Raubex Construction’s new Cat RM500 rotary mixer is proving its worth on a road reclamation work on a South African highway Part of an extensive motorway network some 185km long, South Africa’s ongoing Gauteng Freeway Improvement Project (GIFP) is creating a modern, world-class toll route system. The new road will provide major impetus to socio-economic growth in the country’s most populous and commercially active region.
Being built in stages by the South African National Roads Authority (SANRAL), these r
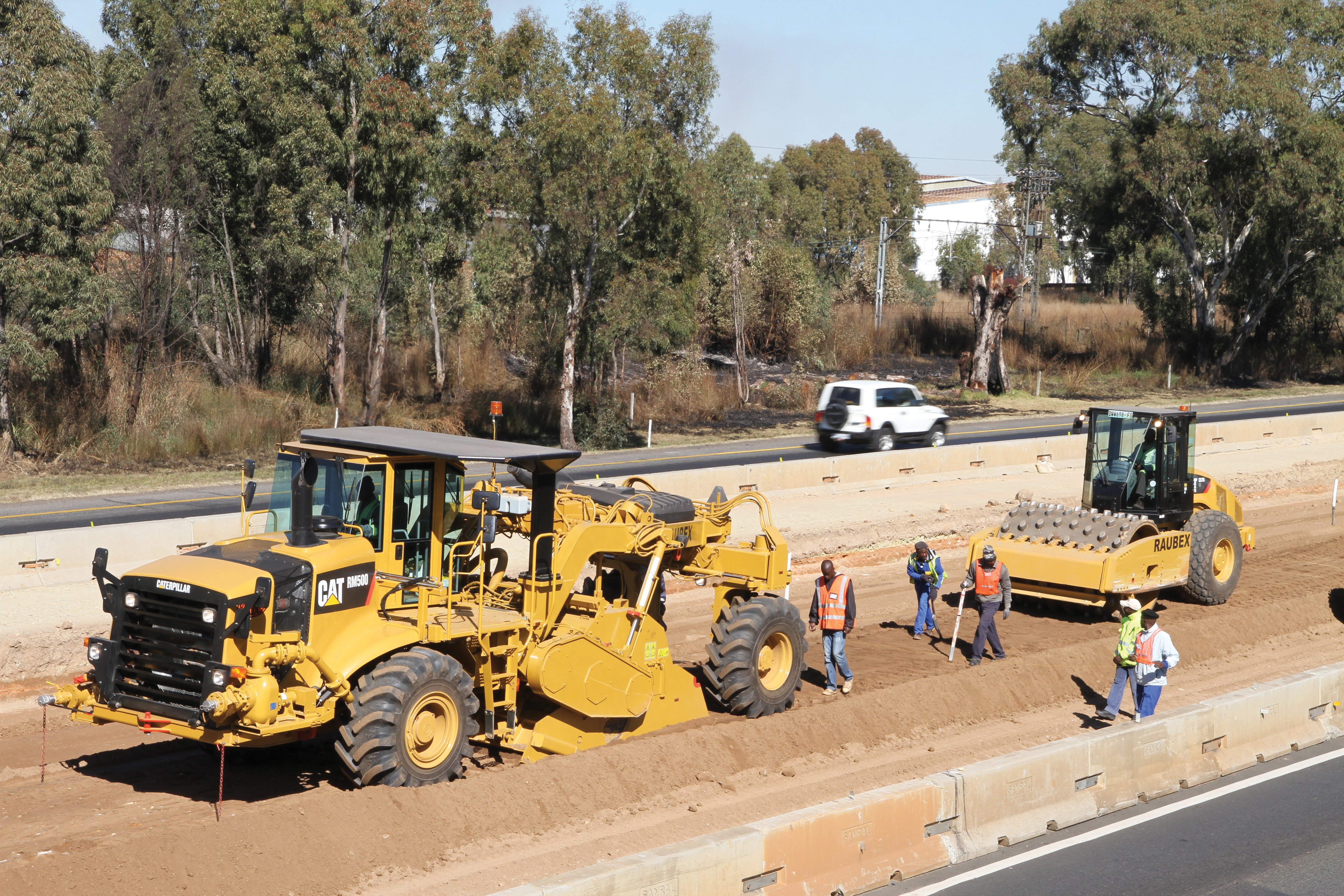
A new Cat RM500 rotary mixer was an early contributor on the jobsite
Raubex Construction’s new CAT's RM500 rotary mixer is proving its worth on a road reclamation work on a South African highway
Part of an extensive motorway network some 185km long, South Africa’s ongoing Gauteng Freeway Improvement Project (GIFP) is creating a modern, world-class toll route system. The new road will provide major impetus to socio-economic growth in the country’s most populous and commercially active region.Being built in stages by the South African National Roads Authority (SANRAL), these roads radiate outward in all directions from Johannesburg and Pretoria’s industrial and residential centres.
Some sections of the road have already been completed, and the results are impressive. Congestion has been replaced by free-flowing traffic, an improvement crucial to the area’s business interests.
National Route 12 (N12) is one of SANRAL’s strategic priorities next in line for improvement. Civil engineering contractor
The existing N12 two-lane road will be replaced by three major new interchanges, successive bridge widenings and three east-bound and three west-bound lanes, which will be placed in an existing median, and a central concrete barrier installed for safety.
Section 19 includes the main access point to Gauteng’s West Rand region, which flows to the agricultural and mining heartland of Mpumalanga Province.
Managing high traffic densities as the roads are realigned is among the challenges.
The durability of the well-travelled road starts with the creation of the base. The N12 design calls for an emulsion and cement stabilisation mix for the sub-base layers. That work is already under way.
“What makes the N12 project particularly noteworthy is that all materials will be worked in-situ or sourced from cuttings that will make way for the new lanes and interchanges along the route,” explained Raubex Construction’s Johan van der Merwe.
“Achieving this requires very complex planning to meet incremental timeframes.”
Some 74 earthmoving machines will be deployed on the N12 site at some time during the project, a high percentage of which are
A new Cat RM500 rotary mixer was an early contributor on the jobsite. The machine handled full-depth reclamation and soil stabilisation for both the new and existing lanes.
Barloworld Equipment’s product manager, Johan Hartman, explained that the Cat RM500 has an operating weight of 28,145kg and is driven by a Cat C15 ACERT engine generating a gross power output of 403kW. This compares with the Cat RM300 operating weight of 24,454kg and gross power delivery of 261kW via its Cat C11 engine. Width of cut on both models is the same at 2,438mm, while the maximum cutting depth is 457mm.
Unlike the RM300 unit, which has a single water pump for optimum moisture content delivery, the RM500 design incorporates both a water and an emulsion pump that are simultaneously monitored in the cab via two separate flow meters. The RM500 pushed two tankers, one carrying 18,000litres of emulsion and the other 18,000litres of water, for the sub-base phase. The emulsion ratio was between 2-3% and cement around 1.5-2%.
With the RM500, Raubex was able to reclaim and stabilise the 300mm sub-base in one pass.
The equipment team on the ETB section will comprise the Cat RM500, the latest generation Cat 140K motor grader, plus Cat CS76 single drum 20tonne vibratory rollers.
In the 300mm sub-base layer, the RM500’s universal rotor-equipped with its 200 carbide-tipped bits arranged in a chevron pattern-came into play in reworking these dense in-situ materials, providing a very high level of material pulverisation and gradation. A three-position mode switch enabled the rotor depth to be controlled manually or automatically to a preset cutting depth to ensure that the engineering design was precisely met.
Most often on the job the machine cut at a depth of 45cm, including a 7cm asphalt surface.
The RM500 mixing chamber features a heavy-duty hood with a large volume capacity to handle deep mixing, and this ensures exact depth control, proper sizing and thorough blending of reclaimed materials.
The production requirements on Section 19 are substantial. Raubex’s RM500 was deployed for the sub-base component, amounting to 135,000m3, while the selected 300mm layer comprised some 102,000m3.
Additionally, the new highway construction will require some 9 million litres of emulsion, 5,000tonnes of cement, 114,000tonnes of BTB, plus 530,000m2 of 35mm AE2 asphalt premix and the equivalent for the 18mm ultra-thin friction course (UTFC) overlay for the final riding surface.
Black-topping will be carried out by Raubex division, Roadmac Surfacing.
The purchase of sub-grade materials from the crushing plant was not required because the machine was able to turn the reclaimed gravel into sub-base material.
“Efficient use of materials and machines will be interdependent on this contract and we have invested in the best possible technologies to meet our completion targets as we steadily transform Section 19 into a multi-lane world-class highway,” van der Merwe added.