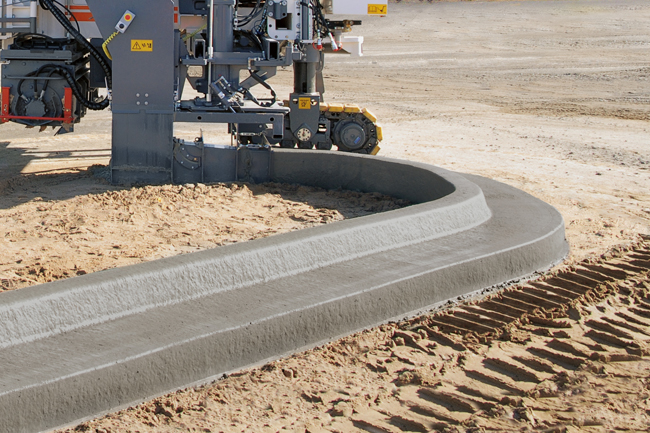
Ed Chenault, president of Fox Enterprises in Richmond, Kentucky said, “Automated control of the paver is the future.”
Fox bought two
The firm is now well used to operating the machine control technology on its slipformers. Chenault said, “The bottom line is that with this technology, on many projects we can install kerb at a lower cost than before. We’ve overcome the challenges that you get with any kind of new technology. Now that we know the machines’ capabilities, we are getting more efficient in their use. We’re developing more and more opportunities to put them to work, and are pursuing other contractors that are using similar technologies, because they understand the advantage of competitive pricing with higher technology.”
Fox often serves as a subcontractor, which was the case when it was placing kerbs, gutters and islands in a reconstructed parking lot for a major manufacturer outside Lexington, Kentucky. The firm was working on a stormwater improvement and parking lot expansion. “Using AutoPilot, we installed a large number of trench drains, and were placing kerb and gutter to tie into the trench drains,” he said.
“We have more success with the tight radius for curbs using AutoPilot than we do with stringline.” To use AutoPilot, Fox has to select the right project and mate the AutoPilot to the project, Chenault said. “It depends on the general contractor we are following,” he continued. “The general has to buy in to the utilisation of the technology.”
The Wirtgen AutoPilot is a 3D control system for use with the Wirtgen SP 15i and SP 25i slipform pavers. It is a system for the construction of poured in-place concrete profiles, such as kerbs or safety barriers, in offset application. GPS-based, the system ensures precision and efficiency and can handle straight profiles, complex curved profile paths, or closed profile configurations. The AutoPilot enables fully automatic, high-quality paving at radii of just 600mm and without the use of stringlines. This dispenses with surveying and also with the installation and removal of stringlines. The Wirtgen AutoPilot also automatically negotiates any obstacles on the job site, such as manhole covers.
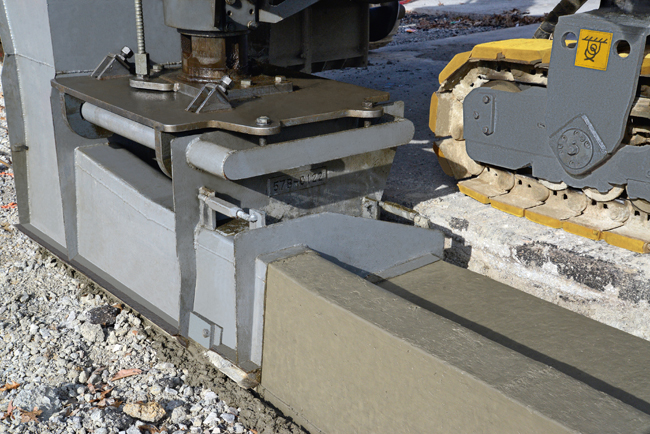
Establishing a digital terrain model is not required as programming of the profile path or profile configuration is completed on site. The system comprises a computer integrated in the machine as well as a control panel. Two GPS receivers, mounted on masts on the machine, communicate with an additional GPS reference station positioned on site. After positioning the total station and laser on the job site, the slipform paver is taken to the specified starting position and heading. Parameters are directly entered into the system via the rotary push-button and function keys at the clearly structured control screen.
Programming the Wirtgen AutoPilot is said to be quick. In a first step, the machine operator selects a profile configuration at the control panel. Next, he enters length, width and radius of the configuration to establish the steering path of the slipform paver. The starting point is determined in a third step, followed by machine level and elevation profile. In a final step, the machine operator determines the cross slope.
A laser sensor or sonic sensor mounted on the slipform paver scans the ground surface to ensure precise level control. The fully automatic paving operation commences. Previously programmed profile configurations can be saved and retrieved as required. The operator is in full control during the entire process. He can intervene in the automatic paving operation at any time if necessary, for example, to modify the machine’s level and angle of incline.