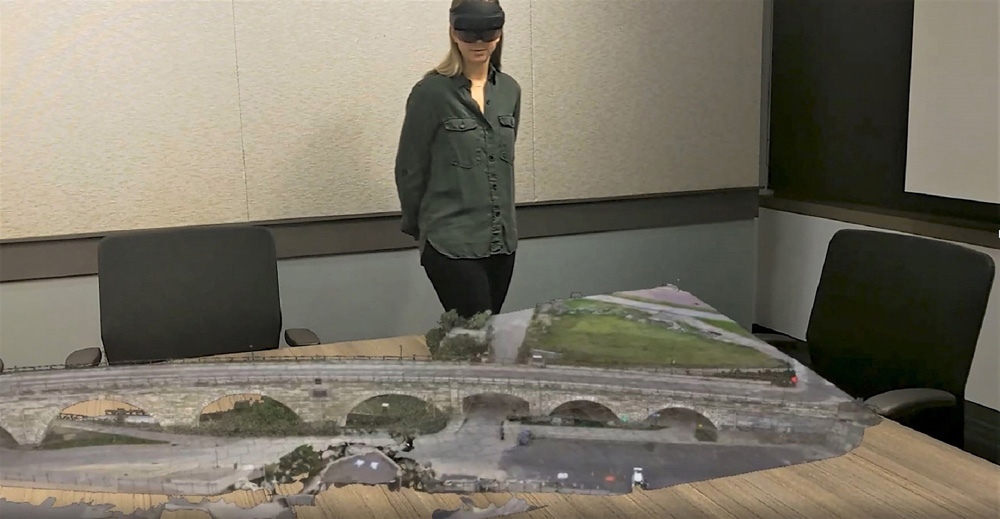
Recent high profile bridge failures—including the Morandi Bridge collapse in Genoa Italy, the Nanfang'ao Bridge collapse in China, and the Mexico City Metro overpass collapse—highlight the risk and danger to the community and the high costs associated with delayed or deferred maintenance on bridges.
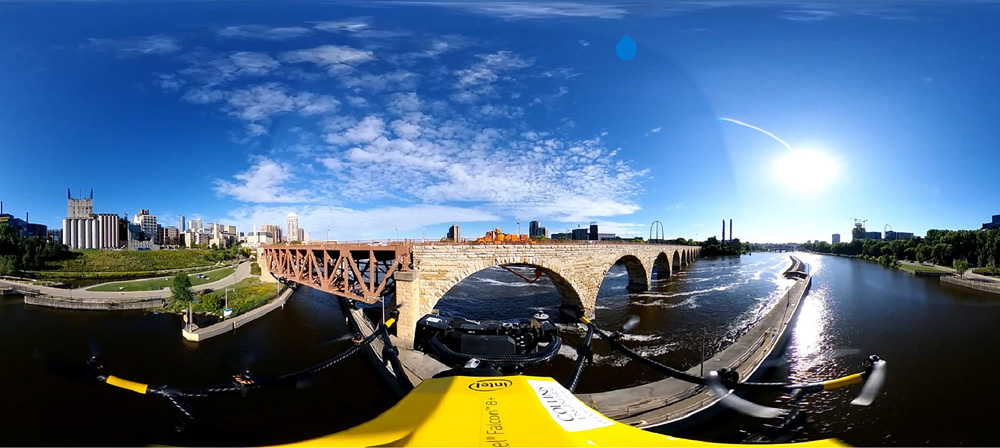
Photo Credit: Collins Engineers
In the U.S., the American Society of Civil Engineers (ASCE) 2021 Report Card on America’s infrastructure shows that while we recognise the need to repair ageing and inferior infrastructure, we are still lagging in the investment needed to address the issue with a repair backlog estimated to be USD 125 billion. America’s bridges scored a C grade, with the report noting that out of the 617,000 bridges across the country, 42% were over 50 years old and 7.5% are structurally deficient or in poor condition.
Traditional visual inspections that take place on site are labour intensive, can require expensive equipment, often require lane closures that create inconvenience for travellers, may present safety risks, and can be inaccurate and error prone.
National bridge inspection standards in the US and other countries around the world require additional data inputs and adds another layer of complexity. And in today’s COVID-19 environment, maintaining social distancing and ensuring safety for employees and the public can present additional challenges.
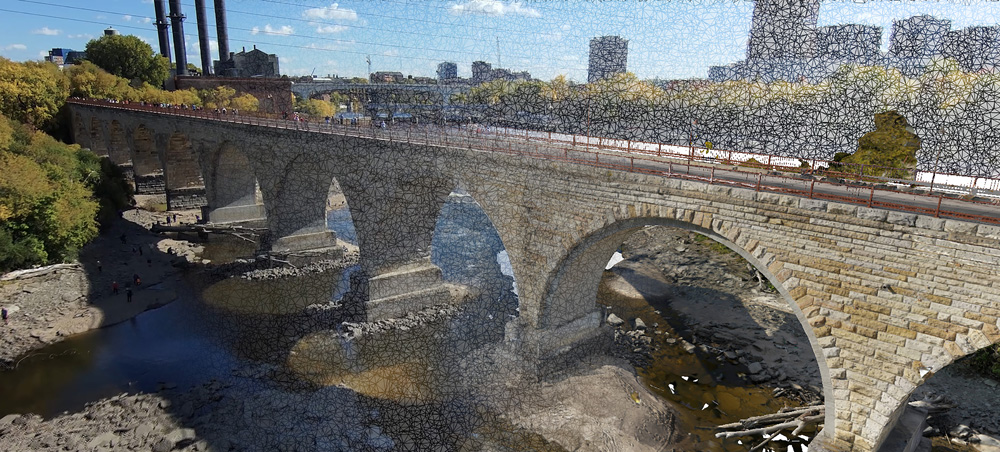
Photo Credit: Bentley Systems
Some of Bentley’s most innovative users are reimagining inspections through the lens of digital twins. A digital twin is a digital representation of a physical asset, process, or system, as well as the engineering information that allows us to understand and model its performance. A digital twin can combine data from continuous surveys, photogrammetry, LiDAR, and sensors, as well as track changes to assets on a timeline, enabling owners to view the digital representation of the infrastructure asset and related real-world conditions over time.
As departments of transportation and road agencies are being pressed to show the most effective use of their limited funding, taking advantage of digital twins can provide for safer, less expensive, and more timely and accurate inspections. Digital twins allow owners to track historical changes and understand information—such as the exact size of cracking, corrosion, or section loss—rather than trying to determine this information by looking at pictures taken over time.
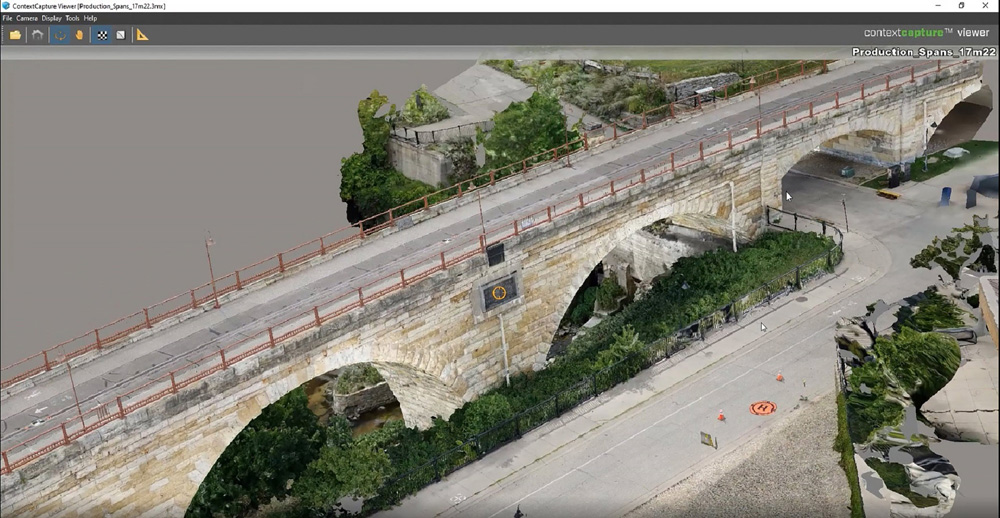
Photo Credit: Bentley Systems
Transportation agencies, such as Minnesota DOT, have used unmanned aerial vehicles (UAVs) to assist with their inspections and achieve savings of as much as 40% with these methods. Because bridges have such a long lifecycle, often up to 75 - 100 years, it is important to track change to the structures over time. These agencies have found that by deploying UAVs and having a digital twin, they were able to see the change over time and have a holistic view of the bridge, including seeing past inspections laid on top of the current data, which can improve efficiency and help predict the future.
There is great opportunity for agencies to use UAVs to complement and augment standard and in-field inspections. The data from these inspections can be reviewed quickly and easily from anywhere, whether in the office or a remote location. When engineers review time-lapse comparisons of detailed changes, they can annotate specific areas of concern and designate anything that needs to be specifically reviewed in the field. Field crews can see all the inspector notes right on the structure, which is more visual, more accurate, and more efficient.
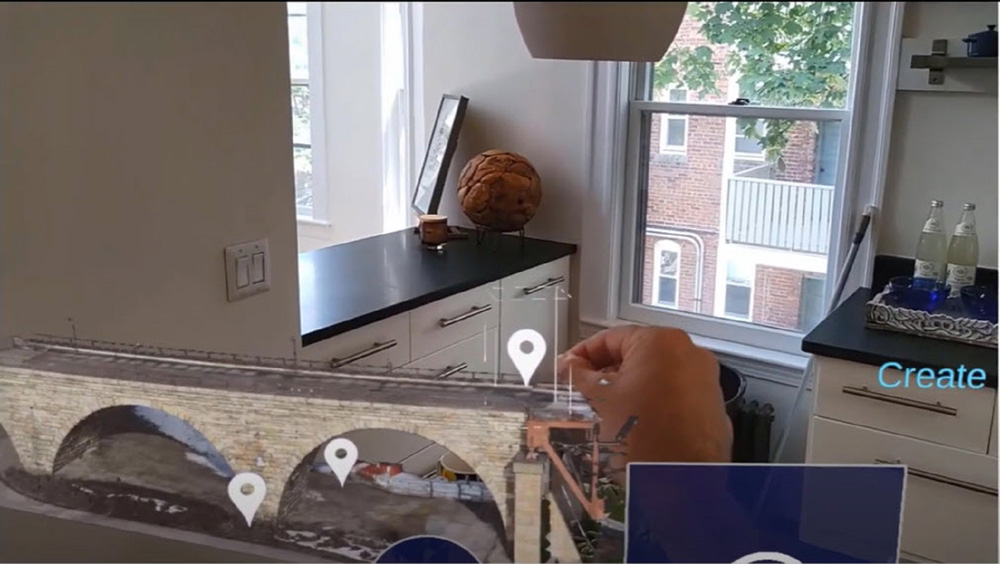
Photo Credit: Bentley Systems
Taking advantage of digital twins allows bridge inspectors to immerse themselves in the model of a bridge structure without being physically on site. Inspectors can conduct inspections using the digital twin of the asset, along with immersive inspection capabilities in Microsoft HoloLens. They can conduct significant parts of the inspection while in the office, reducing the time required in the field, which makes the overall inspection quicker, more efficient, safer, and less costly. A digital twin provides flexibility, as engineers can conduct more in-depth inspections without having to schedule expensive equipment and labour for that purpose. Applying digital twins over many large, complex, or signature bridges can lead to significant savings, while increasing safety and providing richer visualisation is the ultimate goal.
One of the biggest advancements is the reality mesh, the visualisation for a digital twin that gives yet another dimension to understanding of the infrastructure and surrounding topography. A reality mesh is a 3D model of real-world conditions that contains large amounts of triangles and image data. Each digital component can be automatically recognised and/or geospatially referenced, providing users with an intuitive and immersive way to navigate, find, view, and query their asset information.
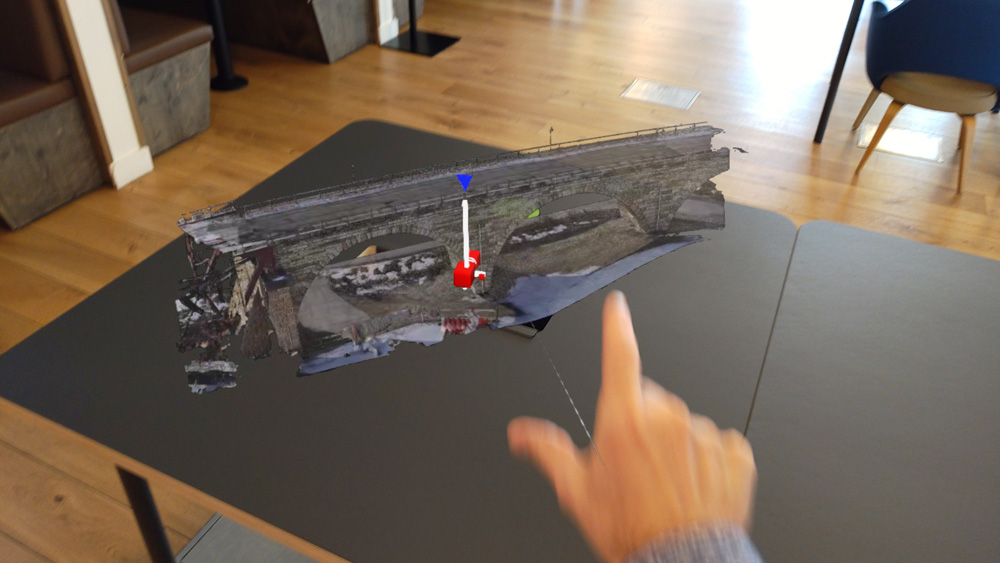
Photo Credit: Bentley Systems
Reality meshes can be used in many engineering, maintenance, or GIS workflows to provide precise real-world digital context for design, construction, and operations decisions. The photos, videos, and data captured by UAVs can be used to produce a high-resolution reality mesh of a bridge. When this reality mesh is combined with other relevant data, it provides a great digital twin representation. And using reality meshes for inspections can significantly decrease the amount of time inspectors have to be on and around structures in the field.
Utilising digital twins and technology—including UAVs—to collect, process, store, and analyse large amounts of data can reduce costs and increase quality of inspections. The immersive inspection capabilities in Microsoft HoloLens can reduce the time required in the field, while making inspections more efficient, safer, and less costly. The technology can improve safety for inspectors and the public at large and help preserve bridge infrastructure into the future.
Meg Davis is Bentley Systems’ Industry Marketing Director, Roads and Bridges. She can be reached at [email protected].
Sponsored content produced in association with Bentley Systems