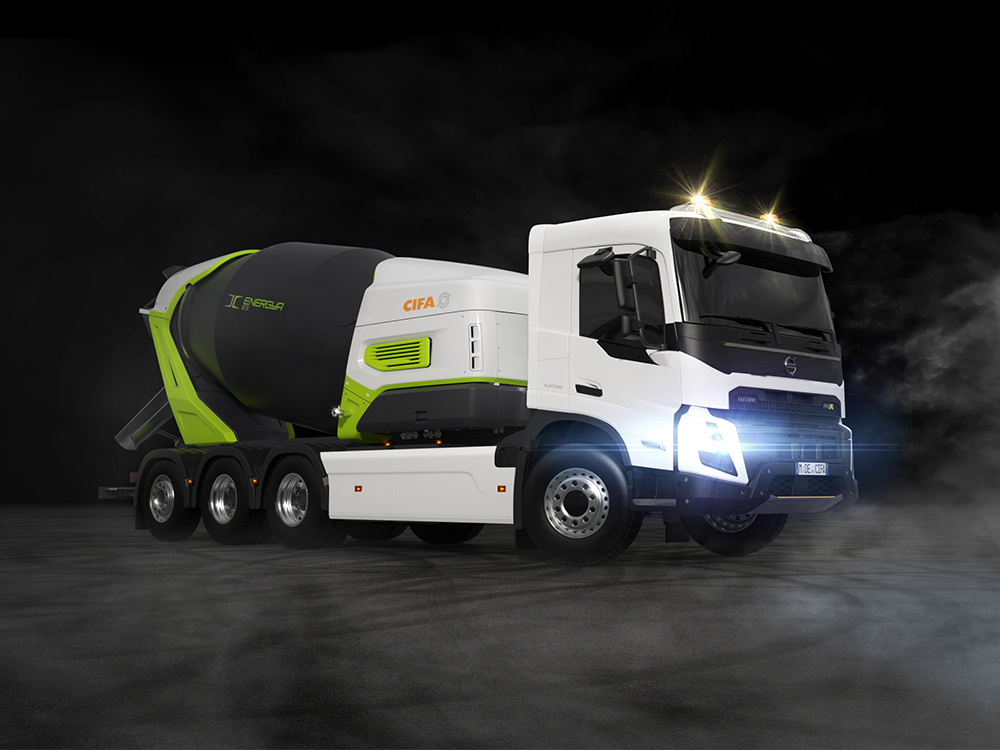
How does the E9 full-electric mixer work?
The E9 mixer is based on a drum drive system that combines the advantages of using the truck's energy with that of the mixer's lithium battery. In traditional cement mixers the movement of the drum is generated by a hydraulic system; in Energya truck mixers, on the other hand, it is generated by an electric induction motor that receives energy from a lithium ion battery, present on the same kit. These batteries store sufficient power for an entire working day. In the extreme case that the batteries of the mixer run out, it can draw power from the power take-off of the electric truck itself, recharging the battery in about an hour.
The E9 system is compatible with both 220 V and 380 V outlets. Charging times vary from 8 hours with a standard system and are reduced by up to one hour if the column designed by CIFA is used. In case of public recharging columns, the time varies according to the available power. The truck, on the other hand, is a Volvo FMX with 330kW of continuous power, 4 tridem axles, and 4 batteries of 360 kWh, rechargeable in 10 hours with AC and 2 hours with DC. The range on the road is about 200 km. On a typical working day, during which the vehicle travels between 120 and 200 km, approximately 30 kWh are required to run the mixer itself. The E9 system, thanks to its batteries, avoids consuming energy to move the drum and the autonomy of the chassis remains the same.
The E9 mixer has an advanced control and management system. In fact, all the information relating to the state of use and operation of the mixer can be checked at all times on the monitor installed in the driving cab of the truck. It is therefore possible to check all parameters and activate or manage the various functions while keeping an eye on the charge level of the battery. There is an identical monitor at the back of the vehicle where there is also an analogue control pad.
Davide Cipolla, CEO of CIFA: "The Energya brand has been a revolution for the sector ever since its launch in 2013, presaging such current concerns as the importance of electrification for sustainability, automation and connectivity. Indeed, these have become prerogatives for all CIFA machines – by using the digitisation of management systems and remote monitoring. We are proud to have been pioneers in a traditional sector such as the concrete industry, which is becoming aware of the need to change and adapt in an evolving global situation. "The concrete sector has three approaches to achieve the objectives of the 2030 Agenda: the introduction of low-impact materials and processes, durability of the equipment and the reduction of CO2 emissions on the construction site. We have worked and will continue to work on reducing emissions of the Energya series, but we also want to go one step further and focus on durability and safety. We know very well that we are one of many nodes in a global network, that of the construction industry, extended in space and time. Not only the construction of products, but all actions have a lasting impact on the environment and on people, and we are responsible for the use of every resource throughout the supply chain all the way to the construction site where our work comes to fruition. That is why we are also implementing sustainable projects for all our corporate activities, from the factory to the offices."
Marco Polastri, Sales Aftersales & Marketing Director: "Energya has become a brand with a business unit in its own right, formed of a team of specialists committed to its development, including in terms of sustainability, both at the level of the product and in terms of economic solutions for customers (for example, by devising local ways that can help with conversion of the fleet), providing a real consultancy service for those who share our green vision."
Click here to find out more
Content produced in association with CIFA