Benninghoven, the leading asphalt plant and accessories manufacturer, believes the greater use of Lignite Energy Pulverized (LEP) during asphalt plant production will ensure huge long-term financial savings for plant operators currently using alternative combustibles.
Guy Woodford reports
The claimed impact of LEP on the German asphalt plant market is impressive. As reported in the July-August 2013 issue of World Highways, 80% of all asphalt plants operated in the country are said by LEP Europe-wide
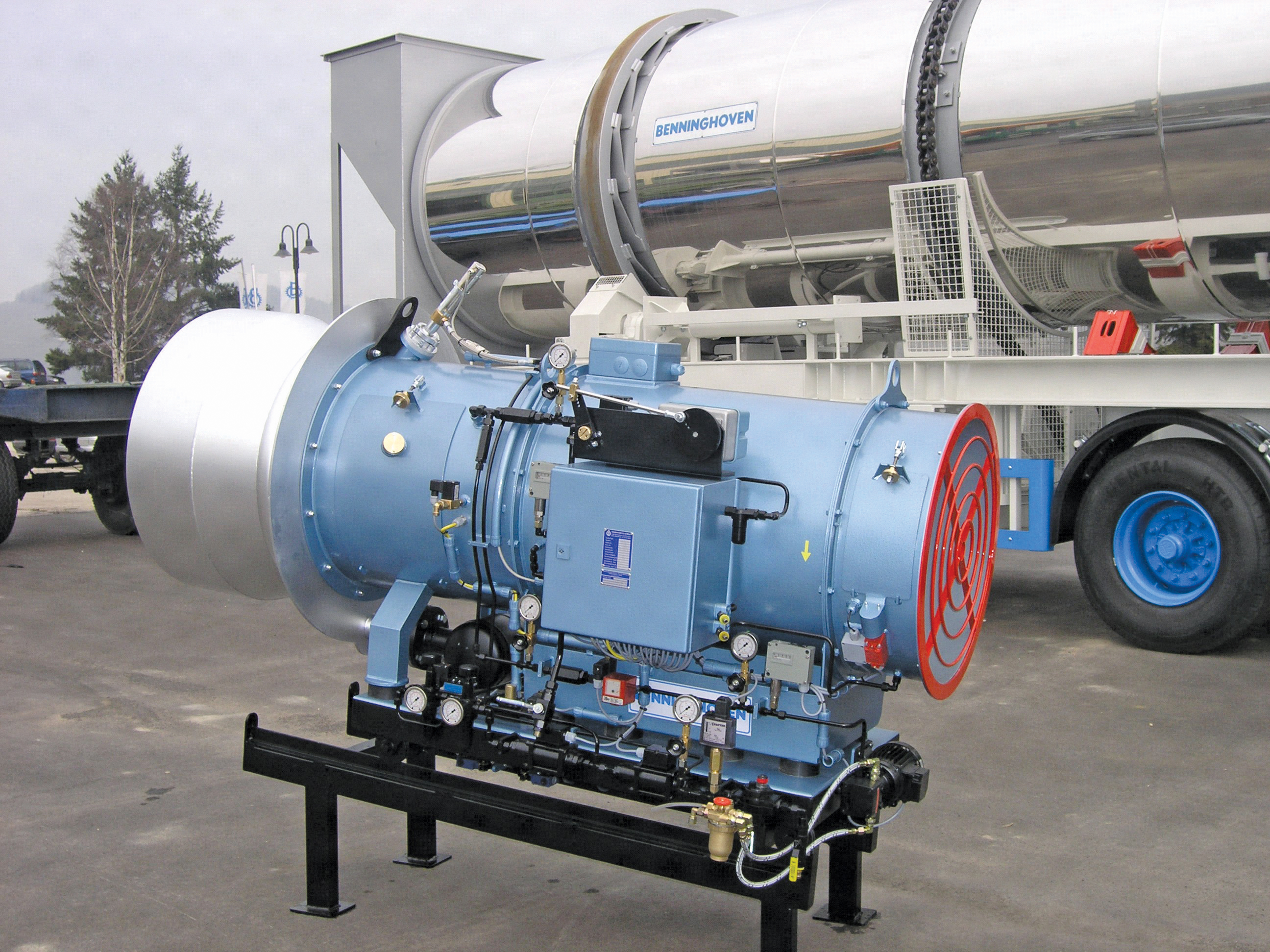
Benninghvoen burner with frequency controlled fan
Benninghoven, the leading asphalt plant and accessories manufacturer, believes the greater use of Lignite Energy Pulverized (LEP) during asphalt plant production will ensure huge long-term financial savings for plant operators currently using alternative combustibles. Guy Woodford reports
The claimed impact of LEP on the German asphalt plant market is impressive. As reported in the July-August 2013 issue ofMany asphalt plant operators elsewhere in Europe, including most in the UK, are yet to switch to LEP to fuel or partly fuel their production. But due to increasing raw material prices, globally renowned asphalt plant manufacturer
Over the past 50 years, Benninghoven has been a renowned manufacturer of burners for all combustion materials that are available on the market: liquid, gaseous and solid. A successful worldwide manufacturer and converter to coal dust firing for the asphalt plant industry, the company has installed more than 600 LEP burners on customer plants.
“Due to the fact that most asphalt mixing plants in Germany together with France, Poland, Czech Republic, Hungary and Romania are already using LEP for the ‘white side’ of drying, it is becoming more and more interesting to also use this coal dust firing for the recycling parallel drums due to increasing energy prices,” said Ralf Port, of Benninghoven. “There is still remarkable potential for conversions in neighbouring European countries, especially in the UK.” Port said some UK plant owners complain about their huge energy costs, making conversions to LEP powered plants attractive.
The supply of LEP to German customers and those in other parts of Europe is guaranteed long-term, said Port, through well-established distribution networks. “Silo trucks with approximately 25 tonnes of content transport LEP to the particular mixing plant. The filling of the storage silo is carried out by the driver of the delivery tanker, similar to the procedure of a supply to a filler storage silo,” he explains. “Delivery to the asphalt plant is carried out by a dosing unit which is positioned underneath the silo outlet. The LEP is transported by a blower using carrier air to the burner and finely dosed according to the plant capacity. Ignition and combustion is supported by a back-up burner during the first stages. Well-engineered combustion technology allows the coal dust flame to burn without back up energy after fail-safe formation.”
A further development, said Port, allows the use of LEP with Recycling-Parallel-Drum-Systems. “Innovative burner technology with frequency inverter control of combustion air, as well as a specially developed burner designed for use with parallel drums, guarantees failure-free operation with this part of the plant,” he added.
Port said plant operators were using larger amounts of reclaimed asphalt as a percentage of asphalt plant production, and is urging operators to compare any financial savings with those achievable through using LEP.