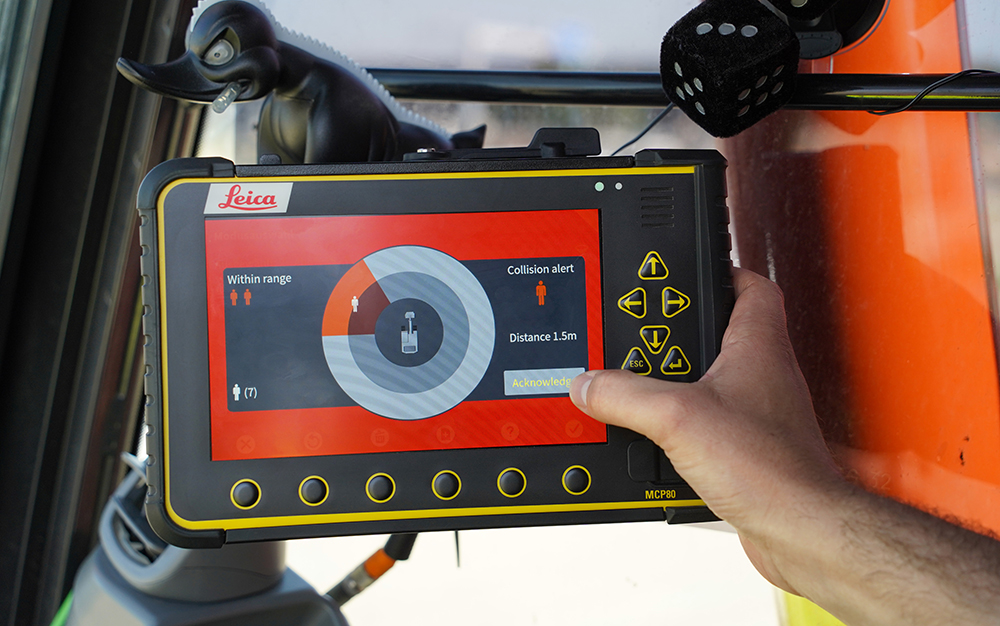
In the USA alone, utility strikes are estimated to cost more than $40 billion a year. And that only applies to what happens beneath the ground.
Every business wants to avoid unnecessary expenses to stay financially healthy. In the world of construction, keeping costs in check is especially vital.
But when it comes to safety, it is not just about money. It is about people, not least because the construction industry remains one of the riskiest sectors globally, with high rates of fatalities and injuries.
Construction workers are three times more likely to be killed and twice as likely to be injured compared to workers in other occupations. That means during a 45-year career, a construction worker has more than a 50% risk of experiencing a disabling injury and a 1-in-2000 chance of being fatally injured on the job. These sobering statistics remind us that safety must be the top priority. Both from a humanitarian and economic point of view, as construction injuries cost nearly twice as much as in other industries.
Technology is the key to site safety culture
By understanding the importance of safety, we can accelerate a culture that prioritises it. Therefore, regular safety training sessions, hazard identification programs, and tool-specific training are mandatory for all personnel on a construction site. Furthermore, it is vital to adapt to the changing world. Over the past decade, digital solutions such as machine control technologies have made operations more accurate, efficient, and sustainable. They also, increasingly, have become a platform for safety awareness solutions directly in the cab. The displayed information gives machine operators a better understanding of their surroundings and can prevent machine-to-people, machine-to-machine, and machine-to-object collisions.
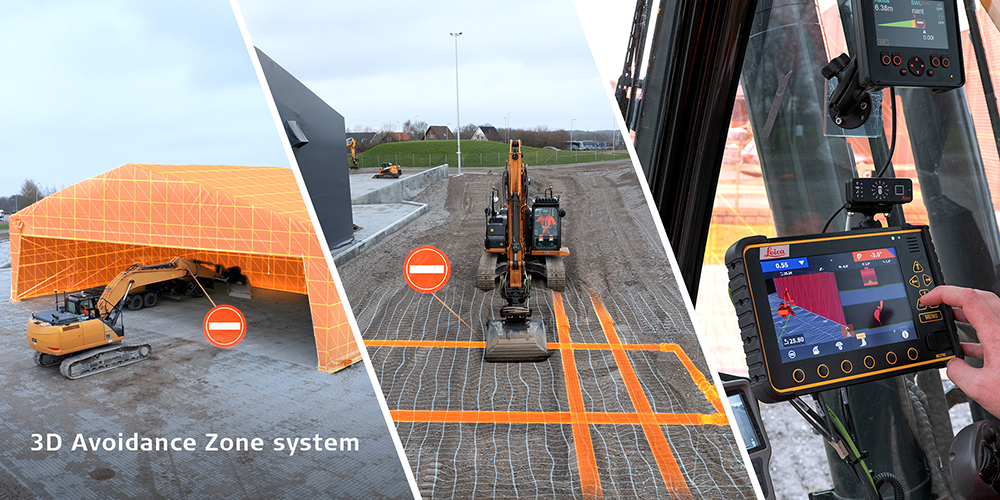
With accurate positioning and measurement of sites, capturing relevant data starts early and continues throughout the project life cycle. The right distances and volumes are essential for construction safety as the information will define later operations through the design model. Reality-capture technologies provide fast access to accurate and holistic digital replications of the actual site conditions. Capturing the data with autonomous laser scanners such as the Leica BLK2FLY additionally minimises risks for construction surveyors as climbing on stockpiles or into excavation pits becomes obsolete. To avoid cutting fiber cables or pipelines, the site conditions must be determined for future above-ground and in-ground operations. Modern utility detection radar systems uncover hidden safety hazards and help avoid major incidents.
As part of Hexagon, Leica Geosystems is a global leader in sensors, software, and autonomous solutions and has more than 200 years of experience in measurement and survey. Based on this expertise, we have developed a whole-solutions portfolio to increase safety awareness on construction sites. Focusing on heavy equipment and moving vehicles, we tackle one of the industry’s most significant hazards, as struck-by incidents consistently rank among the top causes of fatalities in construction.
Protecting people, equipment, and assets with technology
To increase safety awareness, Leica Geosystems and Xwatch Safety Solutions joined forces to enable safer operation of construction equipment. Xwatch’s XW Series of safety systems includes dual-height sensor limitation and height and rated capacity indication (RCI), also called safe load indication (SLI). Integrated with Leica Geosystems 2D and 3D machine control and safety awareness solutions, these technologies prevent an excavator from lifting more than it is allowed per health and safety requirements or local legislation.
The latest combined solution allows users to create or import 3D avoidance zones above and below the surface area directly within the Leica MC1 machine control software. From overhead obstructions to busy areas, existing infrastructure, and underground utilities – approaching these zones triggers the hydraulic functions of the excavator to slow down or even entirely stop.
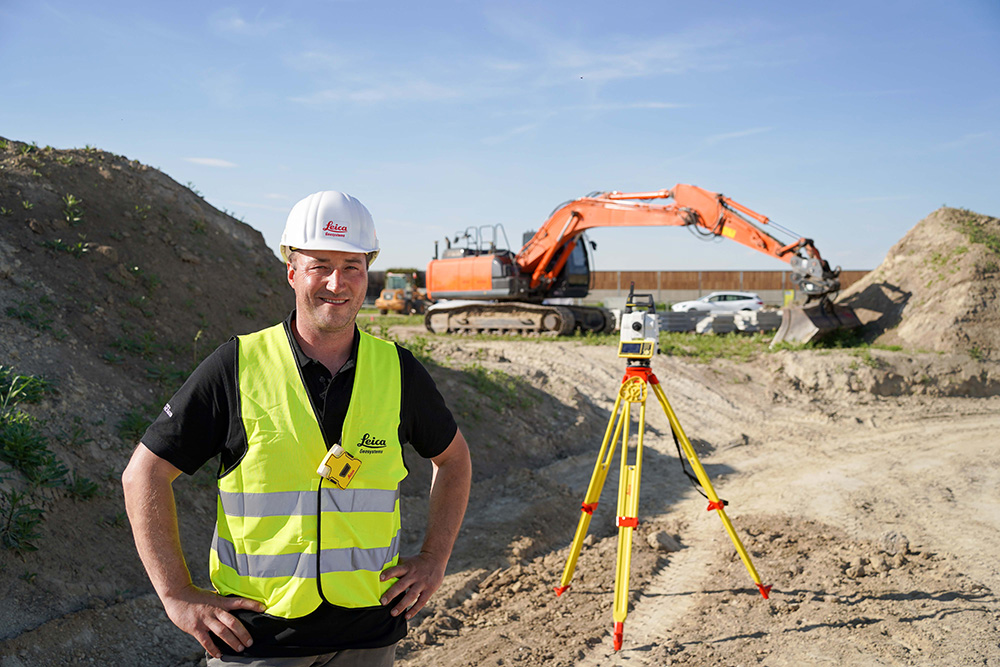
The combined solutions are also integrated with the Personal Alert (PA) solutions. The PA10 combines a tag worn by ground personnel which communicates with anchors on the machines and vehicles to alert all parties if a person is getting too close. The solution provides three configurable alert distances and gives audio, visual, and vibratory feedback to the pedestrian as well as visual and audible feedback to the machine operator or driver.
To enhance this functionality, PA80 integrates the personal alert solution with the Leica MC1 machine control. The machine operator receives visual and audible warnings directly on the in-cabin display. Pedestrians with a PA tag can trigger a panic alert that will notify the machine operator. When a tagged person or object is within a pre-configured zone around the machine, the Xwatch technology allows to proportionately slow down and safely stop the machine.
Adding collision avoidance technology (CAS) to the personal alert solutions brings in machine-to-machine communication, calculating potential collisions within a range of up to 800 meters.
Extending the on-site visibility enhances safety even more. The VA80 (Visual Aid) is a plug-and-play IP camera with a 120 degree field of view. The solution allows operators to capture images and geographic locations of single logged points to increase the as-built documentation. Incidents or hazardous situations can be recorded and exported via USB and Leica ConX. The connection to the cloud-based collaboration platform also improves remote support, as the actual situation can be shared via a live camera feed.
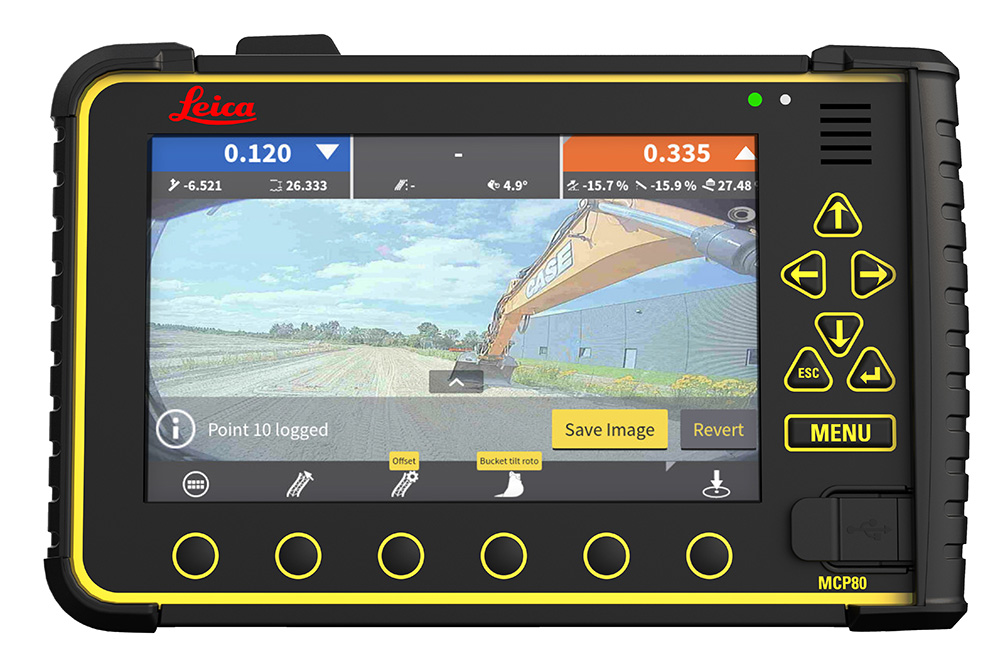
Data-based insights increase safety awareness
Adopting the technology and frequent training helps pedestrians, machine operators, and office personnel to increase safety awareness on-site and minimize incidents. The Leica ConX Safety Awareness Module uses the existing Leica ConX cloud infrastructure to collect data and alerts generated from the Leica iCON PA10, iCON PA80, and CAS solutions. Site managers have a complete overview of incidents and potential incidents. Measuring and analyzing the data will further improve the level of safety over time as it helps to avoid similar situations in the future.
Data can be filtered and exported by event, equipment type, specific machine, and event danger level. Additionally, the module visualizes the selected data on a heatmap, making it easy for safety managers to identify elevated risk areas – or even specific machines at substantial risk.
To enhance office-to-field communications, office personnel can send SOS alerts to all MC1 software users, selected users, or specific machine operators. This way, field crews can be informed about anticipated events that might affect their work or on-site emergencies, like fires, chemical spills, and severe weather. The recipients must acknowledge the notification, which helps identify units that might still be in danger and make quick decisions concerning further actions.
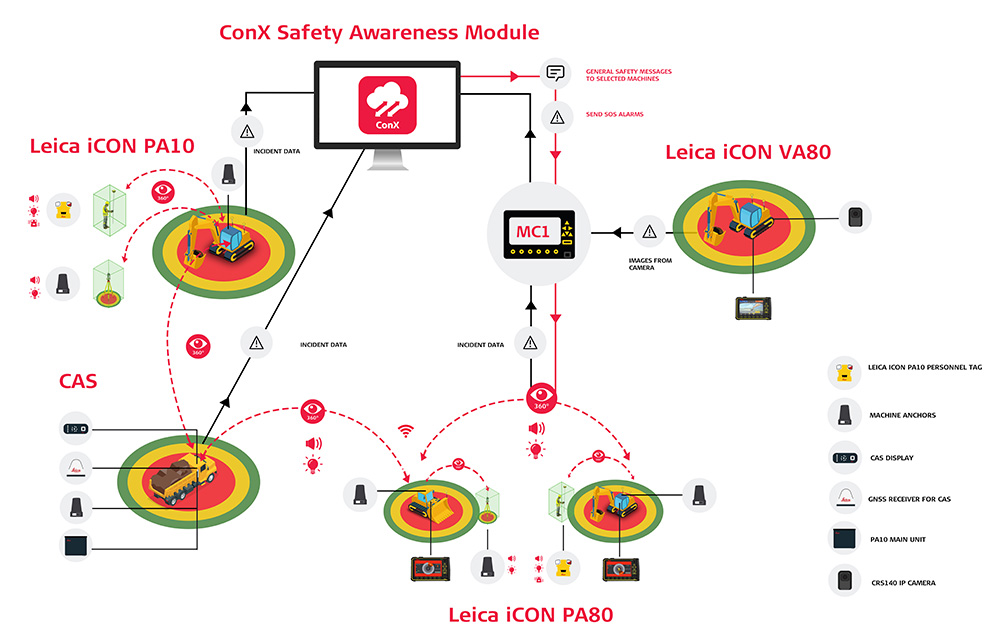
Prevention is better than cure
In this dynamic environment, prevention is certainly better than cure. One of the biggest challenges in overseeing health and safety on a jobsite is the lack of awareness of what is happening on site. While near misses and potential incidents are unlikely to be reported, preventative action can only be taken by knowing about them.
Industry leads and authorities are responsible for cultivating safety awareness and taking appropriate actions. Technology can help mitigate risks and protect human lives, equipment, and assets. It even goes beyond physical safety. Providing peace of mind addresses the psychological aspect of workers’ well-being, fostering a positive work environment and promoting a sense of security and confidence in their daily tasks.
While construction workers benefit from a better perception of their surroundings, office staff are enabled to further improve conditions based on data from real-life situations. It is all about enhancing safety and job satisfaction, improving productivity, and promoting sustainability.
This article was produced in association with Leica Geosystems.
Brad Mullis is product manager at Hexagon’s Machine Control division, responsible for driving the product development of Leica Geosystems’ Safety Awareness portfolio. He joined Leica Geosystems, part of Hexagon, in 2018 as a product specialist and progressed to Product Management in 2020. Prior to that, he worked as a contracts manager and site agent for contractors specialising in urban civils, roadbuilding, bulk earthworks & services. Mullis studied at the Durban University of Technology in South Africa.