Egis has an innovative approach to addressing construction defects - *Martin O’Flaherty, Jean Pohu. Defects often become apparent after construction projects are handed over to the client and this is a common problem across most highway projects. The problem is shared by highway operators who have assumed the responsibility of managing such projects.
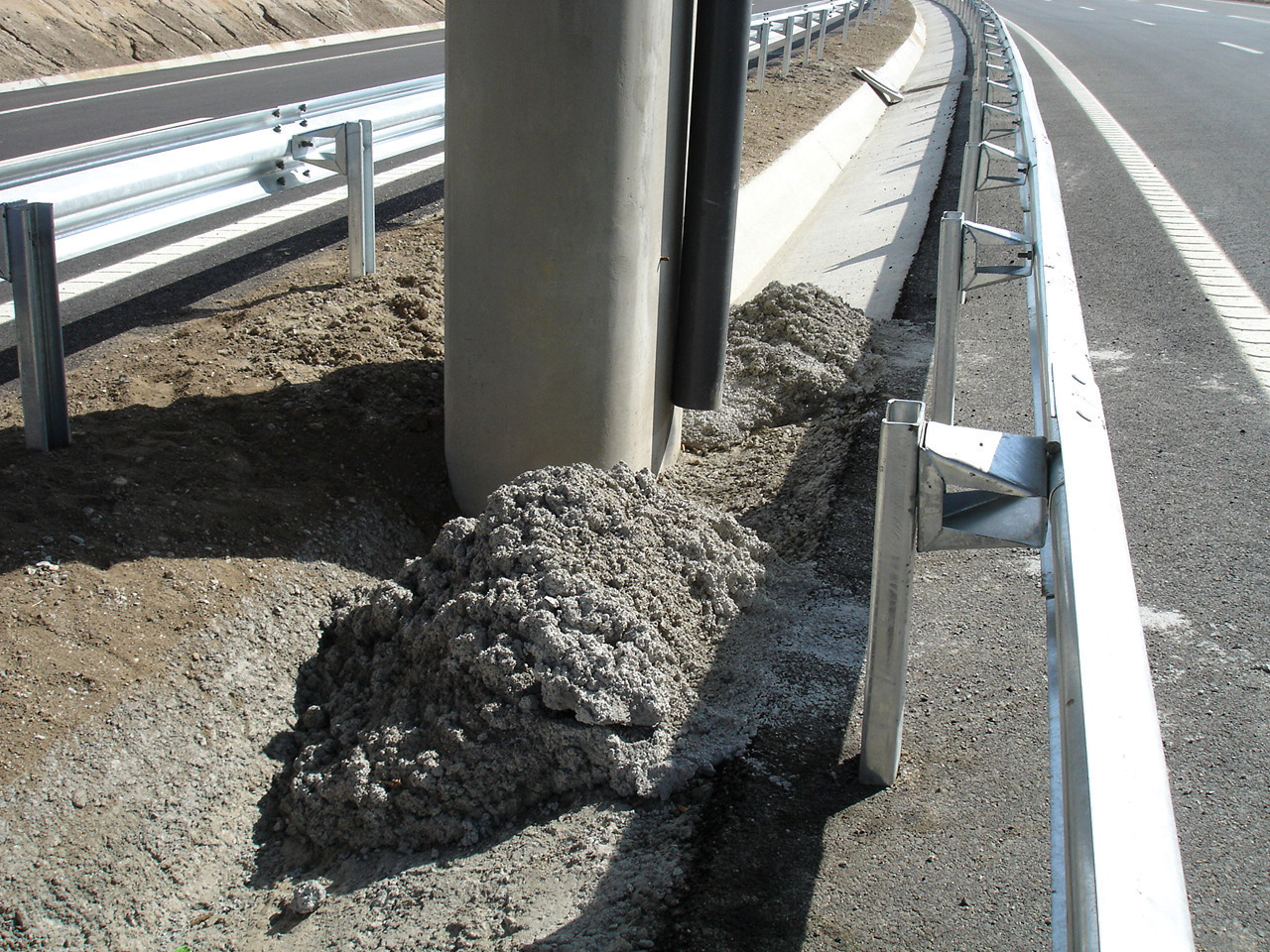
Drainage Channels are often blocked by barrier posts or light poles
Egis has an innovative approach to addressing construction defects - *Martin O’Flaherty, Jean Pohu
Defects often become apparent after construction projects are handed over to the client and this is a common problem across most highway projects. The problem is shared by highway operators who have assumed the responsibility of managing such projects.The biggest risk is that operators may face the cost of repairs or other faults directly caused by the existence of these defects. Over time this risk greatly increases as establishing and proving accountability may be difficult.
Experience suggests that it is only after handover that operators can tackle construction defects and minimise the financial exposure. However, it is worth bearing mind that earlier involvement in projects could also assist in resolving these defects. There are key points that operators should impose to ensure that the process is effective and there are varying degrees of influence that can be achieved during each stage. Using this approach can leave the operator in a strong position and it is important to consider the preparation of contracts, the handover date and the time after the handover.
The obligations of a contractor for a standard design build and operate contract are reduced after the handover date. The contractor’s role is then limited to addressing minor snags and transferring files and other documentation. The majority of these types of contracts between the concessionaire and the contractor are prepared and implemented based on these assumptions with measures included to address any construction defects.
Past experience shows that this does not occur in most cases. It is common for the contractor to have a considerable amount of outstanding works to complete after the project has been handed over to the operator. Both parties then have to work in parallel, which may not have been envisaged in the original contract and can result in conflicts. It may be further compounded by the absence of any direct contractual relationship between the contractor and operator.
To avoid such problems it is best for an interface agreement to be put in place between the concessionaire, contractor and the operator to cover the post-handover period. This agreement should set out a framework for the contractor to carry out necessary final works within the confines of the operator’s responsibilities.
An interface agreement should include several key points including an agreed procedure on how the operator alerts the concessionaire or the contractor to any defects. The procedure should set a policy on recording defects and who should maintain this register, a responsibility that should normally be handled by the concessionaire as the owner of the infrastructure and who authorises payments.
Once construction defects are identified they should be classified so as to meet the operator’s obligations. Deadlines for repairing construction defects should also be imposed on the contractor, providing consistency for the client or relevant government agency, as well as setting a final completion date for the works. It would also be advisable to transfer outstanding construction snag items onto the construction defect list and incorporate them into the process.
Some construction defects may have to be included in the operator’s documentation although this would require a waiver on behalf of the operator, removing its obligation to complete the repairs. This would also provide a log of defects for reporting to the client or government agency. An agreement of any advanced notices and documentation is required by the operator before the contractor can commence repair work on the project. An agreed time frame should be set out by the operator to allow the contractor access to the project to carry out the repair works.
The system should define any health and safety obligations for the corrective work and include clarifying who is responsible to implement legislation and who holds liability for any accidents, as well as identifying whose insurance is in force during the repair work.
The agreement should identify who is responsible for traffic management required for the necessary repair work, as well as who is responsible for approving the traffic management measures. It should highlight who is liable for the cost of implementing traffic management measures and who will pay for subsequent lane rental costs.
There should be an agreed procedure on how the contractor advises the concessionaire or operator that a defect has been repaired. One this notice is received, the agreement has to identify who determines that the repair work meets requirements and is complete. A representative of the designer and concessionaire should be involved in this process, while the operator should have the opportunity to comment and attend sign-off inspections as defects have an impact on operation and maintenance. An agreed dispute resolution or arbitration procedure has to be established should a dispute occur over who has responsibility for a defect or the categorisation of a defect.
The design review process has to be open, allowing the operator to see relevant design documents and comment on behalf of the concessionaire, who may not aware of the implications of modifications to operation and maintenance. During the design review process, the operator should provide insight from an asset management perspective and not assume the role of a designer by detailing solutions.
The operator should assist the concessionaire in carrying out the handover process with the contractor, according to a handover procedure covering all aspects of the infrastructure. The basis for accepting or rejecting work should be the specifications amended by the design review or by standard best practice, while the list of issues to control should cover all asset types.
Typical defects encountered at handover include pavement failing to meet minimum performance levels, drainage leaking on structure piles, the non-stabilisation of slopes and safety barrier posts driven through drainage pipes.
Even if an operator has the final approved functional specifications, past experience should be used by developing a simple mini-guide to assist in detecting construction defects during handover inspections. This guide could detail rules and procedures to follow when an operator’s team is engaged in the handover process and list common construction defects encountered on past projects.
Once the operator has been handed control of a project it is crucial that all critical construction defects are identified as early as possible and are brought to the attention of the concessionaire immediately. If defects are left undisclosed for a period of time it can prove problematic in assigning liability to the contractor who may have limited presence on the project or who can argue that there has been insufficient maintenance.
To avoid these problems it is recommended key steps are taken during the initial months of operations. There should be an increase in the number of inspections required on the infrastructure, with sample checks used if it is not practical to inspect all elements of a particular item. Inspections should be increased in adverse weather conditions such as heavy rain to check the performance of drainage, embankments or bridge construction joints.
There should be additional testing of any electrical, electronic or hydraulic equipment and these should include load tests close to maximum capacity for a recommended period of time if possible. Experts should assess specialised equipment or infrastructure when required, while there should be a review of outstanding construction snag items list so that they can be reclassifies as defects.
Developing a standard approach to reporting construction defects is important and should be handled in consultation with the concessionaire and to existing agreement. Once a construction defect is identified, it should be reported to the concessionaire and the category level should be included using a formal process.
A register of reported construction defects should be kept, with each allocated a reference number and dated. In the absence of any action by the concessionaire or the contractor, reporting of construction defects should continue in order to provide a record should future problems occur.
This process should focus on major defects that cannot be handled by routine maintenance and will pose financial risk to the operator. The value of this process can be undermined if there is large scale reporting of minor defects however. Essentially, the concessionaire should use the experience of the operator to highlight potential design or construction flaws, while the contractor is available to correct defects.
From a contractor’s perspective, involving a reliable operator throughout the mobilisation phase, at handover and at the start of service phase should allow speedy updates to the design and clear defects. It is important that the operators understand the financial risks of not identifying defects as early as possible.